For its annual Lube Room Challenge, Machinery Lubrication recently invited readers to share evidence of how their lubricant storage rooms have been transformed to best practices. While several companies were proud to show how they maintain clean, cool, dry and well-identified lubricants, one entry stood out among the rest.
2019 Winner: Ingredion Canada
The Ingredion Canada plant in Cardinal, Ontario, made an impressive transformation in the way it manages lubrication. The site had a history of lubrication-related failures causing high-cost repairs, which negatively impacted the maintenance budget and process uptime.
The condition of the old lube room and lubricants was dismal at best. The room was an uncontrolled walk-through that had process lines running through it. These lines opened and dumped on top of new oil drums. Oil was dispensed unfiltered by hand pumps into a combination of plastic and/or galvanized transfer containers which were not color-coded.
The maintenance manager at the time realized the need to change how lubrication was being managed. Proper lubricant storage and handling would be a significant part of this change. The plant took advantage of a capital project that needed the old area for a new process. This provided the opportunity for a new lubrication building. Maintenance also purchased new storage units and transfer containers for the new building.
Next, two lubrication technicians were selected and dedicated to lubrication full time. The focus then shifted to training, as the technicians were required to obtain Level I Machine Lubrication Technician (MLT I) and ultrasound certifications.
The condition of the lube room now is described by auditors and assessors as best in class or world class. The clean, climate-controlled building is dedicated solely to lubricant storage and dispensing, and only trained individuals have access to it. Color-coded bulk storage units filter oil as it comes in and when it goes out. Oil is dispensed into color-coded plastic transfer containers that are matched to the bulk storage unit and at the point of use.
The new storage cabinets keep the transfer containers, grease, grease guns and sampling equipment well-organized. An office/lab area has also been designed for the lubrication technicians to conduct viscosity tests and manage their daily work.
Uptime, budget savings and the culture around lubrication have been the most important results. The facility has now had its lubrication center in service for seven years, and it continually is being improved. However, the technicians’ dedication to keeping the room in audit-ready shape remains steadfast.
Honorable Mentions
Novelis
The Novelis plant in Terre Haute, Indiana, is an aluminum-rolling facility. When two of its staff members attended a machinery lubrication training course, it sparked the mill’s journey to transform its lubricant storage and handling practices, which were contributing to major equipment failures.
Oils and greases had been stored everywhere and in all types of containers. Milk cartons were even utilized as dispensing containers. By disposing of 1,200 gallons of waste oil and 1,200 pounds of grease, as well as 45 empty barrels, totes and kegs, the plant freed up 10,000 square feet of storage space.
A list of necessary lubricants was compiled. Those no longer needed were discarded, while the others were organized into a central storage area. Eventually, the mill was able to consolidate from 50 different oils and greases to 19 lubricants, and from 10 vendors to two suppliers.
A new lube room also allowed better control of the storage climate. Previously, some bulk lubricants had been stored outdoors, exposing them to moisture, debris and a wide range of temperatures. Sealable and refillable containers were procured, along with filter carts and bulk storage with filtration, to help combat this problem. A filtration standard was then established to ensure lubricant integrity.
A culture change helped all employees understand that hydraulic oil leaks were no longer acceptable. This resulted in a 75 percent reduction in leaks in just one year. By keeping the hydraulic oil clean, cool and dry, the oil’s service life also increased.
Operational checks of the hydraulic systems have been implemented to alert the plant when a filter needs to be changed or when temperatures rise too high. Air-cooled heat exchangers were installed to prevent water from entering the systems. Adding desiccant breathers to the reservoirs has also helped to keep out moisture.
Finally, an audit was conducted to create a lube point list. With this list, a task-routing tool was used to catalog each lube point with a schedule, specific lubricant and necessary practices for the task. The tool also allows the schedule to be adjusted based on calculations that can identify the proper amount and timing for grease applications. The results have been significant cost savings in oil and grease expenses.
Resolute Forest Products
A few years ago, the Resolute Forest Products’ Saint‐Felicien pulp and paper mill in Quebec, Canada, launched an initiative to increase the reliability of its entire kraft mill. The goals included improving the lubrication program and lube room storage and handling practices.
Before the modifications were made, lubricant drums were placed on the ground, with some on racks to fill containers that had no identification. Four filtration units were used for any type of oil. Tools and other items were placed in old cabinets with no identification or organization. The oil from the supplier was not filtered when it was received at the mill nor before being transferred to the equipment. There was also no identification on the equipment for the type of oil or grease that was required. Many failures occurred that were related to the amount and quality of grease pumped into the bearings.
To kickstart its journey, the mill worked with expert consultants to audit its lubrication program, establish a baseline and develop a plan to improve the current situation. Resolute’s management bought into the idea and the cost-benefit analysis.
