By this point in the Lubricant Lifecycle Stages, it quickly becomes evident that there are numerous variables going into each lubrication decision. Even the most granular lubrication topics can easily become complex with endless factors. But your time is valuable. It isn’t always the best idea to “go down that rabbit hole.” We must use the right tools and proven methodologies to help make these lubrication decisions more efficiently, prioritize them and keep us on the right track.
Ascend™ was created to organize these lubrication decisions from a holistic perspective. The Ascend Chart puts this into a clear visual. It is a reminder of where efforts need to be focused to avoid losing sight of the full lifecycle of a lubricant and the factors that affect it. The end goal of all this is to achieve key reliability objectives and increase overall profitability. The lifecycle of a lubricant starts with Lubricant Selection, followed by a Reception & Storage, Handling & Application, Contamination Control (incl. Reconditioning) and Condition Monitoring (incl. Oil Analysis and Troubleshooting). Last, but not least, is Energy Conservation, Health & The Environmental Impact.
Part of this final stage logically focuses on the end-of-life of a lubricant, how we handle and dispose of used oil and related materials. Other topics included in this stage have dotted lines to many other factors across the Ascend™ Chart, such as health and safety. All of this will be discussed. This Lifecycle Stage has five Factors, listed below.
The first two are part of the Platform Level, the second two are part of the Management Level and the final Factor is dedicated to Key Performance Indicators.
Platform Level
During the lubricant selection process in the first stage, there are many fundamental considerations regarding the selection of the base oil, viscosity, thickener type, oxidation resistance, thermal stability and so on. These are determined based on the tribological needs of the machines. Nevertheless, each lubricant in application has ancillary attributes that can make crucial impacts on energy conservation, the health of individuals and the environment. The associated risk to these considerations has the opportunity to limit or even control the selection of the lubricants all together. Let’s first take into consideration Energy Conservation.
Energy Conservation
Minimizing or eliminating friction is a key function of the lubricant. When the incorrect lubricant is selected or when the lubricant isn’t properly applied (either manually or through an automatic delivery mechanism), the machine has to work harder and consume more energy to overcome unnecessary friction. Take incorrect viscosity for example: both too high a viscosity and too low a viscosity can result in increased energy consumed and waste.
Aside from extending machine life by using a properly selected lubricant, there is a direct opportunity to conserve energy. The driving component of an asset, typically an electric motor, has to work hard enough to keep a shaft rotating with enough torque to overcome all sources of friction. A steady balance of lubricant properties during lubricant selection and deploying various condition monitoring strategies can help keep this on track. Additionally, the delivery method of a lubricant to the frictional surfaces is a factor itself. For example, in a bearing that is manually regreased, the interval should be thoughtfully calculated for optimization. Or alternatively, an automatic method may be deployed for more frequent and precise grease delivery at lower volumes. This holds true for other lubricated components. Energy conservation depends greatly on the selection lubricants and the lubrication system. So whether it is oil or grease, synthetic or mineral, manually or automatically lubricated, balance is key.
Health & Environment
Next, the impact on the health of people or the impact on the environment should be reviewed when selecting lubricants and lubrication systems. The level of risk in this case could very well be more relevant than considerations of machine life extension or general cost savings. As we estimate risk to health and the environment, it is a combination of the probability of occurrence and the resulting consequences. If lubricants selected have a known negative effect when in contact with people or the environment, this would be the consequence. These would include attributes such as toxicity, microbial growth, combustibility, biodegradability and high temperature, among others. The greater the negative effect, the greater the consequence.
The probability is determined based the likelihood of lubricant exposure. If the combination of the consequence and probability are high, the overall risk to people or the environment could be high. Additionally, the lubrication system itself should be considered directly as a possible safety risk (also discussed in the Reception & Storage Stage). Such is the case on lubrication systems with pressurized fluids, electrical energy, mechanical energy, etc.
Therefore, careful selection of either the lubricant with less negative effects or a lubrication system that is more effective at minimizing these negative impacts is key. Addressing the Energy Conservation, Health & the Environment factor should be foundational to a lubrication program, hence why it is part of the Platform level.
