Plants, mines, and industrial organizations of all kinds are constantly seeking out the best-performing hydraulic oils to ensure maximum machine efficiency and reduce total cost of ownership for thier assets. One way to ensure this is by selecting a quality lubricant with a substantial in-service lifespan and the ability to protect equipment from contamination and total system failure.
A Turbine Oil Oxidation Stability Test (TOST) is commonly used to evaluate the potential service life of hydraulic oils. But while many industries still hold it in high regard, relying on TOST alone will not give you the whole picture. Testing conditions may differ significantly from real-world conditions in and around your machine. There are also other tests and properties to consider when choosing a hydraulic oil that meets your needs for service life and performance.
Did You Know?
More than 75% of all hydraulic system failures are due to contamination.Source: AMPTIAC Quarterly, Machinery Lubrication.
What about TOST?
Oxidation stability, while it certainly plays a role in hydraulic oil service life, is not the only determining factor in the actual service life of hydraulic oil used in field conditions. For this reason and it should not be the only source utilized when choosing the right oil for a plant’s needs, especially when evaluating which option will decrease total asset ownership costs.
According to the ASTM, while the TOST method has its place in oil evaluations, “it should be recognized, however, that correlation between results of this method and the oxidation stability of a lubricant in field service may vary markedly with field service conditions with various lubricants.”
This discrepancy is a direct result of the TOST testing method. When hydraulic oil is put through TOST, it is subjected to intense and often unrealistic conditions, including extreme temperatures, severe oxygen contamination, and elevated water levels. By not replicating actual field conditions, the true oil lifecycle is misrepresented, making it difficult to achieve an accurate read on an oil’s potential service life when it is porperly used and protected.
While these results can provide insight into different performance features, they should be used with reservation and not held in regard as the sole source of data during oil purchasing decisions. Because TOST cannot be exclusively relied upon, results need to be analyzed and used in conjunction with other key performance indicators, such as wear resistance, viscosity, oxidation stability, and zinc levels to uncover the true useful life of hydraulic oils.
Key Performance Indicators
Wear Resistance
Wear resistance is hydraulic oil’s ability to reduce the wear rate in frictional boundary contacts, directly affecting machine life and health. This fluid forms a protective film on metal surfaces to prevent direct metal-to-metal contact, which can cause serious wear conditions such as:
- Abrasion: Abrasive wear is the dislocation of materials caused by hard particles or hard outgrowths on surfaces. This is the most frequent and rapid wear mechanism affecting machine health. The most common cause is contamination.
- Adhesion: Adhesion occurs when materials from one surface transfer to another during relative motion and create a localized bonding between the contacting solid surfaces. During this transfer, materials from one sliding surface become attached to another. Common causes include low viscosity and high loads.
- Fatigue: Fatigue results when high shear stresses from rolling contact cause subsurface microcracking. These cracks can become interconnected and intersect with machine surfaces, eventually allowing for the release of particles into the oil. This commonly correlates to the overall age of the machine.
- Corrosion: Also known as chemical wear, corrosion is caused when corrosive fluids are in continual, long-term contact with load-bearing metal surfaces, causing a chemical or electrochemical reaction. Corrosive contaminants can come from cleaning, environmental conditions, and incorrect or degraded oil.
Since most machines have finite lives and wear at some rate, mild wear is usually unavoidable and should be viewed as an expected condition. Mild wear is hallmarked by small particles, less than five microns in size, that are being worn away. These particles are both easily detectable and controllable.
Severe wear, although controllable, is a significant issue. By selecting the hydraulic oil that best protects machines in a facility’s specific environment, plants will extend their savings by not having to spend the manpower and money down the road to correct the issue. This is one of the reasons lubrication selection is so crucial.
Viscosity
Viscosity is the measure of a fluid’s resistance to flow and shear, and according to the Society of Tribologists and Lubrication, it’s one of an oil’s most important physical properties.
Hydraulic oils with a higher viscosity will flow with greater resistance compared to a fluid with lower viscosity. But viscosity, both too high and too low, can cause serious damage to a system. It’s important to find the balance that works best for a specific machine’s needs and the environmental demands put on that machine.
Did You Know?
89% of lubrication professionals consider viscosity index when selecting a lubricant.Source: Machinerylubrication.com reader poll.
Going hand in hand with this is the viscosity index (VI), which measures how a hydraulic oil’s viscosity changes when there is a shift in temperature. An oil with a high VI will maintain its viscosity better over a broader range of temperatures when compared to a lower VI oil. This is especially important when considering a hydraulic oil that will need to operate outdoors and be subjected to the elements.
For the viscosity to be its most effective, it needs both a high VI and a high bulk modulus, or the ability to resist volume reduction under pressure. Any change in these two qualities can have serious effects on the efficiency of which power is transferred in the hydraulic system. While bulk modulus is an inherent property of the base oil and cannot be improved with additives, the VI can be improved through base stocks known as Viscosity Index Improvers.
Not selecting the correct viscosity can often result in a variety of negative effects. For example, if a critical machine is running hot, it could be a warning sign that the viscosity is too high, causing fluid friction, or too low, causing surface contact friction. By maintaining the hydraulic oil’s viscosity within an optimum range, power consumption is reduced and machine cycle times are faster, equaling an increase in productivity.
Viscosity is also an important indication of more serious issues that may be occurring in a system. For instance, a change in viscosity is usually a lagging indicator of oxidation. As the oil degrades, the average molecular weight increases, creating an increase in viscosity.