In 2017, new lubrication equipment was purchased, and the lube room upgrade began. The entire shop was painted, including the floor, walls, doors, fire lines and roof. New light-emitting diode (LED) lighting was installed, and electrical plugs were added for the new equipment. Nine new filter units were procured, with one for each type of oil in use at the mill.
A new distribution center allows oil to be filtered before containers are filled. Four conveyors have been installed on the floor for drum storage and to ensure proper first-in/first-out practices. New cabinets were acquired with identification of what is inside. All equipment now has an identification tag that shows the type of lubricant required.
The mill has also worked with its team of dedicated professionals to develop their skills in lubrication and contamination control. Personnel were trained to use ultrasonic grease guns for lubricating bearings and on lubrication best practices. They now take oil samples every four months and follow up with corrective actions autonomously.
All the lubrication and reliability team members are proud of the changes that have been made. They recently had the honor of presenting their program to visitors from other mills who came to see what had been accomplished. All the improvements have helped the mill reach and surpass the oil cleanliness targets that had been established. This is significant considering the mill had been viewed as the worst Resolute Forest Products mill in 2015 and now is seen as the best.
ZT Kruszwica
ZT Kruszwica is Poland’s largest processor of oil seeds and maker of vegetable fats. Its Brzeg production plant has more than 1,300 machines and components as well as multiple departments, including crushing, extraction, refinery, bottling, maintenance and a boiler house. When the decision was made to create centralized lubricant storage for all departments in one location, it was determined that only a limited number of people should have access to the space. These individuals would be responsible for the warehouse and be required to strictly adhere to the corresponding rules.
In 2017, construction of the warehouse began. During construction, scrap and materials from demolished buildings were used. This helped to minimize costs and waste. Many items from old, liquidated warehouses were utilized to equip the building, such as sump trays, drum carts, etc. An old control cabinet was converted into a tool cabinet to store tools, grease nipples, protective caps and grease caddies. A refrigerated cabinet was transformed to keep industrial chemicals. Rollers from a conveyor belt were employed to build a device for storing oil drums in a horizontal position.
Other updates included implementing waste gearbox oil containers and using colored caps to keep grease nipples clean and indicate the grease brand. The plant also connected its “lubrication cards” with its computerized maintenance management system (CMMS). These cards provide details on the equipment manufacturer, machine type, serial number, department, lubrication points, lubricant type, lubricant amount and lubrication frequency. To date, nearly 900 cards have been completed.
The plant’s lubrication schedule is now optimized, and visual inspection routes have been established. This has allowed for improved reliability and equipment health.
Walter Rau
The Walter Rau food-processing plant in Hilter, Germany, manufactures high-quality margarine products, edible fats and oils. A few years ago, the plant addressed its lube room, which was very messy and unorganized. The space had been used to store a wide variety of lubricant types, many of which hadn’t been needed in quite some time. Most of the oil barrels in the room were also dirty and slippery.
Once the room was cleared, plant personnel identified which lubricants would be needed going forward. Every barrel was then cleaned and returned to the room. Finally, everything was labeled.
Now, the only lubricants in the room are those that are truly needed for the machines in the plant. Every lubricant has a designated place, and everything is correctly labeled. There are also new safety signs and lubricant descriptions. The result not only has been a cleaner lube room, but personnel can also find lubricants much quicker.
JSW Steel
JSW Steel is an integrated steel manufacturer and one of the fastest growing companies in India. In the company’s steel melt shop at its Dolvi Works plant, heat, dust and water contamination are the main challenges to maintaining and sustaining the lubrication system. Unfortunately, poor lubricant storage and handling practices led to increased contamination issues. Grease drums were kept open and included no visible indicators of the lubricant level. Pneumatic grease pumps were filled manually by hand, while empty hydraulic drums were stored anywhere that didn’t hamper the workplace.
When these issues became apparent, the plant decided it was time to make improvements to its lube room. Each grease drum now has a cover to help prevent contamination. Level indicators on the drum covers show when the grease level is dropping. An auto-refilling system is used to fill the pneumatic grease pumps, and empty hydraulic drums are stored in designated places. Operator-friendly standards for cleaning, lubrication, inspection and tightening have also been implemented. These changes have had a positive impact on the plant and help support the organization’s desire to improve and upgrade the quality of construction in India.
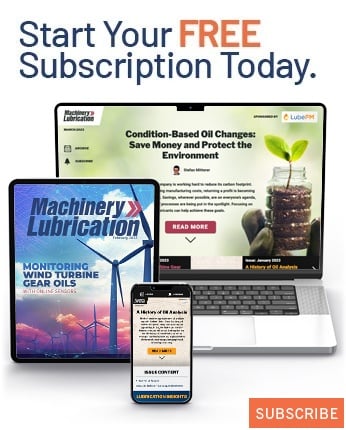