For the last six years, I have traveled the world performing failure investigations and developing lubrication programs for facilities in every industry.
While on the surface, they may all seem as unique as fingerprints, in reality, they all have one major thing in common: their lack of education in best practice lubrication techniques and program management methods is causing catastrophic damage to the assets their businesses depend on.
Whether it’s something as simple as not knowing the current lubricant in their mainline equipment or something as challenging as maintaining the crucial demands of a well-developed lubrication program, all shortcomings lead to pain points that prove difficult to overcome.
No matter where in the world they are located, the largest problem I see facilities facing is not being able to manage their lubrication and reliability program as a whole. When facilities aren’t able to develop lubrication management standardization, there are dire consequences, with one of the most costly and severe being the mixing of incompatible greases.
The Consequences of Mixing Incompatible Greases
Ultimately, the success of a lubrication management program rests on the team’s ability to lubricate bearings with the proper grease at the right time and in the right amount.
Grease is gravely important to understand. If you add a different grease than what was originally used, especially if it is incompatible, this can create massive issues within the machine. Once greases are mixed, they can’t be undone, which can mean unplanned downtime and costly repairs or bearing replacements.
But what exactly happens when two incompatible greases are mixed?
To start, mixing incompatible greases can cause severe damage to bearings. Take a thickener and a base oil, for example. The thickener holds the grease in place, and the base oil lubricates the components. However, if you were to mix two incompatible thickeners, the base oil would bleed out excessively, leading to a catastrophic bearing failure due to starvation.
When this happens in electric motors specially, more often than not, the oil will bleed onto the windings, which act as the insulation for the motor. This will cause the motor to fail at dissipating heat which will lead to overall motor failure. This excessive heat generated from mixing greases can create a potentially very dangerous situation with facility fires or collateral damage.
Did You Know?
From 2017-2021, US fire departments responded to more than 40,000 facility fires where the leading cause was linked to industrial equipment failure.Source: The National Fire Protection Association
In this situation, it’s not just the main machine that you’re worried about; it’s the whole line of machines that are connected to and being driven by that motor. One failing asset affects another asset, and so on, creating a domino effect with severe consequences that must be stopped before widespread damage occurs.
How Does Grease Mixing Happen?
There are several ways greases can mix – most of which stem from simple, preventable errors.
Throughout my career, the number one issue I see is an overall lack of training. Not only will team members not be aware of the current lubricant, but confusion often occurs over which specific lube point they are supposed to lubricate with that grease. This is where lubricant tagging and labeling become crucial to the lubrication program.
Oversights in program management and standardization like this not only open the facility up to an increased risk of maintenance errors but also waste time that many teams don’t have to spare. This includes the time it takes to track down the machine’s true current lubricant and then cross-reference this to uncover the recommended and last-used lubricant, dramatically increasing a facility’s risk of mixing incompatible greases.
Additionally, a lack of standardization quickly causes problems with managing lubrication frequencies and intervals. For example, many facilities operate on a nine-month to one-year regreasing schedule, meaning that if grease is improperly mixed, the issue has a high likelihood of not being caught until the next regreasing cycle.
And even then, many facilities aren’t accurately inspecting their equipment. In this case, the problem may not be caught until failure modes start showing, which can take up to three or four years after the initial grease mixing occurs. By that time, most corrective actions are ineffective, and you could be looking at costly repairs and replacements.
This issue is compounded when you take into account the sheer number of machines a facility has. Throughout my career, most of the smaller plants I visited have no less than 450 assets, which equates to about 1,000 motors that need to be managed and 1,000 chances for grease mixing to happen.
If a facility doesn’t have a great lubrication management system in place, it’s all too easy for team members to become overwhelmed, exponentially raising the likelihood of incorrect lubrication practices and ultimate machine failure.
Painting the Big Picture for Lube Techs
What this all boils down to is a lack of training across the board. But, this isn’t inherently a fault or a character flaw – sometimes, it’s an “unconscious incompetence”. Unconscious incompetence basically means that you don’t know what you don’t know. This is why training is so important for any facility that wants long-term and sustainable success.
No one is immune from this phenomenon. Looking back on my own educational journey, I didn’t know the proper way to grease until I began working at Noria, where they provided me with training. I grew up in the country greasing tractor and trailer bearings, where the mentality was “grease that sucker until the grease comes out.” But, if you apply this same advice to industrial bearings, you’ll blow the seal and cause serious damage.
It wasn’t my fault that I didn’t know, but it would have been my fault if I had known and chosen not to do better. As I tell all the facilities I help, 90% of the time, we are murdering our machines, and at the end of the day, our negligence, either through a lack of knowledge or a lack of effort, does the most damage.
