I encountered an unusual situation during my career as a maintenance inspector for a large regional airline that flew mostly turboprops. Oil analysis on turbine-powered aircraft flying scheduled commercial airline routes continued to show unusual amounts of iron. Inspection revealed no abnormal wear of lubricated components.
The shavings were probably in the 6 to 10 micron range, a size detectable by our spectrometric oil analysis program (SOAP) lab. With a little creative brainstorming we focused our attention on a source containing metal - the oil can! Further investigation revealed that the technician was using a church key type can opener on the oil containers instead of the proper oil spout.
When the technician used the church key to open each one-quart oil can to replenish engine lube oil, microscopic metal shavings were sheared from the can’s unlubricated surfaces and the cutting edge of the church key. These foreign elements were then deposited into the product, the engine, and ultimately in the oil analysis report.
The solution was to use a lubricated oil spout to pierce the metal container holding the turbine oil. Normal use of the oil spout kept sufficient oil on the cutting edge to reduce deposition of metal into the product.
Even this procedure may cause trace debris to transfer into the oil. If metal containers must be used, it may be prudent to take a sample from a newly opened container using an established standard opening procedure. A better solution is to eliminate metal containers that must undergo shearing action in order to be opened.
Metal shavings in airplane engines could be a dangerous thing. Thankfully, however, this condition was merely an oil analysis headache. Once make-up oil was dispensed properly, oil analysis data returned to normal.
Submitted by Robin S. Kurth, Senior Technical Support Manager - Power, Pacific Bell
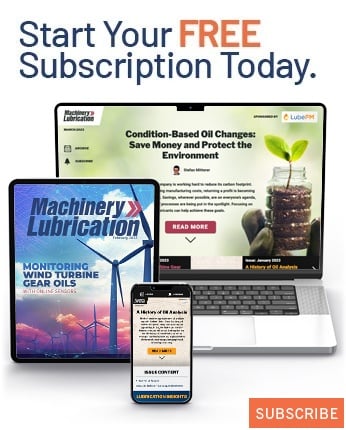