Oxidation Stability
Oxidation stability is the hydraulic oil’s ability to resist heat-induced degradation caused by a chemical reaction with oxygen and is often marked by a foul odor, an increase in viscosity, and a darkening of the oil. The rate of oxidation is affected by conditions such as high temperatures, water, acids, and other catalysts such as copper. Oxidation greatly reduces the oil life and leaves harsh, insoluble by-products such as sludge and varnish. The deposits that form on sensitive machine surfaces interfere with fluid flow and mechanical movements. Varnish and sludge deposits also contribute to wear, corrosion, and impaired heat transfer.
Oxidation is the most predominant reaction of in-service hydraulic oils. Not only is it responsible for sludge and varnish, but it can also deplete additives, break down base oils, increase the acid number (AN), and produce rust.
Every hydraulic oil is designed with oxidation-controlling ingredients known as antioxidants. These antioxidants are intended to be a sacrificial protection layer for oxidation to take place instead of the oil, allowing the maintenance team time to take proactive, preventative measures before real damage can occur. By closely evaluating the base stock and the antioxidant package of a lubricant, facilities can better understand an oil’s ability to protect itself and provide maximum service life.
An effective antioxidant-rich hydraulic oil will perform based on the three basic steps of interrupting oxidation:
- Initiation: Occurs when oxygen enters a hydraulic oil. The antioxidants should limit the amount of oxygen that can enter a system.
- Propagation: Occurs when the oxygen begins to react with the oil. The antioxidants should shorten and limit the number of oxygen reaction cycles.
- Termination: Occurs when the antioxidants break into the reaction cycles and form stable radicals that delay the process.
While the antioxidants do a great job of diminishing the results of oxidation and keeping the oil healthier for longer, once the process starts, an inevitable breakdown cannot be fully prevented. It is important to continually test the oxidation levels of hydraulic oil to measure and track performance to determine when an oil change is necessary.
Other harmful effects of oxidation include:
- Corrosion: Oxidation produces acids that begin attacking component surfaces, causing pitting and surface degradation. Water, another byproduct of oxidation, only serves to increase the corrosive potential of acid in hydraulic oil.
- Loss of Lubricity: Oxidation alters the flow and lubrication characteristics of oils by producing sludge, which attracts and traps active additives, rendering them useless.
- Poor Water Demulsibility: This relates to the oil’s ability to separate from water. This function greatly declines as oxidation runs its course. When water is allowed to stay in a system, it can cause rust, increased corrosion rates, separation of additives and base oil components, and dangerous vaporous cavitation conditions.
- Air Entrainment and Foaming: Entrained air affects the oil’s bulk modulus, diminishing the strength of the oil film and increasing surface-to-surface contact and wear. An exaggerated state of air entrainment can result in foaming, which inhibits heat dissipation and speeds up oxidation, dropping acid and sludge into the hydraulic oil.
ZINC LEVELS
For decades, zinc has been a key additive in hydraulic oils for its antioxidant properties, and is primarily used as an anti-wear agent or an antioxidant. While zinc-based additives are naturally sacrificial, it’s not simply the metal being added to the oil that makes this happen. Instead, it occurs through a chemical reaction between zinc oxides and organic acids that produce an effective compound known as ZDDP, or zinc dialkyldithiophosphate.
ZDDP uses phenolic and aminic compounds to neutralize free radicals and disengage the oxidation reactions, preventing harmful acidic byproducts from corroding equipment parts or changing the base oil’s lubricating capabilities.
Despite this advantage, using zinc-based additives can have serious repercussions that may warrant considering a zinc-free alternative during the hydraulic lubrication selection process. For example, zinc-based additives are corrosive to different metals that can be found on different machinery, and often attack the surfaces of metals such as yellow metals.
Not only are these additives corrosive to metals, but they also have a serious environmental impact as well. Because they are non-biodegradable, research has found that zinc-based additives are also aquatically toxic, negatively affecting both individual organisms and entire ecosystems.
Finally, the variety of ZDDP compounds also differ significantly in their effects on hydrolysis and thermal degradation. Achieving high-quality levels in both categories can be a challenge for lubrication manufacturers, whereas these benefits are more easily achievable using zinc-based alternatives.
Conclusion
While TOST results can provide a starting point when comparing hydraulic oils, it should not be the only property considered. By evaluating multiple facets of an oil, such as its wear resistance, viscosity, oxidation stability, and additives, a facility can get the whole picture of how a hydraulic oil will perform and how long it can be expected to remain useful once in service.
It pays to work closely with your hydraulic oil supplier, taking the time to understand your facility's environment and your applications particular needs before selecting the optimal oil for the job. Fewer drain and fill procedures, less component wear, and improved equipment reliability can all be achieved by improving hydraulic oil selection decisions with a more holistic approach..
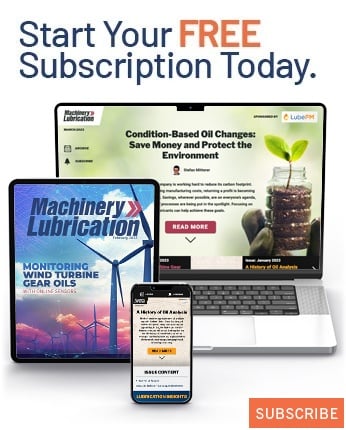