Compressors are an integral part of almost every manufacturing facility. Commonly referred to as the heart of any air or gas system, these assets require special attention, particularly their lubrication. To comprehend the vital role lubrication plays in compressors, you must first understand their function as well as the effects of the system on the lubricant, which lubricant to select and what oil analysis tests should be performed.
Compressor Types and Functions
Many different compressor types are available, but their primary role is almost always the same. Compressors are designed to intensify the pressure of a gas by reducing its overall volume. In simplified terms, one can think of a compressor as a gas-like pump. The functionality is basically the same, with the main difference being that a compressor reduces volume and moves gas through a system, while a pump simply pressurizes and transports liquid through a system.
Compressors can be divided into two general categories: positive displacement and dynamic. Rotary, diaphragm and reciprocating compressors fall under the positive-displacement classification. Rotary compressors function by forcing gases into smaller spaces through screws, lobes or vanes, while diaphragm compressors work by compressing gas through the movement of a membrane. Reciprocating compressors compress gas through a piston or series of pistons driven by a crankshaft.
Centrifugal, mixed-flow and axial compressors are in the dynamic category. A centrifugal compressor functions by compressing gas using a rotating disk in a formed housing. A mixed-flow compressor works similar to a centrifugal compressor but drives flow axially rather than radially. Axial compressors create compression through a series of airfoils.
Effects on Lubricants
Prior to the selection of a compressor lubricant, one of the primary factors to consider is the type of strain the lubricant may be subjected to while in service. Typically, lubricant stressors in compressors include moisture, extreme heat, compressed gas and air, metal particles, gas solubility, and hot discharge surfaces.
Keep in mind that when gas is compressed, it can have adverse effects on the lubricant and result in a noticeable decline in viscosity along with evaporation, oxidation, carbon depositing and condensation from moisture accumulation.
Once you are aware of the key concerns that may be introduced to the lubricant, you can use this information to narrow your selection for an ideal compressor lubricant. Characteristics of a strong candidate lubricant would include good oxidation stability, anti-wear and corrosion inhibitor additives, and demulsibility properties. Synthetic base stocks may also perform better in wider temperature ranges.
Lubricant Selection
Ensuring you have the proper lubricant will be critical in the health of the compressor. The first step is to reference the recommendations from the original equipment manufacturer (OEM). Compressor lubricant viscosities and the internal components being lubricated can vary greatly based on the type of compressor. The manufacturer’s suggestions can provide a good starting point.
Next, consider the gas being compressed, as it can significantly affect the lubricant. Air compression may lead to issues with elevated lubricant temperatures. Hydrocarbon gases tend to dissolve lubricants and, in turn, gradually lower the viscosity.
Chemically inert gases such as carbon dioxide and ammonia may react with the lubricant and decrease the viscosity as well as create soaps in the system. Chemically active gases like oxygen, chlorine, sulfur dioxide and hydrogen sulfide can form tacky deposits or become extremely corrosive when too much moisture is in the lubricant.
You should also take into account the environment to which the compressor lubricant is subjected. This may include the ambient temperature, operating temperature, surrounding airborne contaminants, whether the compressor is inside and covered or outside and exposed to inclement weather, as well as the industry in which it is employed.
Compressors frequently use synthetic lubricants based on the OEM’s recommendation. Equipment manufacturers often require the use of their branded lubricants as a condition of the warranty. In these cases, you may want to wait until after the warranty period has expired to make a lubricant change.
If your application currently utilizes a mineral-based lubricant, switching to a synthetic must be justified, as this often will be more expensive. Of course, if your oil analysis reports are indicating specific concerns, a synthetic lubricant can be a good option. However, be sure you are not just addressing the symptoms of a problem but rather resolving the root causes in the system.
Which synthetic lubricants make the most sense in a compressor application? Typically, polyalkylene glycols (PAGs), polyalphaolefins (POAs), some diesters and polyolesters are used. Which of these synthetics to choose will depend on the lubricant you are switching from as well as the application.
Featuring oxidation resistance and a long life, polyalphaolefins generally are a suitable replacement for mineral oils. Non-water-soluble polyalkylene glycols offer good solubility to help keep compressors clean. Some esters have even better solubility than PAGs but can struggle with excessive moisture in the system.
An example of oil analysis test slates and alarm limits for centrifugal compressors.
Oil Analysis Tests
A multitude of tests can be performed on an oil sample, so it is imperative to be critical when selecting these tests and the sampling frequencies. Testing should cover three primary oil analysis categories: the lubricant’s fluid properties, the presence of contaminants in the lubrication system and any wear debris from the machine.
Depending on the type of compressor, there may be slight modifications in the test slate, but generally it is common to see viscosity, elemental analysis, Fourier transform infrared (FTIR) spectroscopy, acid number, varnish potential, rotating pressure vessel oxidation test (RPVOT) and demulsibility tests recommended for assessing the lubricant’s fluid properties.
Fluid contaminant tests for compressors likely will include appearance, FTIR and elemental analysis, while the only routine test from a wear debris standpoint would be elemental analysis. An example of oil analysis test slates and alarm limits for centrifugal compressors is shown above.
Because certain tests can assess multiple concerns, some will appear in different categories. For example, elemental analysis may catch additive depletion rates from a fluid property perspective, while component fragments from wear debris analysis or FTIR may identify oxidation or moisture as a fluid contaminant.
Alarm limits often are set as defaults by the laboratory, and most plants never question their merit. You should review and verify that these limits are defined to match your reliability objectives. As you develop your program, you may even want to consider changing the limits. Frequently, alarm limits start out a bit high and change over time due to more aggressive cleanliness targets, filtration and contamination control.
Understanding Compressor Lubrication
In regard to their lubrication, compressors can seem somewhat complex. The better you and your team understand a compressor’s function, the effects of the system on the lubricant, which lubricant should be selected and what oil analysis tests should be conducted, the better your chances of maintaining and enhancing the health of your equipment.
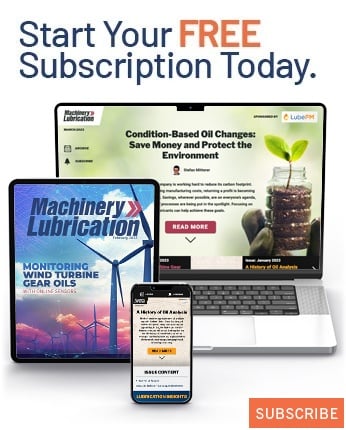