Storage & Disposal of Used Oil & Materials
As lubricants degrade, they are disposed of unless they are deemed suitable for reconditioning (overviewed in the Contamination Control and Reconditioning Stage). Typically, after a drain or purge of used lubricant from a machine, the used lubricant should be brought to a well-labeled storage container until it is removed offsite by an appropriate contractor. Other materials, such as filters and rags, may also be contaminated with this used lubricant and should also be handled similarly and appropriately.
Just like any other lubricant and storage practices, there are various risks that could be associated with used lubricants and a range of actions needed to minimize the risks. Having careful steps and procedures for these activities is important. In addition to these considerations as general guidelines, many organizations have policies and rules that must be followed. Outside of those, there are local and even federal laws and regulations regarding the handling and storage of these used lubricants to consider. This could include regulatory bodies such as the EPA, OSHA, MSHA and others.
Management Level Leakage Management
One of the silent killers at a plant is the quiet, steady leak of oil from a machine. Such leaks can often go unnoticed, uncorrected and often result in lubricant starvation. This is why daily inspections on lubricated components and installing quality, easily inspected sight glasses are so important. Some equipment, if critical enough, may even require built-in level monitors that provide real-time feedback if a leak occurs. Nevertheless, when leaks do occur, having procedures to handle oil leaks is important to minimize the risk to people, the risk to the environment and unnecessary costs.
Large or small, leaks can become costly fast. Here are some costs associated to a leak:
In addition to monitoring for leaks, certain steps should be followed when leaks do occur. This may include labels, used of dike materials and prioritized/scheduled remediation actions. Prioritization could consider equipment criticality, volume (and cost) of the lubricant and ease of repair. After leaks are remedied, a detailed leak report should be documented, including any findings from a Root Cause Analysis performed to avoid a repeated event.
Training
Leakage Management protocols help minimize risk. To accomplish this, role-specific training is required. This is also true for Handling Used Oil & Materials and managing all aspects of Energy Conservation, Health and Environment. All plant individuals will need some core training to ensure there is awareness to the risk to human health a lubricant may pose. For those handling the lubricant and making lubricant selection decisions, such as lubrication technicians, reliability engineers and lubrication program managers, additional training should be expected for leak management procedures and the impact lubricants may play in energy conservation or the environment.
Key Performance Indicators (KPIs)
Making good lubrication decisions becomes much easier when key observations from past activities are applied to future considerations. Monitoring performance variables and establishing these as metrics help with this process and creates a pace for continuous improvement. The last factor in this stage are the KPIs for Energy Conservation, Health & Environment. These will include various leading and lagging indicators on how well the plant is making improvements. For example, there could be metrics to compare the volume of lubricants applied to machines versus the volume of lubricant disposed. Over time, the difference indicates how much lubricant has leaked or been otherwise consumed.
Simply tracking oil usage and disposal can be trended to help monitor for efficiency gains and waste reduction as lubrication practices are optimized to require less lubricant changeouts. Similarly, other KPIs should be considered for monitoring safe disposal practices and energy conservation. Marking events where lubricants were known to negatively impact personnel health or the environment can also serve as a learning opportunity for future prevention.
In Conclusion of the Lubricant Lifecycle
Lubricant is a key component of machine design. In addition, what lubricants are used and other lubrication decisions can make critical impacts on cost, labor, uptime and safety through their effects on energy conservation, health of people, the environment, leak management and more. It’s better to keep track of processes and policies to ensure proper practices are being followed. Like with other Factors in the Ascend Chart and throughout the lifecycle of a lubricant, we must document these concerns in a Corporate Lubrication Standards Manual and present it openly for clear communication. The more care and consideration you put into lubrication decisions, the more equipment reliability and overall profitability will increase.
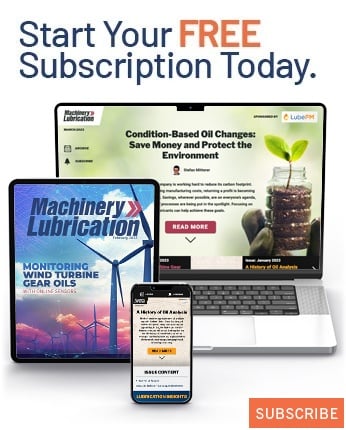