Almost every day, impressive new developments in machine learning and artificial intelligence (AI) are reported, such as:
- A computer program that taught itself the strategy game “Go” and beat the current world champion
- Impressive advancements in facial recognition software
- Almost instantaneous translation of one language to another (either written or spoken) using freely available online software
With all these advancements, it is natural to ask whether such techniques could be effectively applied to lubrication problems.
The rise in these many examples of machine learning/artificial intelligence is directly linked to the availability of high-quality data (and lots of it). Machine learning and artificial intelligence can generally be split into two types: supervised models and unsupervised models. Simply put, supervised models typically find statistical (or regression) models relating input data to output data and provided new input data that is covered by the training data set. These techniques should work well, although they are not able to reliably extrapolate if the new input data is outside that of the training set.
Unsupervised models typically use neural networks. Neural networks, also referred to as "deep learning", are a collection of algorithms loosely modeled on the human brain, designed to recognize patterns. These unsupervised models can effectively “work out” the best model for themselves - however, once a good model has been found, it is not always obvious why it works. In other words, the underlying algorithm that the machine learning model has found is not easy to unravel. There are numerous examples where artificial intelligence and machine learning have already been applied within the lubrication/tribology community, including:
Condition monitoring - Machines are now being supplied with an increasing number of sensors that can report their operating conditions (speeds, loads, lubricant temperatures) back to the OEM and/or machine owner. These machines can be fitted with additional sensors that monitor vibrations and electrical currents going in and out of the machine. Lubricant sensors can also detect wear particles or monitor lubricant degradation (such as dielectric-based sensors).
Figure 1: The types of events preceding machine failure.
By monitoring a large number of machines, warning signs of likely future failure can be predicted based on previous failures and correlating such failures with the various sensors data. Customers can be advised to service their machines or replace specific components once early signs of failure are detected. Even better, they may catch the root causes before they lead to failure symptoms. The schematic in Figure 1 below shows the type of signals that can be picked up before failure occurs.
The most commonly used techniques for condition monitoring are vibration monitoring and thermography (looking for “hotspots”). A number of commercial solutions are available today that use artificial intelligence and machine learning for condition monitoring (from companies such as SKF, GE, Siemens, and Bosch). There are also numerous start-up companies using more specialized techniques, such as ultrasound (UK-based Tribosonics; US-based UE Systems, with their OnTrak SmartLube system). For high-value machines, other specialized techniques such as lubricant monitoring by infrared and wear particle sensors may also be used. Although the general application is to advise customers of machines that may need service or components replaced, these techniques can also be used to monitor energy consumption, and customers can be given advice on how to reduce their energy consumption (and related cost savings can help pay for such monitoring systems).
Chatbots for Lubricant Helplines - Shell offers an online chatbot (Lubechat) that can answer simple customer queries and provide technical data on lubricant products. The 24/7 service is available in twelve countries and several different languages (including Chinese, Russian, German, etc.) Questions that cannot be answered by the Virtual Assistant are passed on to human experts for answers.
Fleet Telematics - There are commercial companies (such as Microlise) that extract data from heavy-duty vehicle electronic control units (remotely). The data contains speed, load, temperature data, route data and fuel consumption data. By combining data from many trucks, the most efficient routes between two or more places can be identified. This data can also identify improvements in logistics efficiency and fuel-heavy drivers (who can then be given training into how to reduce their fuel consumption).
Visualization and Classification of Wear Particles - AI and machine learning techniques are particularly powerful for image identification and classification. A number of researchers have used such techniques on wear particles. Size, texture, shape and color are all parameters that contain information about the wear mechanism and where it occurs. Neural network algorithms have been used to identify if the wear particle is metallic or an oxide; and whether the wear is due to fatigue or severe sliding.
Design of New Materials - Machine learning has been used by a number of researchers to optimize the properties of metal alloys and vapor-deposited hard coatings. For coatings, the thickness, composition, hardness and Young’s modulus all contribute to the tribological performance. Hard coatings are usually used to reduce wear. Similarly, for metallic alloys, properties such as density, hardness, Young’s modulus and fatigue life are all properties that researchers are attempting to optimize.
Prediction of Lubricant Properties - Lubricants are often a complex mixture of two or three different base oils, an additive package (which could comprise from 1% to 15% of the final lubricant), and in some applications (such as engine oil), large polymers known as viscosity modifiers. Predicting the various viscosities of the lubricant for different temperatures and shear rates is not straightforward; historically, such properties have been measured experimentally on a number of slightly different blends to find the optimum.
