Our plant added lubrication to its reliability enhancement program last year. I was assigned the responsibility to develop the comprehensive lubrication program and determine a time frame for implementation.
Several meetings were held with superintendents, supervisors and top operators from each operational area (rotating equipment specialists, vibration technicians, machinists, electricians and others) to get input on what needed to be accomplished. One phase of the program that we developed was relubrication PMs on electric motor bearings performed by operations personnel. Some of the questions which came from these meetings are answered below.
How Much Grease is Needed?
We implemented the use of the SKF grease meter, which measures the amount of grease pumped from the grease gun into the equipment bearing. We purchased these through our local bearing supplier which handles SKF bearings. We learned that it was important to make sure the guns have a small air release valve on the end.
How Often Should this PM Activity be Performed?
SKF supplied us with a chart and formula for relubrication amounts. Time intervals based upon bearing size, equipment speed and load severities (from the National Electrical Manufacturers Association (NEMA) electric motor standards) were referenced to develop our relubrication schedules.
When Do We Know if the Grease Has Properly Reached the Rolling Elements of the Bearing?
A shock pulse meter supplied by SPM Corp. was acquired to let us know if the grease was reaching the bearings. This small instrument has an accelerometer attached to the meter by a cable. High-frequency vibrations picked up from the bearing are shown in bar scale on the face of the meter. When first connected to the equipment bearing housing, the meter may read from one to nine bars. During relubrication, if the meter is at one bar and starts increasing, the grease gun operator should stop the relubrication process. If the meter is at eight bars, the reading will decrease as the fresh grease reaches the bearing’s moving elements.
Operations personnel were trained to use both instruments to relubricate the equipment according to guidelines from NEMA electric motor standards and SKF. Both meters and a laminated chart showing relubrication amounts were attached to each grease gun.
What are the Benefits?
In the three years before this lubrication program was implemented, our computerized maintenance management system (Maximo Tracking System) showed a total of 32 motor bearing-related repairs per year. Since implementing the lubrication program, our plant has had only 23 motor bearing-related repairs in 2001 and 17 repairs from January to October 2002. Operations relubricates motors only 40 horsepower and above. Our plant has approximately 1,000 motors in this category.
Our plant achieved a 30-percent decrease in motor bearing repairs in 2001 from the average in 1999 and 2000, and another 25-percent decrease in 2002 from the repairs in 2001.
With these advantages, we continue to look for ways to help improve lubrication and our equipment’s reliability.
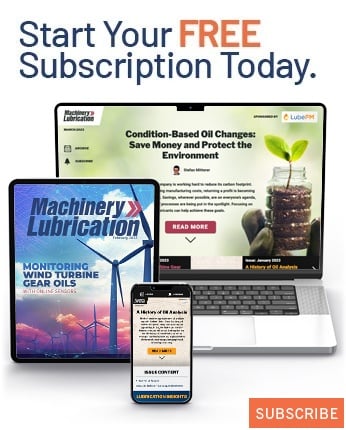