One of the best ways to care for machine assets is to ensure that the lubricants protecting them are clean, healthy, and ready to perform before they are put into service in our machines. It is common for oil analysis to be used to monitor the condition of in-service lubricants, but fewer organizations take a close look at "new" lubricant shipments to determine whether they meet standards for cleanliness or other properties. Some facilities may not even have set specific and documented standards with lubricant suppliers, making it difficult to hold them accountable if a shipment arrives too dirty, with incorrect viscosity, or other issues.
This article will help get you started in the process of defining standards and maintaining them through proper condition-monitoring activities and lubricant storage practices with a focus on the early stages of the lubricant lifecycle. With these insights, you can keep lubricants cleaner and better protected from the start, leading to downstream benefits across the entire lubricant lifecycle, including fewer oil changes, less wear on components and seals, and ultimately a lower total cost of ownership. One of the best ways to secure your investment into both your machine assets and lubricants is by working to enhance the standards for receiving, storing, and maintaining "new" lubricants to ensure they remain as high-quality as possible while awaiting use.
Dirty Lubricants
Before diving into potential contaminants, it is important to clear up a common misconception. Namely, that "new" oil is clean oil. In reality, lubricants can (and often do) arrive dirty if you and your supplier do not have controls in place. Depending on your cleanliness targets for that lubricant, it may simply require additional filtration before use, or it could mean rejecting the shipment and returning the lubricant to the supplier in exchange for a product that meets your specifications.
Contaminants
While most lubricant manufacturers set out to produce a clean, high-quality oil, contamination is still an ever-present threat, including fibers, debris, oxidation, and chips from oil drum liners. Without stringent process controls, all can find their way into a lubricant. The four main culprits for contamination during the manufacturing process are:
- The formation of raw materials
- The packaging containers
- The manufacturing process
- The manufacturing environment
Did You Know?
Cleaning lubricants by just one cleanliness code can provide a 35% increase in equipment life.
Most lubricant manufacturers exercise considerable caution to not inflict solid debris contamination abuse on the lubricant they are manufacturing. From the start, the manufacturer visually inspects the raw materials before and during blending. As the materials are loaded into blending kettles, screens are used to catch unwanted materials. While these screens help control contamination, many manufacturers only use filters for larger-sized particles. It’s important to verify what filter sizes they are using, and to request a small, particle-capturing filter if needed and available.
Receiving
With less-than-ideal lubricants increasing the chances of experiencing machine failure and severe damage, it’s critical that facilities have a rigorous quality control process in place to check lubricants as they are received. Companies pay good money for these lubricants, and it’s important to ensure they are receiving the quality they paid a premium for.
Work with the Supplier
When first negotiating with a lubricant manufacturer, there are details that need to be agreed upon before the first delivery. This includes aspects such as delivery time, any documents that need to accompany the delivery, and the agreed-upon cleanliness standards that can be expected with each delivery. This will help set the bar for what is considered acceptable lubrication by both parties and help align expectations.
One accompanying document to consider requesting is a Certificate of Analysis (COA). This document includes details about the lubricant, such as:
- Base stock quality
- Additive quality and concentration
- Lubricant performance
- Thickener performance properties
- Contaminant and foreign additives presence
Table 1 lists specific lubricant tests that can be applied to assess these five new-lubricant qualities. Because testing can be expensive, the selection of these tests needs to be carefully and judiciously considered to ensure a facility is getting the entire picture it needs without overspending its budget.
