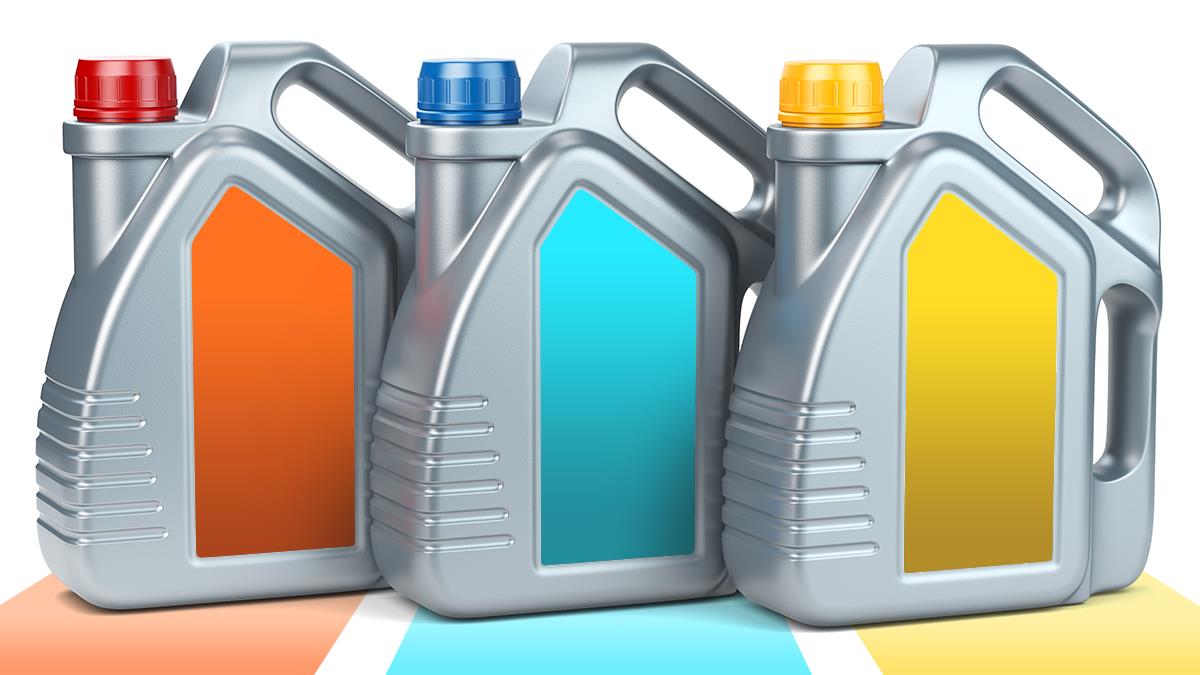
Proper lubricant selection is more than a simple maintenance task; it’s at the heart of keeping industry moving. Contained within all moving machinery, lubricants are their very lifeblood, supporting and propelling industries worldwide.
Proper lubricant selection plays a pivotal role in achieving facility goals. By selecting the appropriate lubricant for each application, facilities can enhance overall equipment lifespan, reduce energy consumption, improve operational efficiency, and
minimize the risk of unplanned downtime.
By understanding what goes into selecting a lubricant, facilities can choose the right one for the job, reap long-term business benefits, and enjoy healthier, more predictable operations.
Understanding Machine Needs
From a holistic viewpoint, few processes have as direct an impact on downtime rates, machine health, and the overall maintenance budget as lubricant selection. This is why experts consider this one of the most crucial decisions any maintenance program can make.
Every lubricated asset is precisely designed to accomplish a specific task, and choosing the correct lubricant for that asset is the best way to ensure its proper function and protect both the asset and the company's investment. A single mistake in the selection and management of lubricants can
cause the wrong lubricant to be applied to critical equipment, causing premature failure of the machine and bringing a halt to the operations it supports.
While selecting a lubricant can seem deceptively simple, it’s critical that selection decisions are not made lightly. Small errors in lubricant selection can result in huge long-term consequences, often because these mistakes go unnoticed until it’s too late to fix them. Furthermore, factors like lubricant formulation and production constantly evolve as new data and technologies emerge. To properly select lubricants, a facility's selection process must keep up and not rely on outdated standards and recommendations.
