A fluid’s viscosity is one of its most important physical properties. Significant change in an oil’s viscosity is meaningful and should not be ignored. Therefore, it is a mistake to underestimate the importance of viscosity alarms and limits.
Baselining New Oils
The importance of establishing a baseline for viscosity monitoring cannot be over-emphasized. The ISO viscosity grade classification system (ISO VG 32, 46, 68, etc.) is merely a nominal value that establishes the midpoint of an acceptable viscosity range. Actual viscosity values may vary from this midpoint by ±10 percent and still be considered conforming (within grades).
Similarly, viscosity values for individual manufacturers’ products will vary by batch and even container. Published values on a specification sheet are typical values and are often not precise.
To be effective, all alarm and limit values must be referenced to a starting condition known to provide acceptable performance. If specification viscosity values or ISO VG midpoint viscosities are used to established alarms, sensitivity is lost and false alarm rates may increase.
The most common alarm variation in viscosity is within 5 percent of the new oil’s baseline viscosity. For example, a particular ISO VG 32 lubricant is specified by the manufacturer to typically have a viscosity of 31 cSt, well within the limits of the viscosity grade (28.8 cSt to 35.2 cSt). An upper alarm is set at +5 percent, for a value of 32.6 cSt. Individual deliveries of this lubricant may have varying initial viscosities, which will make the actual alarm setting more or less than the intended 5 percent.
If alarms are based upon the nominal ISO VG viscosity of 32 cSt, a product at the upper end of the allowable viscosity range will tend to have upper alarms triggered too frequently, or even at delivery. Remember that a product may exceed the midpoint by 10 percent and still be within grade. This may cause an unnecessary alarm - a false positive.
Alternately, if a product is blended to be only 30 cSt when new, a viscosity increase of 8.67 percent would be required to trigger any further investigation. In this case, conditions that were intended to trigger an alarm-viscosity values elevated by 5 percent - do not, and therefore appropriate corrective action will likely not be taken, resulting in a false negative.
Alarms vs. Limits
The purpose of alarms is to indicate that something unfavorable may have occurred. This may prompt further investigation and/or testing, perhaps resulting in a maintenance action. Alternately, an alarm may trigger closer and more frequent parameter monitoring.
Alarms should stimulate further interest and initiate appropriate action. They should not, in most cases, be a cause for panic. In the case of viscosity, an alarm might trigger a retest by a more precise testing method, or simply a confirming retest using the same viscometer. Further oil analysis tests are often needed to investigate potential causes of a viscosity change so that they, and not the symptom, may be addressed.
In Figure 1, such an example can be seen in the data from Nov. 8, 2000. A retest failed to confirm the alarm, and therefore no other maintenance action was required.
Figure 1
Cautionary limit values should be set at some level sufficiently within the boundaries of safe values that do not compromise functionality. Exceeding a critical limit, such as low viscosity, should trigger immediate corrective action to avoid damage to the protected system. For example, an out-of-limit viscosity measurement might trigger an oil change.
As indicated in the previously referenced viscosity article, viscosity alarms and limits must be bidirectional. Elevated and depressed values can equally indicate problems. (Refer to the referenced article for a discussion of the significance of each change in value.)
Trending Viscosity Values
Plotting viscosity values over time allows the investigator to identify potential trends even before cautionary or critical alarms are triggered. Viscosity values that continuously trend downward over several readings may arouse the investigator’s curiosity if viscosity is expected to rise over time, or vice versa.
Plots in which viscosity readings are plotted over time are known as time plots (Figure 1), and can be used to establish alarms and limits, as well as identify trends. When creating such plots, the x-axis is typically used to convey the passage of time.
The y-axis then indicates viscosity values returned from the oil analysis tests. Individual viscosity values are plotted versus the date the sample was taken, not the date the analysis was performed. Usually, viscosity is trended for each machine or sump individually, however some alarms and limits intended to apply globally to a group of similar machines will have all values plotted together as a scatter diagram (no lines connect data points).
Other information that may be included on such a plot are factors that could be responsible for variations without being a cause for concern. While there are many examples that are often application-specific, a common one would be the dates when make-up volume was added to a system.
When trending viscosity, make-up volume may result in false alarms if the initial viscosity of the make-up lubricant is significantly different than that of the original fluid. This can be due to normal product variations, oil degradation or contamination.
Types of Alarms and Limits
The most commonly applied viscosity alarms are based upon a set measure of change. Usually, these are based upon a percentage change from the baseline value, though in some applications, absolute differences may be used. The most common rules of thumb for fixed percentage viscosity alarms and limits are ±5 percent (cautionary) and ±10 percent (critical), respectively.
The power and accuracy of these alarms and limits can be improved by incorporating other analysis methods such as rate-of-change and acceleration calculations and plotting. When viscosity versus time is plotted, the rate-of-change is determined by dividing the amount of viscosity change during a specified time period by the time over which that change occurs.
This will be the slope of the curve for that period (the first derivative of the viscosity-time function). If the rate-of-change (slope) of the viscosity-time plot is evaluated for each intervening period, the rate-of-change plot is created (Figure 2).
Figure 2.
If it establishes a somewhat consistent rate-of-change, it can be used to predict the time at which the viscosity may be expected to reach the actual alarm or limit value.
In the example provided, the viscosity is low enough that the rate of change, which is in the direction of the limit, warranted an oil change because the viscosity could be expected to fall below the lower limit before the next scheduled analysis.