Test or Property |
Base Oil Quality |
Additive Treat |
Overall Lubricant Performance |
Thickener Properties (Grease) |
Contamination and Cross-Mixing Between Lubricants |
Viscosity (40C and 100 C, high temp/shear, etc.) |
X |
X |
X |
X |
X |
Cold cranking and pumping viscosity |
X |
X |
X |
|
|
Flash point |
X |
|
X |
|
X |
Pour Point |
X |
X |
X |
|
|
Cloud point |
X |
X |
X |
|
|
Aniline point |
X |
|
X |
|
X |
Nitrogen |
X |
X |
|
|
|
Color |
X |
|
|
|
X |
Interfacial tension |
X |
|
X |
|
X |
Acid number/base number |
|
X |
|
|
X |
Elemental spectroscopy |
|
X |
|
X |
X |
Oxidation stability |
X |
X |
X |
|
X |
Rust tendency |
|
X |
X |
|
|
Copper strip |
|
X |
X |
|
X |
Foam stability/tendency |
|
X |
X |
|
X |
Air release |
X |
|
X |
|
X |
Hydrolytic stability |
|
|
X |
|
|
Thermal stability |
X |
|
X |
|
|
Shear stability |
|
|
X |
X |
|
Demulsibility |
X |
X |
X |
|
X |
Film strength (4-ball, etc.) |
|
X |
X |
|
|
Filterability |
X |
|
X |
|
X |
Bleed resistance |
|
|
X |
X |
|
Dropping point |
|
|
X |
X |
|
Grease consistency |
|
|
X |
X |
|
Particle count |
|
|
|
|
X |
Moisture analysis |
|
|
|
|
X |
Storage stability |
X |
|
X |
|
|
Table 1: Each “X” denotes that this test can supply useful information for the corresponding quality characteristic. Source: “Should New Lubricant Deliveries be Tested?” - Machinery Lubrication Magazine
In the Real World: Importance of Testing Oil DeliveriesWe had a customer several years ago in the mining industry in southwestern Wyoming that started with an oil analysis program. Some of the first results from their gear boxes were baffling them. They used an ISO 220 EP oil in most of their gear boxes. It was delivered in a bulk tanker from their local supplier (a major oil company distributor) into a bulk storage tank onsite. Many of the gear boxes they sampled came back with a “degraded” ISO level of less than 190. They also had traces of an anti-foam additive that was not supposed to be in the oil. We suggested they check with their supplier to see if they may have gotten a shipment of ISO 150 R&O oil mixed instead of the 220 EP. The supplier assured them that was not the case. We then suggested they watch the next delivery closely and test the oil right from the tanker. When the next delivery occurred, they were out observing it when they realized what the problem was. They had a bulk tank of ISO 68 hydraulic oil next to the bulk tank of 220 EP. Both oils were delivered from a “split tanker”. The hydraulic oil was in one compartment on the tanker and the gear oil was in another. The hydraulic tank was the first in line, so the distributor filled that first. When they filled the gear oil tank, they did not flush the hose they used to transfer the oils. “AHA” moment – the customer determined that the supplier filled the tanks in that order every time. After all those deliveries, the residual ISO 68 hydraulic oil left in the hose had diluted the gear oil’s ISO code – and introduced additives that they did not want in the EP gear oil. They insisted that the supplier use separate hoses for each oil from then on, and the oil got back to a level of tolerance within 6 months. The takeaway tells us that we should always observe and test our incoming oil deliveries. If it doesn’t enter your plant cleanly and uncompromised you are starting with oil that contributes to your machinery failure issues. |
Inspection
After the basic expectations have been met by the supplier, the receiving facility should begin inspecting the new lubricating oil. This can be done in two ways – visual inspection or oil analysis.
With visual inspections, a facility should:
- Check the label to make sure the right lubricant is being delivered and in the right amount.
- Check the container’s bungs, caps, and seals to check for potential contamination points.
- Check the label to make sure the lubricant is not out of date and falls within the required shelf life of the facility’s lubrication program.
If a facility is receiving a bulk delivery that must be delivered and offloaded with a pump, all lubricant transfer equipment should be inspected to make sure they have been properly cleaned and stored to reduce the chance of contamination.
Depending on the total lubricant volume and overall machine criticality, some sites will benefit more from performing an oil analysis instead of a visual inspection. Testing can be done on-site or through a traditional laboratory. Two simple yet crucial qualities to test for include:
- Viscosity – This is the single most important property of a lubricant; if the oil does not have the right viscosity, it needs to be returned to the supplier.
- Particle Count –If the facility can manage the current particle levels, lubrication professionals can begin filtering the lubricant to achieve the desired cleanliness state.