This type of problem is amenable to AI and machine learning since there are only a limited set of base oils, additive packages and viscosity modifiers in widespread use, and such techniques would be useful to lubricant and additive companies to improve the efficiency of their lubricant design process. Such companies are also likely to have good viscometric data on a wide range of lubricant formulations to test their AI models on. Unfortunately, since the composition of lubricants is usually a closely guarded secret or can change without warning, these techniques are likely to be kept “in-house” and used by lubricant suppliers for their own products.
Prediction of Lubrication Regime - Recently, researchers have used machine learning to predict the lubrication regime of a journal bearing. Key parameters such as speed, load, oil and surface temperatures, contact conditions and friction coefficient were recorded. Characteristic frequencies were found for the different lubrication regimes, and the model developed was able to distinguish between journals in the hydrodynamic, mixed or boundary lubrication regimes.
Numerous researchers have attempted to use artificial intelligence and machine learning to predict friction and wear. This is a much more complex problem since friction and wear are properties of the complete system rather than its individual components. The figure below shows a schematic of the complicated nature of a simple lubricated contact. Often, “running-in” takes place over a number of hours, during which contact conditions change. The simple passage of a loaded ball or cylinder over a flat piece of metal can induce hardness and other changes to the metals, which can influence friction and wear.
In addition, there are complex tribo-films formed by the lubricant, whose composition and other properties are not precisely known. The contact conditions (hydrodynamic, mixed or boundary lubrication) are determined by the operating conditions (speed, load, lubricant temperature, surface roughness), and, if wear occurs, the type of wear (abrasive or adhesive) depends critically on the loads and speeds. A large amount of data is needed to characterize the complete system; this data is not normally reported in sufficient detail in research papers for machine learning to be applied. In addition, the composition of lubricants is proprietary and usually only known to the lubricant and additive suppliers.
Figure 2: The complex nature of a typical lubricated contact.
Researchers, such as Professor Daniele Dini at Imperial College, are actively attempting to develop a “digital twin” of a tribological contact, but this is likely to be a long-term project which requires advances in a number of key areas (wear modeling, lubricant tribochemistry, material changes during sliding, etc.). In addition, any successful machine learning model will need to distinguish between the “good wear” that occurs during “running-in” from the “bad wear” that occurs near the end of a component’s life.
Looking further to the future, researchers at the University of Central Lancashire, led by Professor Ian Sherrington, are actively working in the field of tribotronics, in which individual tribological systems are monitored, and contact conditions can be changed depending on the sensor data. For example, in two-stroke marine engines, the oil film thickness between the piston ring and liner can be measured using a capacitive sensor, and the oil feed rate to the cylinder can be increased or decreased depending on the oil film thickness. Such systems could benefit from machine learning algorithms too.
Artificial intelligence and machine learning algorithms have already been used for many applications in lubrication and tribology. To progress further, the lubricant and tribological community will need to develop ways to share the large amounts of data that such models need. To date, most tribology tests generate relatively small amounts of data (compared, for example, to the number of photographs or text online, used for facial recognition and language translation); key material, surface roughness, and lubricant properties are not generally available for later analysis.
In the near future, when machines are connected and routinely sending information back to their manufacturers (and customers) about how they are performing, the use of AI and machine learning to give early warning of potential issues or faults with the machine will enable proactive maintenance to be undertaken, and customers will avoid potentially costly breakdowns und unscheduled machine downtime.
Further reading:
- Condition monitoring: see for example, https://www.ge.com/digital/iiot-platform, https://www.skf.com/uk/products/condition-monitoring-systems, https://www.boschrexroth.com/en/xc/company/press/index2-31872, https://www.tribosonics.com/, https://www.machinerylubrication.com/Read/31982/ue-systems-ontrak-smartlube
- Shell Lubechat: https://www.shell.com/business-customers/lubricants-for-business/shell-expertise/lubrication-services-for-your-industry/shell-lubechat.html
- Fleet telematics: https://www.microlise.com/
- Classification of wear particles: https://www.sciencedirect.com/science/article/abs/pii/S0888327015004732
- Design of new materials & lubricant properties: https://www.mdpi.com/2075-4442/9/1/2/pdf
- Lubrication regime: https://www.mdpi.com/2075-4442/6/4/108
- Predicting friction and wear: https://my.demio.com/recording/X4TOkK8i
- Tribotronics: https://www.sciencedirect.com/science/article/abs/pii/S0301679X07000631
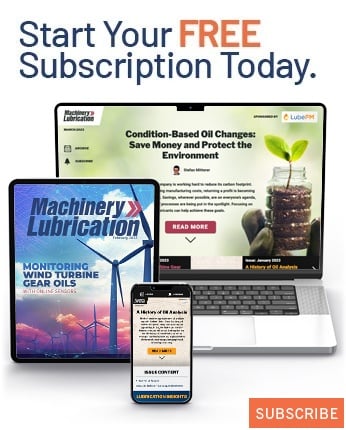