But before a lubricant is chosen, a team must fully understand the needs of the equipment being lubricated. While
Original Equipment Manufacturer (OEM) recommendations can be an adequate place to start, additional checks must be in place to ensure the recommended lubricant is a viable option. Many facilities find it necessary to make adjustments to their selection criteria based on their equipment's unique operating parameters, including:
-
Speed
-
Load
-
Operating temperature
-
Internal surface materials
-
Environmental conditions
-
Contamination potential
-
Food-grade or environmental requirements
Each of these parameters must be considered and balanced against lubricant availability and overall price.
Many facilities looking to cut costs often consider purchasing cheaper lubricants. However, this is often ineffective from a profitability perspective and risky as a maintenance decision. On average, lubricant costs only make up
approximately 1-3% of a facility's annual maintenance costs, and total maintenance budgets average 8-10% of total operating costs. This means that for every dollar spent by the company, lubricant purchasing would only make up 1/10th of a penny.
Obviously, when viewed from such a high level, lubricant selection does not demand a large portion of a company's annual budget. However, this doesn't mean that maintenance will automatically have access to the appropriate budget it needs. In these instances, decision-makers must make well-informed and appropriate decisions for their equipment while respecting pre-set spending limits.
Ultimately, the cost of the lubricant itself is a small fraction of the cost of the unscheduled downtime that could cripple production when machines fail. However, the lubricant is only the medium by which lubrication occurs; it’s up to the maintenance team to incorporate it into an effective strategy that also considers things like
proper contamination control and management of lubrication tasks.
The 3 Lubricant Categories
Once the asset’s needs are fully addressed, the next criterion that should be considered is the lubricant’s performance level. Most lubricants fall into
three main categories: standard-performance, high-performance, and specialty-performance. Understanding their differences and appropriate applications is crucial to ensuring a facility is making the right selection.
Standard Performance
Often offered as bulk purchases that help minimize cost, standard performance lubricants are the most common type in use. They are broad solutions that perform the basic functions required to meet most OEM minimum operating requirements. It is estimated that approximately 80% of all mechanical components can be effectively lubricated with standard-performance products.
High Performance
High-performance lubricants are manufactured using specialized materials that offer enhanced capabilities. Some address specific performance needs, such as heavy load support,
high wear resistance, or extended lifecycle needs. Selecting a higher-performance lubricant is usually appropriate for 18-20% of all mechanical components.
Specialty Performance
These products are specifically designed for extraordinary circumstances. For example, in nuclear power environments, extreme operating temperatures, operations in a vacuum or low-gravity, or in facilities regularly working with highly corrosive materials. Each specialty lubricant is designed with a specific environment or specification in mind and should be both chemically and physically stable in those situations.
However, certain disadvantages do exist. In many situations, these lubricants typically can't support a
variety of valuable additives. Cost is also a factor – these lubricants can be cost-prohibitive, often 200 to 400 times more expensive than typical lubricants. That said, most facilities won't ever have the need for these types of products (and if they do, the cost is usually justifiable). Specialty performance lubricants are only used in 1-2% of plant applications across all industries.
Conclusion
In an era of increasing operational complexity and steady competition, proper lubricant selection should not be considered as a mere maintenance task; it's a strategic investment that should be carefully considered. Cultivating this perspective as part of a well-informed and data-driven lubrication program, facilities can unlock significant operational advantages. By taking into account specific equipment needs, exploring lubricant categories, and balancing performance with price, facilities can optimize equipment lifespan, enhance efficiency, gain a competitive edge, and minimize operating costs.
Obtaining certification can be a challenge; new terms, concepts and topics can overwhelm even the most experienced reliability professionals. Training experts all agree that extending the learning beyond the classroom dramatically increases knowledge retention. To aid in this retention and create an innovative student experience, Noria is pleased to offer the Noria Academy app.
RelaWorks 1328 E. 43rd Court, Tulsa, OK 74145 918-392-5058 | RelaWorks.com
Finding the right products can be difficult. Every industry and application is unique. Over-spending and guess work is common. At RelaWorks, we help reliability professionals solve this challenge. Our mission is to provide products for your unique needs and budget. Backed by Noria Corporation’s expertise and legendary customer service, we’re excited to help your reliability program succeed.
LubePM 1328 E. 43rd Court, Tulsa, OK 74105 800-597-5460 | LubePM.com
As a Lubrication Management System (LMS) engineered by lubrication professionals, LubePM helps an organization create accountability to ensure that every lubrication point is carefully maintained, inspected and measured. Ready to take your facility’s Lubrication Management System to the next level with LubePM? We’re ready to help. Simply request more information or schedule a demo.
About the Author