With either testing method, it’s important to choose the one that best fits the needs and capabilities of the receiving facility. If a lubricant is determined to be low quality or contaminated beyond what the facility is equipped to filter, the lubricant should be returned to the supplier. Make sure to establish expectations and a timeline for replacement lubrication delivery.
It is important to keep a record of the lubricant deliveries and mark the quality of the lubricant when received. If lubricant cleanliness goals for new deliveries are consistently being met, this is a strong partnership and a facility should consider keeping their current supplier. However, if lubricants are not meeting standards, a new supplier should be considered.
Storing Lubricants
Just like bearings or gears, lubricants need to be considered working components in mechanical systems. Just as a facility wouldn’t install dirty or damaged bearings, neither should they apply contaminated or dirty lubricants to their machines. Once the lubricants have been properly received and filtered, the lubricant needs to be stored properly to maintain its quality and prevent deterioration and contamination.
Building a Lubricant Storage Room
Having a dedicated space to properly store and handle lubricants is critical to keeping the lubricant ready for service. By establishing that the lubricant is properly stored, it ensures the oil is ready at a moment’s notice while also guaranteeing its own performance capabilities. This equates to better machine performance, less repair work, less downtime, and smoother operations.
No matter what steps were taken during receiving, if the lubricant storage room is not set up to properly house and protect the lubricants, all those efforts will be in vain. Each lubrication room should be outfitted to accommodate the number of lubricated assets in the facility as well as the quantity requirements for each machine. A great starting list of essential lube room equipment includes:
- Storage racks for drums
- Storage cabinets for sealable and refillable containers
- Bulk oil containers with a dispensing system
- Oil and grease transfer pumps
- Individual filter carts for each type of lubricant
- Reclaimers (for reconditioning used oil)
- Proper disposal receptacles for used oil
- Basic maintenance supplies (rags, fittings, spare filters, reservoir screens, etc.)
Environment
When it comes to lubrication storage, the environment has a large impact on the quality of protection offered to the lubrications housed within. Three of the most common silent adversaries include extreme temperatures, temperature fluctuations, and humidity.
These three conditions support the movement of air between the atmosphere and the headspace of the lubricant container, allowing the container to “inhale”. When this happens, air, moisture, and small airborne particles can enter the container and degrade the base stock and additives. As water condenses inside the container, it will eventually drop to the bottom, where it can accidentally be pumped into a machine during top-offs. This moisture also has the ability to degrade the additive package and accelerate the oxidation of a lubricant’s base stock once it’s put into service.
Storage Life
Most lubricants come with recommended shelf lives based on their additive packages. Shelf-life information is available from the lubricant supplier or manufacturer for each product and should be verified upon delivery. This shelf-life is based on the idea that the lubricant will be stored in ideal conditions, so the cleaner and more efficient a facility’s lubrication room is, the longer the lubrication will last. It is also essential that a facility employ a First-In-First-Out (FIFO) rotation schedule to ensure that stored fluids do not accidentally exceed their shelf-life.
Conclusion
With machines being pushed to new performance heights every day, it’s more critical now than ever for a facility to have a quality lubrication program in place. By ensuring that during every stage of the lubricant journey, from receiving to storing and handling, to transferring into the machine, ensuring required quality standards are being met, a facility can guarantee the cleanliness and longevity of its lubricant investment.
By understanding that no new oil is ever clean, lubrication experts can take control of their lubricants' quality and form an action plan that fits the needs of the company. Through this, a facility can hope to achieve new levels of success and continue advancing in a proactive manner.
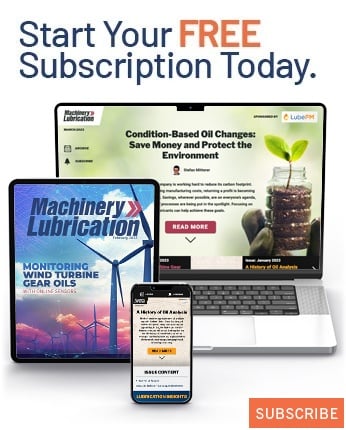