Monitor Internal Conditions from the Outside
Oil analysis is a diagnostic, predictive maintenance tool for monitoring and evaluating lubricant and equipment conditions. Participating in an oil analysis program allows you to see what’s happening inside your equipment to identify issues, prevent catastrophic failures and increase equipment reliability.
Testing and analysis provide vital information as to the condition of both the oil and the equipment being tested. Wear particles and contamination concerns can be identified using several methods and, if left unchecked, can severely affect equipment performance and reliability or cause a significant failure. In addition, sources and causes of equipment issues like abnormal wear, lube degradation, and component failures can be identified and mitigated.
Predict Maintenance
Playing a crucial role in predictive maintenance strategies, oil analysis results can help foresee maintenance needs by providing early indicators of potential issues, including fuel dilution, excessive idling, and component malfunctions. Establishing and monitoring trends within the oil properties can identify changes or deviations from normal operating conditions and may reveal deteriorating conditions, increased contamination levels, and degradation of the lubricant.
Establishing a trending history of oil analysis for equipment components can give early indications for maintenance activities like oil changes, filter replacements, and component repairs before the concerns turn to failure.
Oil Analysis Value: More Than Testing
Standard oil analysis tests include Elemental Analysis by ICP, Fuel Dilution, Nitration/Oxidation, Acid Number/Base Number, Viscosity, Particle Count, and many more. Each of these tests, performed by an accredited laboratory, provides equipment users with test results with severities, a review by a Data Analysts team, and maintenance recommendations to address the identified concern.
Effectively interpreting your sample test results and acting timely is where a world-class, successful oil analysis program differs from others – and has the greatest return on investment (ROI).
Numerical test results are indicated on the oil analysis sample report, and these results include:
- Wear metals
- Contaminant metals
- Multi-source metals
- Additive metals
- Contaminants (fuel, soot, water)
- Fluid properties (viscosity, acid number, base number, oxidation, nitration)
For each data set, results are flagged by severity, and a data analyst comments after reviewing the results.
Figure 1. Lubricant Analysis Reports Test Results for Wear, Contaminant, and Additive Metals
A systematic approach to interpreting results can help you better understand the data and make informed maintenance decisions. Comprehending each specific testing parameter and severity can help determine what the value represents and how it relates to the overall performance and health of the equipment and lubricant.
Figure 2. Lubricant Analysis Reports Test Results for Contaminants and Fluid Properties
Baseline values and trends can be established by collectively analyzing historical data from previous samples and comparing them against baseline reference samples. Baselines serve as ideal reference points for comparison and should represent normal operating conditions for the equipment.
Addressing Problematic Particle Contamination with Oil Analysis
The most common cause of component failure is the contamination of particles. This includes external particle contaminants, such as dirt or sand, and the microscopic pieces of metal generated during equipment operation that work their way into the lubricant. Through several oil analysis tests, including Particle Count, Particle Quantifier, Analytical Ferrography, and Filter Debris Analysis, these particles can be identified and quantified, and the root cause investigated.
Particle Count
Particle count is a valuable test for determining fluid and system cleanliness in filtered systems such as:
- Hydraulics
- Turbines
- Compressors
- Auto/power-shift transmissions
- Recirculation systems
- Filter gear systems with a fluid viscosity of approximately ISO 680 or less
Particle count testing measures all particles accumulated in a system, including metallic and non-metallic particulates, dirt, fibers, biological growth, etc.
Several test methods exist to quantify the particles when measuring the number of particles within a used lubricant. Results can differ by instrument and laboratory, so it’s important to know what method is used on your oil sample and understand how the test methods can influence your results.
The Automatic Particle Counting method uses an instrument to count the particles in a sample. The particle count instrument has a laser and sensor to detect and measure the number of particles via light omission. Typically, the results are presented as the number of particles per milliliter at several different micron sizes.