Even though it is often overlooked, training is one of the most crucial parts of developing an effective lubrication program. With training, team members become confident in their understanding of best practices and feel empowered to implement changes that keep machines healthy and create a new maintenance culture.
Changing the Culture
It can take years for a facility to realize it needs help with its maintenance management program. Part of the problem is that although team members, like reliability engineers, understand that lubrication is important, they can’t implement an entire maintenance management program by themselves. They need buy-in from senior leadership and all other team members to get the program off the ground.
Did You Know?
A strong organizational culture increases workforce numbers by 25% over a three-year period and net profit by 85% over a five-year period.Source: Gallup
So, while there may be awareness that the current system isn’t effective, there isn’t anything a single individual or team can really do to permanently correct the issue until everybody is on board and makes changing their practices a priority.
The education and involvement of leadership, such as the plant manager and maintenance supervisors, help create the foundational knowledge that, first and foremost, lubrication is important.
The leadership team will ultimately be the ones responsible for outlining and developing the plan for change. Not only must this plan be developed using best practices, but they must be able paint the big picture for the team. This way, the team knows why these changes are crucial and why they are being asked to change how they have performed lubrication all these years. Without their enthusiastic and educated perspective, there is a risk that the goals and importance of the change plan won’t be communicated effectively.
Additionally, training for team members, such as lubrication technicians, ensures that when these change plans are communicated, they not only understand why the changes are being enacted, but they also have the required skills to make the changes happen and to maintain them.
When a decision is supported by the appropriate actions, that’s when changes begin to have a positive effect on uptime and productivity, which secures the health and longevity of the facility’s critical assets and equipment. Through training, team members at every level discover how important lubrication is to securing sustainable change while learning how to properly implement and maintain a new program.
Measuring Success
Once a change plan is in place and all teams are doing their part, it’s important to communicate progress and results effectively. This means tracking Key Performance Indicators (KPIs) and metrics and regularly posting the results somewhere everyone can see them.
By posting the results, every team member is on the same page and clearly understands how their role contributes to successfully reaching the facility’s goals. It also brings the added benefit of boosting morale and encouraging best practices, no matter how tedious they can feel, because the team can see the positive results of their hard work.
At the end of the day, it’s the small things team members didn’t realize mattered that make the biggest impact, and now facilities will have the data to prove it.
Keeping Up with the Times & Technologies
It’s one thing to share the data with the team and another thing entirely to collect it. It is management’s responsibility to stay up with the times when it comes to the best way of collecting this data. This means that instead of relying on a traditional paper-and-pencil system, facilities should transition to using devices.
Whether it’s a cell phone, tablet, or computer, every team member across the entire facility needs to have access to one. This allows everyone to not only track progress in real-time, but also get the information they need right at their fingertips. Technology also cuts down on missing or incorrect information, confusion, and the doubling of efforts, all while reducing the risk of tasks being forgotten or performed incorrectly.
This real-time collection and exchange of information provides several benefits. For instance, it can be used to analyze maintenance management program success. It also guides maintenance and lubrication efforts by alerting team members to when an asset needs lubrication, as well as what kind of lubrication is needed and how much should be applied. This ensures all assets are being properly relubricated at the right time, cutting down on machine failure and associated costs.
At the end of the day, all facilities rely on their machines to drive critical operations, and there is zero room for error. Technology is a low-cost investment that creates a quick, high return for everyone. A single iPad can cost as little as $400, and this iPad can be equipped with industry-specific applications to help manage maintenance and lubrication operations.
When you consider that a machine or component failure can easily cost $60,000 or more to repair or even replace, not including the loss of revenue from downtime, the $400 investment seems worthwhile. Everything is all right there in the palm of a team member’s hand.
At the end of the day, every small decision we make with conscious, intentional effort, such as training, data collection, and lubrication program development, creates lasting change, allowing facilities to properly care for the critical assets that are a business’s lifeblood.
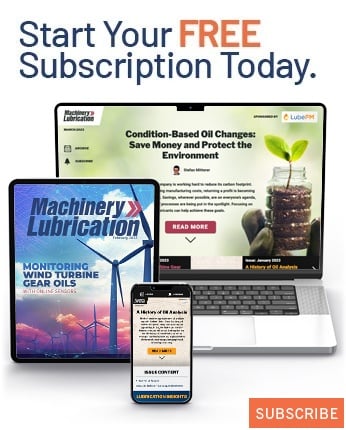