Arizona Public Service’s Palo Verde Nuclear Generating Station (PVNGS), is the 2001 recipient of the Augustus H. Gill Award for Excellence in Oil Analysis. Congratulations to Bryan Johnson and his team at Palo Verde for their contribution to industry in the development of best practices.
Arizona Public Service, through PVNGS, has contributed to the development of innovative standards for maintenance programs. Examples of this outside of lubricant analysis are in the use of other PdM technologies.
“Thermography has been significantly upgraded - programmatically, technically and in scope. The thermography program monitors and records more than 2,000 standard surveys annually with the performance of the PdM tasks generated routes,” said Bryan Johnson. “Vibration monitoring is a key component of the PdM program especially when combined with the fact that many points are also monitored with lubrication technologies. Both technologies are beneficial when applied to rotating machinery, especially when data from each technology supports the other.”
“The implementation of the thermography process is unique to industry. The new process includes a portable computer to process the data in the field, making the thermography program fully predictive and trend-based versus a more traditional preventative approach.
“The Palo Verde lubrication program has long been a successful portion of the PdM strategy. A cornerstone of this process is a comprehensive onsite oil and grease analysis process that has tested more than 20,000 lubricant samples since its inception.
“Testing is divided into categories of wear analysis, cleanliness and chemistry. Oils and grease are routinely tested. Staff knowledge has been technically augmented by consistent participation of the lube team members in industry standards committee activities. Offsite training has been embraced by the facility and its team members.
The success of the Palo Verde lube program is a result of much more than just testing. It encourages 1) careful product purchase, 2) detailed attention to ensure that only specified products are introduced into machines and lube addition logs, 3) proper lube handling and 4) condition monitoring testing for both equipment and lubricant health. The lubrication program has become an accepted and integral portion of the PVNGS maintenance culture,” continued Mr. Johnson.
A broad new culture of ownership in the lubrication process is clearly evident at Palo Verde. Lubricant storage is an example of how maintenance has embraced this evolving culture. Before handling changes at PVNGS were implemented, lubricants were received through the warehouse, tested and then released to maintenance for staging and use. A weakness was identified in the storage and distribution practices once the lubricant left the warehouse. To resolve this problem basic guidelines were given to the team of frontline employees who began to improve the handling and short-term storage practices. The new program established that once the lubricant left the warehouse, it is staged in one of two secure centralized storage facilities. The two dedicated buildings are climate controlled with filtered air to ensure consistent temperatures. All drums are grounded, labeled to allow traceability and have a dispensing oil filter. Labels of larger drums include several smaller peel-off stickers containing product information to be applied to smaller secondary containers when lubricant is transferred for use.
Click here to see more pictures from Palo Verde
Secondary containers are used to move and store oils to an auxiliary storage within the plant. Prior to filling these containers, a volume of oil is added to flush the container to ensure cleanliness. Makeup is not added to any container until it is empty. When the oil is added, one of the smaller peel-off labels from the larger drum is added to ensure traceability.
Lubrication requirements for each plant machine sump/reservoir/cavity are uniquely identified in a controlled electronic database. Only a small number of individuals have access to this database to make changes; a single approved lubricant defined by brand name is approved for each pump. The technician/operator is required to search the electronic database/manual to identify the correct lubricant prior to any lubricant top-ups or change-outs. The work is then tracked, which provides change-out dates for each lubricant. For every identified lubrication point at PVNGS, there is a clear expectation that only the defined lubricant will be used.
![]() |
Steve is performing several viscosity tests at once as he watches oils in the 40°C test bath.
|
In addition to test methods typically used such as acid number and viscosity, FTIR analysis is used as a main-stay of the receipt inspection program. An FTIR reference baseline spectrum has been established for each lubricant. All new lubricant shipments must match the reference spectra. If a difference is found, an investigation is conducted until the product is either rejected or a new baseline is established.
A vendor formulation change is treated as a new product when differences in FTIR spectra are detected. In this case, a new product evaluation is performed to decide if the product is acceptable. This process has helped keep the station up-to-date on vendor formulation changes and gives PVNGS control over which products to use within the plant. It also allows PVNGS to either accept the changes in the lubricant prior to use, or to perform a market survey and convert to a better product if needed.
![]() |
Jeff, journeyman mechanic, is transferring oil into a secondary container for an oil addition. The red plastic bags hanging from each drum contain peel-off labels that he will use to label the secondary container. Note that the tips of each tube downstream of the handpumps are sealed to keep contaminants out.
|
The International Council for Machinery Lubrication presented the 2001 Augustus H. Gill award to Bryan Johnson, representing Palo Verde Nuclear Generating Station and Arizona Public Service, on March 19th, at the Practicing Oil Analysis Conference 2002 plenary session in Tulsa, Okla. The award features a scale model of a torsional viscometer. It is believed that Professor Gill, in his seminal text “A Short Handbook in Oil Analysis,” of 1897 was the first to describe this viscometer. In the years that followed, there were several viscometers advanced based on this original design. These include the well-known Brookfield rotary viscometer.
The 2002 Gill Award will be presented in the spring of 2003 during Lubrication Excellence 2003. Is your company up to the challenge?
Bryan Johnson nominated PVNGS for the 2001 Augustus H. Gill Award by submitting an application form found at www.icmlonline.org. You too can nominate your company for the honor of being recognized as an industry leader in oil analysis and lubrication best practices. For more information contact ICML at 918-451-7849.
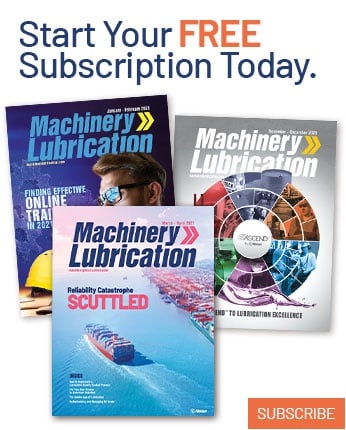