Sometimes it is necessary to quickly determine if a machine is generating an unusual amount of wear debris. One way to accomplish this is to simply pull a patch and look at the particles with a simple top-light microscope. Wear particles tend to be shiny because they reflect light, especially freshly generated particles that have not had a chance to oxidize.
Sometimes, however, one needs to separate the wear particles from the dirt particles to get a clearer view. Here is an easy on-site method for separating magnetic debris (e.g., iron and steel) that is quick and inexpensive. Once separated, the particles can be viewed under an inexpensive field microscope for evaluation.
1. Mix a measured amount of oil with kerosene (or other suitable solvent) about 50/50 in a flat- bottomed flask or beaker. Be sure the kerosene is dispensed through a filtered dispensing bottle.
2. Hold a disc magnet tightly to the flask bottom and slosh around the mixture for three minutes.
3. Without removing the magnet, decant the liquid and non-magnetic debris out of the flask through a membrane (patch) using a common vacuum apparatus. This leaves the magnetic particles behind.
4. Remove the magnet and add about 50 ml of filtered
kerosene or solvent and slosh around a little more.
5. Next, transfer the magnetic particles to another patch.
6. View the patches using the top-light microscope. The first patch will be primarily dirt, polymers, rust, oxides, sludge, and non-ferrous wear metals (e.g., copper, babbitt, aluminum, etc.). The second patch will show particles generated from critical surfaces such as shafts, bearings, and gearing.
7. Refer to a wear particle atlas as required to interpret your findings.
This technique is very flexible and provides on-the-spot information. It can be used to verify high particle count, abnormal vibration readings, rising temperatures, or even a suspected failed filter. Visual conformation like this increases your confidence in making decisions and recommendations.
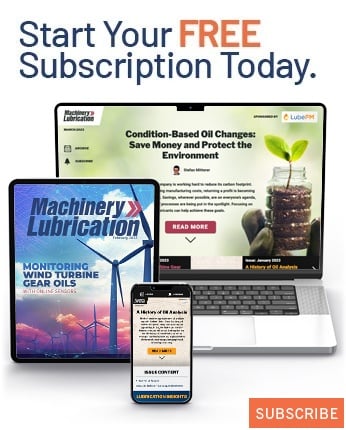