More and more these days, you will hear people (in almost any industry) talking about their concerns with locating and acquiring biodegradable lubricants. In most places, even non-machinery lubrication related, everyone seems to be very concerned with going green and utilizing biodegradable containers and packaging. I personally think it’s a great shift in our culture to not waste and litter as much. Going back to machinery lubrication, though, I often get asked a few questions about biodegradability: What is it? How is it determined or measured? Why does it even matter?
What is it?
Biodegradability refers to the ability of an object or substance to decompose by way of bacteria or other living organisms. Examples of biodegradable objects include paper and food. However, “biodegradable lubricant” is, to me, kind of a weird term. You see, petroleum or “crude oil” is a fossil fuel but not in the sense that it is old, degraded dinosaurs: a common misconception that even I believed for a long time. Petroleum is actually formed from 300-400 million-year-old aquatic phytoplankton and zooplankton: essentially really old algae. My point is that petroleum is inherently biodegradable in nature. It is a product of millions of years of biodegradation. However, that doesn’t necessarily mean that all lubricants are inherently biodegradable. As we all know in the lubrication industry, lubricants are made up of a lot more than just crude oil. Industrial oils and greases are complex and calculated combinations of specific base oils, thickeners and additives. Regarding lubricant biodegradability, we are mainly talking about lubricants that are READILY biodegradable, more along the lines of vegetable oils and some synthetic ester base stocks. Polyalkylene glycols (PAG) are generally a good biodegradable lubricant to use in place of vegetable oil and are manufactured in such a way as to increase the performance of the lubricant to meet a wider variety of requirements and conditions.
What Industry Requires Biodegradable Lubricants?
Generally, food processing requires biodegradable lubricants. Food processing facilities aren’t so much concerned with the biodegradability as they are with the non-toxicity of the lubricants that are associated with biodegradability. Not that food processing facilities are going to put out a product that potentially has an accidental lubricant leak somewhere in their process; they are very stringent on their quality requirements regarding what enters and leaves those facilities. I know this from personal experience with food processing facilities; they all take this ultra-seriously, so rest assured that food safety is at the top of their priority list. As a consultant with Noria, I also take this very seriously when making food grade lubricant recommendations to meet the operational requirements of their machines. It is a long and tedious task, but it is of the utmost importance that we recommend a lubricant that is safe and exceeds the desired performance requirements.
How it is Determined/Measured
ISO 9439 is the standard that must be met for a lubricant to be deemed readily biodegradable. In some other cases, OECD 301B Standard can be performed in place of ISO 9439. A biodegradable lubricant has to be degraded by more than 60% within 28 days in order to qualify as a READILY biodegradable lubricant. The biodegradability tests treat a lubricant sample using a variety of microorganisms with oxygen present, which will produce CO2. The amount of CO2 produced is measured and used to determine the biodegradability of a lubricant.
Along with meeting those standards, the lubricants are run through quite a few different toxicity tests. For instance, OECD 202 Daphnia Sp., Acute Immobilization and Reproduction Test and ASTM D6081 Aquatic Toxicity Test are two of the common toxicity tests run on potential biodegradable lubricants. Although a lot of the toxicity tests are for marine and aquatic toxicity, there are also tests that utilize bacteria, plants and various other organisms.
Why it Matters
As we all know, resources are becoming more and more scarce. So, being able to extend the life of a machine through better lubrication practices is becoming a higher priority for a lot of the facilities we visit. Not only because they are changing lubricants less but because they are also spending less in the long run on high volumes of lubricant and specialty lubricants like biodegradable lubricants. Couple that with the reusability of biodegradable lubricants, and we have the perfect storm for maximum recyclability. By utilizing fewer resources, specifically oil and grease, some of the higher price points of these Environmentally Acceptable Lubricants (EALs) sting a little less. Both biodegradable and regular industrial lubricants are often recycled through a process called vacuum distillation to remove contaminants and produce a new base oil.
Every company, every industry and every employee is running very lean. I’m talking ten percent body fat lean. Most people we interact with in these plants and facilities are usually wearing multiple hats and performing multiple jobs. Our lubricants also need to be able to perform multiple jobs, not in the application sense but in terms of sustainability, cost-effectiveness, reusability and recyclability. Before, there were obvious causes of concern with the performance of these EALs; the other concern was price point. With a high cost and low performance, most industries were very reluctant to change to EALs if they were required to do so. Now lubricant manufacturers have sort of figured out a way to meet all of the specific machinery requirements while still meeting biodegradable standards and it is becoming slightly easier to make the switch to EALs. A lot of these facilities are making the switch and becoming greener processes; in return, the world is still receiving quality products while reducing the wasting of our precious resources.
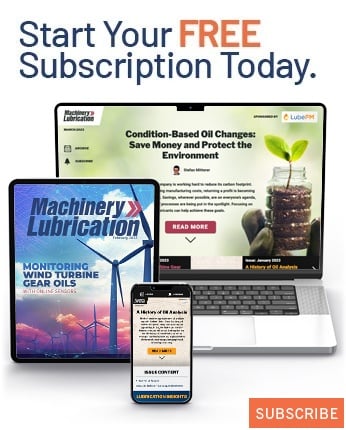