Like so many attendees in a Noria training class, Bill was no exception. When asked why he was there, he replied, ‘To learn a little more about oil analysis, so I can get the full value from my oil analysis program.’
A little later, in a side conversation, Bill was heard to lament the fact that he recently had to rely on his vibration analysis to spot a failing gearbox at his paper mill. The fact that no single technology is capable of detecting all of the problems in all of the machines is why integrated technology condition monitoring is crucial. Nevertheless, Bill, who was responsible for the oil analysis, naturally wanted his program to stand proud, so missing a failure left him frustrated. Fortunately for the class, he had brought along copies of his oil analysis report relating to this unit.
“No single technology is capable of detecting all of the problems in all machines, which is why integrating technology condition monitoring is important.” |
These reports were a good learning tool to introduce in the interactive session. Look at the report and see if you can spot the problem.
Bill explains:
“This gearbox is used under our slusher tank, which holds up to approximately 30 tons of pulp. The pulp is loaded in from a conveyor above the tank, in 3-foot square blocks, which is then broken up into slush by the agitator, which the gearbox drives. As you can imagine, it is an extremely tedious process considering it has to start and stop up to 100 times in 24 hours. If this box breaks down, then the entire papermaking operation onsite is down at the rate of $4,500 an hour. We do have a spare box but it takes six hours to carry out a change. This failure cost about $12,000 to repair, and the price of a new gearbox is about $45,000. “
There is an oil cooler attached to this box and the oil is pumped up to the output drive internally. The tank above slushes water consistently and often leaks water onto the top of the box. We have fitted various seals to try to stop this and have had some success in doing so.
“We carry out vibration monitoring on this machine every two weeks, and noted a rise in an output drive bearing defect frequency and decided to analyze the oil. However, we had taken our next set of readings before sample diagnosis came back and this showed a further rise in bearing vibration amplitude, so we took another oil sample and sent it away requesting an urgent reply. However, because the vibration readings were climbing, we took readings a couple of days later and found an alarming increase in the output drive bearing defect frequency and decided to shutdown and change the gearbox.”
Check out the report below:
31/08/99
16/11/99
04/04/00
Have you spotted the root cause yet?
Now read the report and comment for September 2000 received after the change out: “The sample contains 0.6 percent water contamination. Identify source of ingress. Extremely elevated levels of iron allied to the PQ Index (ferrous wear) indicate severe wear occurring in this unit. Flush unit to reduce debris and renew lubricant.”
To an analyst, the location of this gearbox immediately calls for a close watch on water ingress at all times. To a proactive maintenance practitioner, this situation calls for upgraded seals and desiccating breathers, or sealed expansion chambers. It also calls for quick-connects for the easy flushing/dehumidifying of the unit, or a permanent off-line filtration unit. Bill now appreciates from the course that there are a number of areas for improvement here, and the cost of implementation is a lot less than a new gearbox.
Bill plans to set target cleanliness levels for the unit to cover both particle counts and moisture. In this demanding environment, these targets need to be as tight as possible to ensure maximum lubricant and machine life.
Second, apart from the upgraded seals, Bill needs to look at the breathers and filtration. Because there is a pumped internal circuit, this could be utilized for a filter, although the easier option would be to fit a permanent off-line circuit that can run independent of the gearbox operation allowing the filter to be changed on the run. This circuit should have an appropriate sampling port downstream of the pump and upstream of the filter. Secondary sampling ports may also be an option on the sump and on the drain port to check for sludge build up, or free water.
Finally, Bill needs to monitor the condition of the lubricants more frequently to ensure compliance within the targets, and plan a site-based screening approach to check the contamination levels and the basic lubricant properties including viscosity.
A few more improvements that Bill plans to make include the baselining of his samples. He needs to get a new oil sample annually to use as a benchmark for his additive depletion and compliance check. He should also plan to record all the information necessary for the accurate analysis, such as the number of hours the unit has run, the number of hours the oil has run and whether any additional oil has been added, including what volume since the last sample.
Long term, he should consider whether this is the most appropriate oil for this application, whether high-quality oil might offer greater life and reliability from the unit.
Bill now appreciates what he could have done earlier to save the gearbox before the bearing actually failed, and reduced his costs significantly.
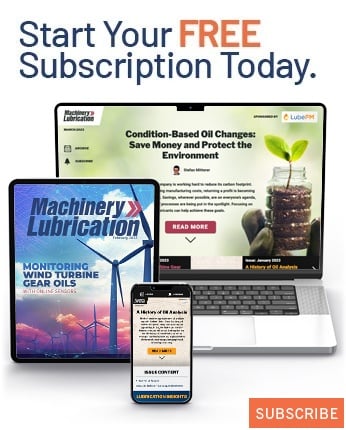