What is Micropitting?
Many gears are plagued by micropitting. Although micropitting is not a new phenomenon, its significance has not been widely appreciated, and at times it was thought to be harmless. However, it is now recognized as damaging to gear tooth accuracy, and in some cases, a primary failure mode. Micropitting is surface fatigue occurring in Hertzian contacts, caused by cyclic contact stresses and plastic flow on the asperity scale.
It results in micro-cracking, formation of micropits and loss of material. Micropitting is also referred to as fatigue scoring, flecking, frosting, glazing, gray staining, microspalling, peeling and superficial spalling. However, micropitting is the preferred name because it aptly describes the appearance and mechanism.
All gears are susceptible to micropitting, including external, internal, spur, helical and bevel. Micropitting can occur with all heat treatments including through-hardened, carburized, induction-hardened and nitrided. It is common with carburized and ground gears because loads are usually high and ground teeth are especially vulnerable to micropitting.
Currently, there is no recognized analytical method to assess the risk of micropitting. However, this article gives guidelines developed from experiments and inspections of laboratory and industrial gears to help engineers select and apply lubricants to avoid micropitting.
How to Recognize Micropitting
Appearance
To the unaided eye, micropitted gear teeth appear dull, etched or stained with patches of gray. Micropitting is difficult to see under diffuse fluorescent lighting and is best observed with intense directional lighting. A flashlight with a concentrated beam held in the proper direction effectively illuminates micropitting. With intense lighting, micropitting may sparkle or appear speckled.
Occurrence
Micropitting begins as surface contact at high points on gear tooth surfaces, such as crests of undulations, peaks of cutter scallops, ridges of grinding lay and edges of grinding scratches where maximum peak-to-valley roughness of tooth surface may be about two to four mm.
Micropitting may occur at edges of teeth and boundaries of surface defects, such as scratches and dents. It may also occur adjacent to damage from other failure modes such as macropitting or scuffing, and anywhere lubricant film is disrupted.
Multiple cracks originate at these sites and coalesce to form micropits along lines that follow high points of surface topography. If ridges are periodic, micropitting may form in regularly spaced rows. Micropitting generally progresses until surface peaks are removed, and may continue until large areas of tooth surface appear porous and continuously cracked.
Gear teeth dedenda (the portion of the tooth below the midpoint or pitch line of the tooth) are vulnerable to micropitting, especially along the start of active profile (SAP) and the lowest point of single tooth contact (LPSTC). However, micropitting may occur anywhere on active flanks.
When micropitting damage varies from tooth-to-tooth, it usually means there are variations in tooth geometry or surface roughness from tooth-to-tooth. Gearsets with nonhunting gear ratios may develop micropitting patterns that repeat at the frequency of a common factor. For example, a gearset with a 20/45-tooth combination may have similar micropitting on every fifth tooth. Generally, the gear with the roughest surface causes micropitting on the mating gear, especially if it is harder than the mating gear.

Micropitting Starting on Peaks of Cutter Scallops
What Causes Micropitting
Micropitting occurs under elastohydrodynamic lubrication (EHL) oil films where film thickness is of the same order as composite surface roughness, and the load is borne by surface asperities and lubricant. When a significant portion of load is carried by asperities, collisions between asperities on opposing surfaces cause elastic or plastic deformation depending on local loads.
Incubation
In addition to contact stress due to normal loading, sliding between gear teeth causes tractional forces that subject asperities to shear stresses. The first 104 to 106 cycles of stress occurring during run-in are an incubation period during which damage consists primarily of plastic deformation at asperities.
Cyclic contact and shear stresses accumulate plastic deformation on asperities and at shallow depths below asperities. Plastic flow produces tensile residual stresses and with sufficient cycles, initiates fatigue cracks.
Nucleation and Growth
After incubation, micropits rapidly nucleate, grow and coalesce. Microscopy shows a continuously cracked surface. Periodic inspection of tooth profiles with a gear inspection machine discloses a steady rate of surface deterioration. The process of plastic deformation, followed by initiation, growth and coalescence of cracks may be continuous. Damage may be extensive after only 106 cycles.
Micropitting begins when a fatigue crack grows from the gear tooth surface at an angle to the surface. A micropit forms when a branch crack connects the subsurface main crack with the surface and separates a small piece of material. The resulting pit may be only 10 mm and not resolved by the unaided eye. Subsurface crack networks are usually more extensive than would be implied from surface features.
The main crack undermines the surface by growing deeper and spreading in a fan-shape. Micropits enlarge as back edges of pits crack and small pieces of surface material are dislodged. Debris from micropitting can be as small as 1 mm, and may not be removed by strainers. The particles act as polishing agents and polishing wear is often found on gear teeth with micropitting, both in areas between micropits and in areas without micropitting.