Particle Quantifier
To measure the concentration of sizeable ferrous wear particles in used lubricants, particle quantifying (PQ) is the preferred test method. Particle quantifying technology measures the density of ferrous debris without a particle size limitation and assigns a value based on the degree of metallic content present in the sample.
When used in conjunction with AES-ICP, comparing PQ results with ICP results, the severity of an abnormal wear event becomes evident. The ICP will detect the smaller wear sizes but has a limitation with larger (> 7µm) particles. An elevated Particle Quantifier result from the same sample would indicate that the component has begun generating larger-sized wear debris no longer detectable by the ICP. Further testing can then be performed to investigate the size and shape of the particles to help maintenance personnel discover the source of the contamination and assess the damage to the component.
Carefully monitoring iron concentrations with elemental metals analysis (ICP) and the particle quantifier will identify increasing wear trends and alert the operator to a potential problem early on. This will also help act as a cue to have the laboratory perform an Analytical Ferrography test on the lubricant sample to qualify the type and severity of the wear.
Analytical Ferrography is a powerful tool when correctly performed by a trained analyst and provides deeper insights into mechanical wear or contamination. When used in conjunction with metals analysis, PQ, viscosity, acid number, and water content, a well-defined course of action is provided to the user to correct the condition of the unit and the lubricant.
Analytical Ferrography
Analytical Ferrography takes particle contamination identification to the next level by analyzing and characterizing wear particles suspended in lubricating oils. It provides detailed information about the size, shape, composition, and distribution of wear debris, allowing for a comprehensive understanding of the equipment’s condition.
Analytical Ferrography involves reviewing a ferrogram (a slide prepared from the sample to study the wear and contamination under a microscope). A portion of the used oil is transferred to a slide on which the ferrous (containing iron) objects in the oil are collected. After proper agitation, a small amount of the sample is poured through a thistle tube across a glass slide suspended over a powerful magnet. The oil, soot, dirt, and other debris are rinsed from the slide, leaving the ferrous wear visible under a microscope.
Figure 3. Analytical Ferrogram Showing Ferrous Sliding Wear, Lead/Tin Sliding Wear
Analyzing a ferrogram allows the analyst to see the different types of wear mechanisms in the oil. It is not limited by the size of the wear particle, like some other types of testing, meaning that large and small wear is easily identified in addition to clues of possible causes.
Figure 4. Analytical Ferrogram Showing Corrosive Wear, Abrasives, Lead/Tin Alloy
Filter Debris Analysis
Oil filters installed in equipment systems are designed to remove contaminants and particles that would otherwise circulate and damage the system. However, this also removes evidence that can help determine recommendations to address problems. By extracting the material caught by the filter and examining it, more insight can be gained into the type and magnitude of system wear and contamination.
The Filter Debris Analysis process removes particulates from the filter media and isolates them for laboratory analysis. This includes preparing a filter patch of debris present, an analytical ferrography, and an elemental metal test on any oil that arrived with the filter. A trained ferrographic analyst can then identify the particulates’ type, size, and shape. Combined with routine oil analysis testing, this can be valuable in discovering the root cause of equipment wear or catastrophic failure.
Oil Analysis: A Predictive Maintenance Tool
Oil analysis is an accurate and effective tool to detect abrasive particle contamination in lubricating oils with the proper interpretation, which can alert to needed maintenance well before failure occurs. Timely detection of potentially harmful contamination allows maintenance personnel to identify potential sources, take corrective actions, prevent adverse effects on performance and reliability, and improve the overall equipment lifetime.
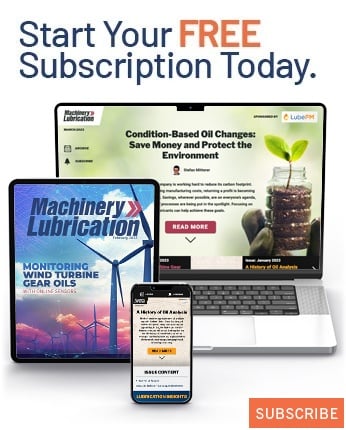