Wind turbines are notoriously difficult to monitor due to several environmental and mechanical factors. First, the drivetrain consists of elements that change load, speed and torque quickly and continuously as the winds change speed and direction. The gearbox internal elements range from 18 rpm planetary gears to 1400 rpm helical gears. In addition to the turbine mechanics themselves, the distributed nature of wind farms, along with the 250-foot (or higher) climb to access the system, makes remote monitoring an efficient choice.
Early wind turbines had no diagnostic systems included by Original Equipment Manufacturers (OEMs). It is now common to rely on annual or semi-annual oil samples from the gearbox sump using spectrographic iron analysis to alert operators of developing problems. This periodic monitoring is not always successful at avoiding problems, though. The chances of sampling the turbine at the optimum time to detect a problem are unlikely.
The Need for Continuous Condition Monitoring
The costly repairs and potential for significant downtime associated with interval-based monitoring are both excellent reasons for considering a continuous condition monitoring system in this application. The turbines already had a data network for monitoring their basic status, power output and temperatures. These networks could easily be leveraged to add additional sensor technologies to continuously monitor drivetrain health and condition. To introduce continuous condition-monitoring to the process, two basic technology types were considered: vibration-based systems and wear debris technology.
Option 1: Vibration
Since many wind operators had roots in the conventional power plant space, vibration-based systems were familiar to operators and many fleets were retrofitted with vibration-based systems already. These systems were sometimes very adept at finding problems in the high-speed, helical portion of the gearbox as well as the generator, which ran at even higher speeds. Another key advantage the vibration system touted was the ability to pinpoint the source of the issue based on the frequency signature. However, the vibration systems often struggle to identify planetary defects in these gearboxes with their lower speeds. Mounting accelerometers where they could effectively monitor these planetary sections is also difficult. Vibration systems require many accelerometers to monitor the drivetrain, which can make installation expensive. Furthermore, a trained individual is often required to review and interpret data from these systems in order to obtain maximum benefit.
Option 2: Wear Debris Detection
Wear debris technology, on the other hand, has only one sensor and can be easily positioned as a sidestream loop on a variety of gearbox technologies, resulting in lower purchase and installation costs. Aside from being a more economical choice, wear debris systems provide a range of usability benefits. These systems are highly capable of detecting any flaw that liberates ferrous or non-ferrous debris anywhere in the gearbox. The wind turbine operator’s own staff can interpret results with ease and not only determine the existence of a problem, but also the rate and extent at which it is progressing. This can be extremely valuable, especially in planning for wind turbine repairs, which commonly require an expensive heavy lift crane with 300+ foot boom. Bundling multiple repairs together is a huge advantage when maintaining these systems.
Assessment of Wind Turbine Gearbox Planetary
A manufacturer of wind turbine gearboxes had a failure mode characterized by the outboard mounted planet bearing races spalling and cracking on a certain gearbox model. One of these gearboxes was found to have some steel debris on the filter during maintenance, but a borescope inspection couldn’t identify the damaged bearing due to a small clearance between the races. No other damage was evident, and planet bearing damage was a known failure mode for this type of gearbox. Initially, this failure mode was thought to fall in the “run to failure” mode. To mitigate risks while a gearbox replacement plan was being formulated, a Poseidon wear debris sensor was sourced to monitor the debris generation within the gearbox. Low levels of debris generation were immediately evident. Debris generation was proportional to higher wind events and remained quite low during the summer seasons. Given the ability to continuously monitor the gearbox and the high-quality data recorded from the wear debris monitor, it was decided to continue to run the defect to capture the failure “signature.” This could then be used to gauge the degree of damage progression in other gearboxes with the same failure mode. During the monitoring of this gearbox, another gearbox was diagnosed in the extreme early stages of the same failure with a few particles on the oil filter.
The combined benefits of early detection,
avoided O&m costs, logistics planning, accurate
budgeting and risk management have led
Cogentrix Energy Power Management to invest
in more Poseidon particle counters outfitting
groups of gearboxes that share common failure modes.
The Cost-Saving Solution
A repair on the early-stage gearbox in which the planet bearings were successfully exchanged while the gearbox remained in the tower was made. A much smaller crane was used, and the repair cost was 25% of the cost of complete gearbox replacement. This cheaper repair made early detection of the failure mode a critical component of proper maintenance. This method was even more economical when the work could be grouped to utilize the same crane and traveling crew on several repairs in succession. The wear debris monitors allow operators to scan for a rapid increase in debris generation, signaling a significant change in machine condition has occurred.
This continuous window into the machine condition reassures the operator that continued safe operation of the machine is possible until a step change in debris generation is observed. Even when a step change in particle generation is noticed, the blade pitch schedules can be altered on the turbine to effectively lower the stresses on the gearbox, reducing particle liberation. Particle generation feedback was used to find the optimum pitch schedule to maximize production while minimizing bearing damage. Once particle generation becomes severe, the unit can be secured to prevent the gearbox from seizing.
Measurable Results
The “run to failure” unit, as shown in the graph below, was run for 2.5 years before particle generation reached extreme levels. The wear debris monitor showed increasing levels of wear debris generation each year before exhibiting a step change, presumably when the bearing race experienced a through crack. Although the unit was slated to receive a complete gearbox exchange, the planet bearings were exchanged using the “uptower” method at a significant savings. Once disassembly was complete, it could be seen that 2 of the 6 planet bearing races exhibited massive spalling and through cracks. Since bearing replacement, this unit has run an additional 3.5 years on the replacement bearings. The Poseidon units have helped manage 9 additional bearing replacements and become a valuable tool in mitigation of this failure mode.
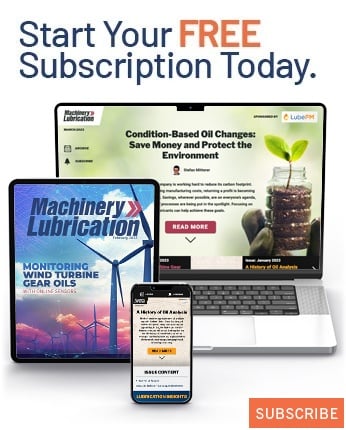