Alternately, the analysis interval could have been shortened to keep a closer eye on this situation as it developed. Note that on the sample collection date, May 7, 2001, the viscosity was still above the limit value by about 0.6 cSt; however, the viscosity was dropping at a rate of more than one cSt per month.
When using this technique, it is important that only data collected at roughly regular intervals, such as monthly, be used in the calculation of rates-of-change; otherwise, random fluctuations in data can cause a large rate change that will overshadow potentially significant changes in the actual viscosity. This information is most relevant when used in conjunction with the viscosity-time plot as indicated in the previous example.
Was it likely or probable that the viscosity would have continued to drop? If slopes are calculated for the viscosity rate change plot, the acceleration (2nd derivative), which may also be plotted versus time (Figure 3), is determined.
Figure 3.
Continuing with this same example, the viscosity is dropping at increasing rates (accelerating) as indicated by the increasing absolute values of the plot in Figure 3. Therefore, it is of greater concern because an unstable situation is developing. Had the acceleration plot been returning to zero or even turned positive it would be reasonable to consider that the viscosity may in fact be re-establishing a new stable value within acceptable limits. If this was the case, the analyst in the example might have suggested more frequent analysis rather than an oil change.
Selecting Alarm and Limit Values
As previously mentioned, alarm and limit values may be set at absolute or percentage change values. How should these be determined? These informal methods utilize an inherent human understanding of more formalized statistical approaches. While many rigorous statistical methods are available for establishing alarm values, the power of a simple trend plot for setting alarms and limits or discovering trouble should not be ignored. Even the inexperienced eye can identify what is normal versus what is not when viewing a dataset presented in this way.
Figure 4. #3 Turbine Viscosity Frequency Plot During Baseline Period
Frequency plots or histograms (Figure 4), which plot the number of times a returned value falls within given ranges, are also useful for establishing limits by identifying expected values and variability. Random variations resulting from sampling, operating and testing imperfections result in random variations in returned values.
For viscosity measurements they will, however, tend to distribute themselves over a relatively narrow range of values. Setting alarms outside these expected ranges avoids unnecessary false alarms. Statistically-based methods, such as the one discussed above, are often used with oil analysis software packages due to the number of required calculations. Spreadsheets may also be used to provide automation and generate plots.
Responding to Nonconforming Results
When a properly set viscosity alarm is triggered, an opportunity exists to further investigate the cause of the nonconformance. Perhaps a more aggressive analysis interval, a retest for confirmation or further testing is warranted. Regardless of the action taken, an alarm that is not outside the limit is generally not a cause for panic, but rather a measured and appropriate response. It should be a yellow flag - an early warning of trouble that may be developing.
The Practicing Oil Analysis articles mentioned in the beginning of this article discuss several potential causes for viscosity changes in lubricating fluids. While they do not contain an exhaustive list, they do address the most common causes.
A review of all current and relevant information available should be the first step in the investigation. While this may seem obvious, in our haste to creatively solve problems, we too often overlook the obvious facts on hand. For instance, when was make-up oil volume last added? How much was added relative to the total sump volume? How certain are we that the correct product was added at that time? What other oil analysis tests were run in addition to viscosity? Was the sample inspected for color, clarity and odors before it was analyzed?
The investigation should serve to eliminate all potential causes via evidence available, and, if necessary, prescribe needed additional testing. If only one possible cause remains, it is the likely culprit. If no likely causes remain, then the investigation should shift its focus to look at less common causes. This is the basis of all scientific investigations.
Onsite vs. Off-site Viscosity Measurement
Onsite viscometry is a great early warning and screening tool, especially for verifying new oil deliveries. One study suggested that up to one in 40 drums of new oil is delivered with incorrect packaging information, indicating either an incorrect viscosity or base oil/additive blend.
Onsite oil analysis, including viscometry, increases an organization’s awareness of its oil analysis program’s goals, methods and requirements, often resulting in improved support and interest. Onsite viscometry is a useful prescreening method for identifying problems before ordering more complete testing, and it can be a cost-effective way to implement oil analysis.
Despite its many benefits, onsite analysis is not perfect. Some inexpensive viscometers may be less accurate than laboratory-quality models and many do not conform to ASTM standards for test methodologies. It is important to understand these limitations so that errors are not made when attempting to trend data derived from multiple sources. (For more information on the limitations of onsite viscometers, please see the previously referenced article, “Understanding Absolute and Kinematic Viscosity.”)
Techniques exist for improving the effectiveness of value and percent change viscosity alarms. Viscosity alarms must be set bidirectionally. Plotting values over time allows the investigator to identify potential trends in values even before value-based alarms are triggered.
Other information that can be included on such a plot are those factors that may be responsible for variations in the parameter that may not be a cause for concern. To be effective, all alarm settings must be referenced to a starting condition that is known to provide acceptable performance. The importance of establishing a baseline for viscosity monitoring from the new oil cannot be overemphasized.
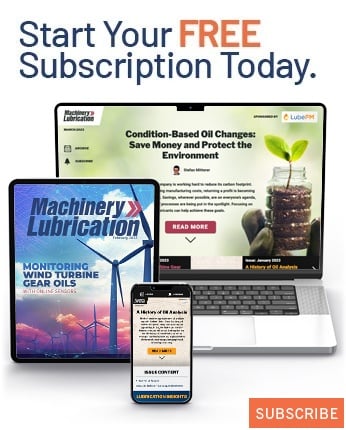