“Which type of filter failure mode should you be most concerned about: plugging, channeling, fatigue cracks or media migration?”
Each of these failure types has a distinct failure mechanism and method of detection. While they all are bad, they can be prevented or detected with simple system analysis.
Plugging
Filter plugging occurs when oil has circulated in the system for too long without a change or other routine examination. The filter is saturated or covered in carbon sludge or other failure products like varnish. Oil analysis may show no trend indicating this type of failure, but the system will register an increased pressure differential across the filter, as the flow path is all but stopped. Routine changes of the filter and in the oil system will help to prevent this type of failure.
Channeling
Channeling, also known as media pore erosion, is where the filter weave or screen is bombarded by high-speed abrasive particles, such as sand or wear metal. These particles slowly erode the filter material or lodge in the filter pores and force themselves through, irreversibly expanding the pores. This usually can be prevented by checking and maintaining the system’s gaskets and seals. Failure can be identified in analysis reports by observing an upward trend in the number of large particles in the particle count test.
Fatigue Cracking
Fatigue cracking, also called media matrix deformation, is where the filter weave warps due to operational stresses, such as violent cycle shifts of pressure and flow. Some forms of woven filter media can be reinforced with simple metal screens. In other cases, the filter may need to move inside the system, possibly even “offline” into a kidney-loop circulating line to keep the filter away from the higher pressures. This mode of failure will restrict oil flow through the filter and force a bypass around it, resulting in an upward trend in the total particle count on analysis reports.
Media Migration
Media migration, or media matrix rupture, is similar to fatigue cracking, but instead of warping the filter and bypassing it, the high pressure/flow transient partially destroys the filter and ruptures the material out of the filter structure. In addition to normal contaminants not being caught in the filter, new contaminants are introduced in the form of the failed filter pieces circulating through the system. Plus, anything previously captured by the filter is now at risk of being re-released. Rupture problems only increase in the presence of abrasive particles such as sand or wear metal. Failure can be identified by the oil system showing low or no pressure drop across the filter and oil analysis revealing an increase in the total particle count.
Media migration is the worst type of filter failure, as it essentially is the other three modes happening simultaneously. It can be the most difficult to immediately detect, and the introduction of large, broken filter pieces into the system can cause catastrophic damage to downstream components. You can prevent this failure mode by conducting daily visual inspections of the system, observing pressure and flow behavior, properly analyzing oil samples, and performing routine maintenance activities like inspecting and changing the oil and installed filters.
References
Toms, L.A. (2008). Machinery Oil Analysis: Methods, Automation & Benefits
Fitch, B. (June 2013). “Anatomy of an Oil Filter.” Machinery Lubrication
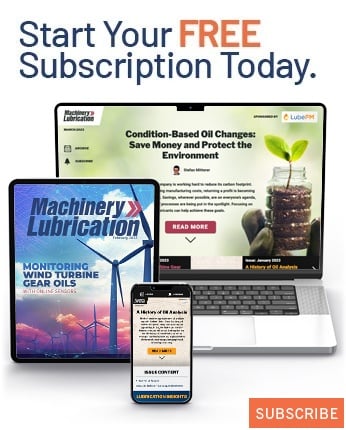