Lubricant Effects
Lubricant properties such as basestock, additive chemistry and viscosity affect micropitting. Tests show micropitting resistance varies from lubricant to lubricant. Some lubricants may be capable of arresting micropitting after it has started.
Base Oil Properties
Oil solidifies under high pressure generated in EHL contacts, and tractional stress on surface asperities is limited by the shear strength of solidified oil. There can be significant differences in solidification pressure and shear strength among various lubricants and therefore differences in their tractional properties exist.
For instance, polyglycols and esters have molecules with flexible ether linkages and lower shear strength than hydrocarbons. Naphthenic mineral oils have relatively stiff, compact molecules that generate high traction, whereas paraffinic mineral oils and polyal- phaolefin (PAO) synthetic oils have open, elastic molecules and low traction coefficients.
PAOs and nonconventionally refined mineral oils have significantly lower traction coefficients than conventionally refined mineral oils. Many PAO synthetic oils are blended with esters to increase solubility for additives. Unfortunately, esters have affinity for water, and micropitting resistance of PAO oils may decrease if contaminated with significant quantities of water.
Micropitting can occur with mineral or synthetic lubricants. At high temperatures, PAO and PAG synthetic oils have thicker EHL films and higher micropitting resistance than mineral oils with the same ISO viscosity grade and additives. For gear tooth temperature in the range of 70°C to 90°C, there is little difference between EHL film thickness of mineral and PAO lubricants, whereas PAG lubricants have significantly thicker films.
Additives
Antiscuff (EP) additives are often necessary, but can be chemically aggressive and may promote micropitting. Oils without antiscuff additives have maximum resistance to micropitting.
Experiments show widely varying, and sometimes conflicting, results for the influence of additives on micropitting. For example, some tests show antiscuff additives containing sulfur and phosphorus (S-P) promote micropitting, whereas other tests seem to prove S-P additives impart resistance to micropitting.
Additive activation temperature may cause some variation if tests are conducted at different temperatures because additive performance depends on the operating temperature of gear teeth. For this reason, a lubricant’s micropitting resistance (basestock and additive composition) is best determined from field tests with industrial gears. Laboratory tests should simulate industrial gears and actual operating conditions as closely as practical.
Viscosity
Low viscosity reduces fatigue life by reducing EHL film thickness and promoting hydraulic propagation of cracks. High viscosity oils have higher micropitting resistance because they have thicker EHL films and less tendency to promote hydraulic propagation of cracks. However, viscosity must be limited because excessively high viscosity may cause high temperature, excessive energy loss, or high oxidation rate without a significant gain in operating viscosity.
Additive influence can overwhelm viscosity effects. Therefore, increasing viscosity may not help if micropitting is promoted by aggressive additives.
Debris
Lubricant-borne solid debris much larger than EHL film thickness can be entrained between gear teeth due to rolling action. Once into the contact, debris is subjected to enormous pressure. Brittle debris fractures into smaller pieces, with some particles embedding in gear tooth surfaces, and other smaller fragments passing through the contact. Tough debris larger than the film thickness is able to pass through the contact by the combined effects of debris flattening and tooth surface denting.
Dents caused by brittle debris tend to be relatively small in area but deep, and edges of dents are sharp. In contrast, dents caused by tough debris tend to be relatively large in area, shallow and with a smooth floor. Dent edges are smooth and raised above the tooth surface forming ridges that outline dents.
Debris dents are local depressions that cause loss of EHL film thickness and lead to stress concentrations around edges of dents. Cyclic contacts at these sites generate pressure spikes, plastic deformation and tensile residual stresses that eventually initiate micropits.
Manufacturing debris is not immediately removed by filters. Permanent debris dents may occur during run-in unless gearboxes are assembled in a clean environment and filled with clean lubricant. Furthermore, cleanliness must be maintained during service. Table 1 gives guidelines for oil cleanliness designed to ensure adequate cleanliness of new oil, gearbox assembly and gearbox operation.
Water Contamination
Many experiments have shown that wet oil promotes micropitting. The mechanism is unproven, but thought to be due to hydrogen embrittlement. All lubricants are susceptible to water contamination, but ester-based lubricants and mineral oils with antiscuff additives are especially prone to absorbing water, and generally give lower fatigue life with high water content.
Elastohydrodynamic Lubrication (EHL)
Gear teeth are successfully lubricated by EHL because teeth elastically flatten and oil viscosity increases exponentially under high Hertzian pressure. Elastic flattening creates a converging zone at the contact inlet. Oil adhering to gear teeth is entrained into the inlet zone and subjected to an increasing pressure that dramatically increases viscosity and builds an EHL oil film.
Film Thickness
Oil film thickness is determined by the oil’s response to the shape, temperature and velocity of the surfaces at the contact inlet. Higher load causes increased elastic flattening without significantly changing inlet geometry. Therefore, film thickness is insensitive to load and elastic properties of gear teeth.
