Lubricants play a vital role in the intricate world of machinery. In the industry, we often refer to them as the lifeblood of a mechanical system, tasked with minimizing friction and wear to ensure smooth operation. But what happens when you decide to change the type of lubricant used or need to mix different lubricants?
Can they coexist harmoniously, or will they clash, causing performance issues and potential damage? This article delves into the fascinating world of lubricant compatibility, equipping you with the knowledge to make better, more informed decisions for the overall health of your equipment.
Understanding the Reasons: Why Change?
Operators often choose to change the type of lubricant in their machinery for various reasons. These include the pursuit of enhanced performance tailored to specific operating conditions, such as reducing friction, minimizing wear, or extending equipment lifespan (Rudnick, 2016). Environmental concerns also drive this decision, with a growing emphasis on eco-friendly lubricants to align with sustainability goals and regulations (Rudnick, 2016).
Compatibility issues between the current lubricant and other machinery components may necessitate a switch to a more compatible option to prevent damage. Cost savings, driven by factors like lower maintenance requirements or extended service intervals, can also prompt a change. Advancements in lubricant technology continually introduce formulations with improved properties, enticing operators to upgrade for better lubricity or resistance to extreme conditions (Mang, 2018).
Additionally, equipment upgrades or modifications may require adjustments in lubricant selection to match updated specifications. Ultimately, the decision to change lubricants is multifaceted, influenced by performance needs, environmental considerations, compatibility requirements, cost factors, technological advancements, and specific equipment considerations. The question remains: what are the risks associated with such change?
Understanding the Players: Oils and Greases
The symphony of machinery will play in harmony when every instrument hits all the right notes. The choice between oil and grease for lubricating equipment comes down to its design, operating parameters, and environment. Each has its strengths: oil excels at reducing friction and heat, while grease excels at staying put and sealing out contaminants.
Base oils form the foundation of lubricants, dictating their viscosity, thermal stability, and lubricity. Common base oils include mineral oils, synthetic oils, and vegetable oils (Rudnick, 2016). Mineral oils, derived from petroleum, are widely used due to their affordability and compatibility with a range of materials.
Synthetic oils, such as polyalphaolefins (PAO) and esters, offer superior thermal stability and oxidation resistance, making them suitable for high-temperature applications. Vegetable oils, while environmentally friendly, may exhibit poor oxidative stability compared to mineral or synthetic oils (Rudnick, 2016).
Greases are lubricants that incorporate thickeners to enhance their consistency and adhesion properties. Thickeners, such as lithium, calcium, and polyurea, are chosen based on their compatibility with the intended application and other lubricants (Mang, 2018).
Lithium thickened, mineral oil-based greases are versatile and compatible with most materials, making them a popular choice for general-purpose lubrication. Calcium-based greases offer improved water resistance but may react unfavorably with certain additives. Polyurea thickeners provide excellent high-temperature performance but require careful consideration of compatibility with other greases (Mang, 2018).
Considerations When Mixing Lubricants
Mixing lubricants can lead to unpredictable results if compatibility issues are not addressed. Some key considerations include base oil and thickener compatibilities as well as additive interactions.
Different base oils may not mix well, leading to phase separation or reduced performance. It's essential to ensure compatibility between base oils when blending lubricants.
Greases with different thickeners may exhibit chemical incompatibility, resulting in softening, hardening, or loss of lubricating properties. Compatibility testing is crucial before mixing greases with different thickener types.
Most lubricants contain additives to enhance their performance characteristics. However, additives from different lubricants may interact adversely, causing degradation or loss of functionality. Compatibility testing should assess the compatibility of additives when blending lubricants (Bell, 2017).
Verifying Compatibility
Industry-available charts for both base oil and thickener compatibilities can serve as a first step in verifying how likely an undesirable reaction can occur when changing lubricants of different chemistries. Both compatibility for the base oil and for the thickener should be looked at independently. Below are a couple of examples of such charts you can refer to when considering a decision to change.
Miscibility of Base Oils
Source: Klüber Lubrication
Miscibility of Thickeners
Source: Klüber Lubrication
In addition, it is important to consider the materials present in the equipment. Lubricants may influence sealing materials, causing them to swell, shrink, or become brittle. Certain chemistries are not compatible with paints and primers that may have been used on the internals to initially prevent corrosion.
Base Oil Compatibility with Seal Materials
.jpeg)
Source: Klüber Lubrication
An operator can also perform quick in-field checks, considered as spot tests, where small quantities of lubricants are mixed, ideally in a clean glass container, and observed for separation, thickening, or oil bleeding. Similarly, oils can be mixed at different ratios to observe for separation, cloudiness, or any other readily observable reactions like forming of gelatinous substances. Such tests are not meant to be scientific and definitive but can be used in times of desperate need for a quick check.
Though these charts or spot checks are a good start, it is recommended that laboratory compatibility testing is carried out to help minimize the effects of lubricant mixing, especially in critical applications where an unplanned shutdown needs to be prevented above all costs. There are several methods that can assess lubricant compatibility and identify potential issues, such as:
Solubility Testing: Solubility tests involve mixing lubricants at elevated temperatures and observing phase separation or cloudiness, indicating poor compatibility. Usually, three sets of mixes are considered: 90:10, 50:50, and 10:90 (ASTM International, 2020).
Foaming Characteristics of Lubricating Oils: This test method evaluates the foaming tendency and stability of lubricating oils under specified conditions. (ASTM International, 2020)
Four-Ball Wear Testing: Four-ball wear tests evaluate the friction and wear properties of lubricant blends, helping to assess their performance under load conditions (Bell, 2017). This is a quick and inexpensive way to check for basic wear resistance performance of mixed lubricants.
Fourier Transform Infrared Spectroscopy (FTIR): FTIR analyzes the chemical composition of lubricant blends, detecting any changes or reactions that may occur upon mixing (Bell, 2017).
In addition, for greases, typical tests include Dropping Point and Worked Penetration testing to establish compatibility.
Lubricant compatibility is a critical aspect of maintenance and reliability engineering, ensuring optimal equipment performance and longevity. Understanding the properties of base oils, thickeners in greases, and additives is essential for selecting compatible lubricants and avoiding detrimental effects on machinery.
By incorporating compatibility testing methods into lubricant management practices, industries can mitigate risks associated with lubricant mixing and maintain efficient operations. As a final word of caution, anytime you are considering a change, a proper flush and drain can help mitigate issues down the road and ensure you are getting the most out of the new lubricant you decide to use.
References:
Rudnick, L. R. (2016). Synthetics, Mineral Oils, and Bio-Based Lubricants: Chemistry and Technology (3rd ed.). CRC Press.
Mang, T. (2018). Handbook of Lubrication and Tribology, Volume II: Theory and Design (2nd ed.). CRC Press.
ASTM International. (2020). ASTM D4175 - 13(2020) Standard Terminology Relating to Petroleum, Petroleum Products, and Lubricants.
Bell, J. P. (2017). Compatibility of Grease Thickeners. Machinery Lubrication Magazine.
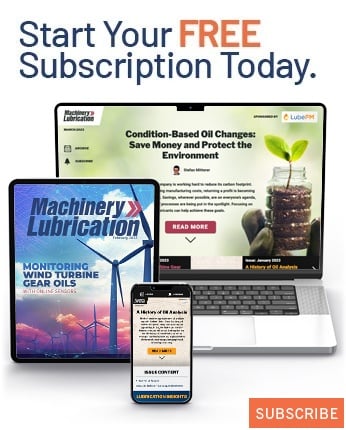