In contrast, film thickness depends strongly on entraining velocity and oil viscosity. Although transient temperature flashes occur in the central region, film thickness depends on gear tooth equilibrium temperature and not flash temperature.
The central region of contact is a relatively long, thin gap that carries most of the load. Once into the central region, oil cannot escape because viscosity is very high, the gap is thin and contact time is extremely short. Essentially, all entrained oil travels through the contact as a solid sheet of uniform thickness. At the contact exit, oil reverts to its atmospheric properties.
An ideal gear lubricant would have high viscosity, high pressure-viscosity coefficient (a), and low traction coefficient (m). Unfortunately, high viscosity increases oil’s frictional heating in the inlet, which tends to reduce viscosity, and oils with high a tend to have high m.
Micro-EHL
Modern computers, 3-D maps of surface topography and efficient numerical techniques have enabled analysts to explore the effects of surface roughness on EHL contacts. Rough surface topography of real surfaces, including transversely ground, longitudinally ground and a shaved surface with nearly isotropic topography has been investigated.
The studies show surface topography and orientation have significant effects on asperity contact area and asperity load sharing, but negligible effects on average film thickness. Therefore, surface topography influences micropitting principally by causing a change in asperity interaction, and not by altering oil film thickness.
Specific Film Thickness
Specific film thickness, l, is the ratio of EHL film thickness to composite surface roughness of the gear teeth as defined by the following equation. It is a means to estimate lubrication regime and assess severity of asperity contact.
Prevention of Micropitting
The following guidelines summarize methods for mitigating and preventing micropitting. Not every measure may be achievable or applicable for a given application, but as many as possible should be implemented.
Maximize Specific Film Thickness Increase Oil Film Thickness:
- Use highest practical oil viscosity.
- Run gears at high speed.
- Cool gear teeth.
- Use synthetic oil if gear tooth temperature is greater than 80°C.
Reduce Surface Roughness:
- Coat teeth with iron-manganese phosphate, copper or silver.
- Run-in with special lubricant.
- t Pre-filter lubricant and use a fine filter (£ 6mm) during run-in.
- Keep oil cool during run-in.
- Run-in gears using a series of increasing loads and appropriate speed.
- Drain lubricant and flush gearbox after run-in, and change the filter.
Optimize Lubricant Properties
- Use oil with high micropitting resistance as determined by test.
- Use oil with low traction coefficient.
- Use oil with high-pressure viscosity coefficient.
- Avoid oils with aggressive antiscuff additives.
- Keep oil cool.
- Keep oil clean of solid contaminants.
- Keep oil dry.
Parameters Controlling Micropitting
Load
Olver has reported that micropitting wear rate increases and incubation life shortens with increasing load. However, the author has found micropitting on lightly loaded gears, and even on backsides of teeth where loads were light and infrequent. Therefore, load is not a strong influence, and high loads are not necessary for micropitting to occur.
Speed
Gear teeth roll and slide on one another. Rolling velocity is beneficial because it entrains lubricant between contacting teeth, increases oil film thickness and reduces severity of asperity contacts. Sliding velocity, on the other hand, generates heat and increases asperity distress.
Temperature
Gear tooth equilibrium temperature is relevant to micropitting because it influences EHL film thickness and additive activation. The equilibrium temperature is established by the balance between heat generation caused by friction and churning, and heat dissipation caused by conduction and convection. Tooth temperature of high-speed gears may be significantly higher than the temperature of oil supplied to the gears.
Micropitting resistance generally decreases with higher gear-tooth temperature. However, some lubricant additives may actually improve micropitting resistance as temperature increases. This observation emphasizes the importance of running micropitting tests at temperatures relevant to the particular industrial gear.
Micropitting damages surfaces of gears beginning at the asperity contact points and propagating through gear surface cracks. Micropitted gear teeth appear dull, etched or stained with patches of gray. Micropitting incidence increases relative to surface finish (hardness and topography), load, speed and temperature. Various lubricant properties influence any lubricant’s ability to control micropitting, including base oil viscometrics, additive type and composition, and type and extent of lubricant contamination. Proper treatment and gear operation at the run-in stage can influence susceptibility to micropitting.
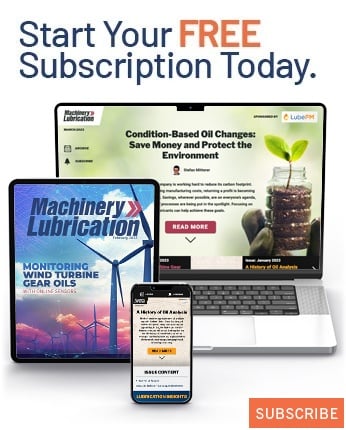