Wear debris analysis is tricky business. Done properly, however, it is perhaps the most effective non-destructive/non-intrusive testing technique available to the reliability professional for determining the nature and root cause of mechanical wear. On one hand, wear debris represents the mirror image of the component from which it was released. Its analysis reveals details about the surface of your machine components without intrusive inspection. On the contrary, the process of wear debris analysis is plagued with problems related to poor sample quality and the inability of the method to localize where the problems exist.
These limitations challenge the maintenance organization's ability to make effective decisions and implement appropriate corrective actions. For instance, suppose an oil analyst advises the maintenance manager of a steel mill that a 35 circuit hydraulic system is generating debris. If the analyst can't localize where the debris is being generated, the maintenance manager is likely to run the machine to failure, then repair the damage, just as he would without knowledge that wear is being generated. In that instance, condition monitoring has failed to deliver value to the organization. However, had the analyst localized the component or circuit under stress, corrective action could be scheduled with precision avoiding the consequences associated with a surprise failure.
The Secret is in the Sample
There are a number of reasons why it is difficult to precisely nail down which component is generating debris, but it primarily comes down to the sample. Wear debris, unlike homogenous properties such as viscosity, TAN, etc., is a transient and very fragile fluid property. For instance, here are some of the ways a sample can be disturbed:
Particle settling - Particles left in a reservoir tend to settle to the bottom of the sump or reservoir. There, they get "lost in the sauce" as they combine with sludge, oxides, last-year's failure, etc.
Particle aging - Just because a wear particle finds its way into your sample bottle doesn't mean the particle was recently produced and represents the current condition of the machine.
Particle filtration - Filters are great for extending machine life through proactive control of contamination, sampling after the filter is analogous to wearing rose colored glasses, unless, of course, an assessment of the filter's performance is desired.
Particle Dilution - In multi-component systems, one component, say a bearing, produces wear debris after which it is swept away by the oil. However, the oil returning from the bad-acting bearing is combined with the return fluid from other components and ultimately deposited in the reservoir, often thousands of gallons in size where the precious few wear particles are diluted creating a needle in a haystack type searching proposition. In the reservoir, the dilution problem is compounded by particle settling, as previously described.
Sampling Problems. Sampling issues ranging from dirty bottles, inappropriate sampling valves, inadequate flushing, etc. can undermine efforts to ascertain machine condition with oil analysis.
Sample Preparation. Failure to adequately shake samples (with a paint shaker) results in poor oil analysis performance.
How do we address these issues? First, we have to get our house in order with respect to sampling procedures. If you don't have clearly defined (preferably written) sampling procedures for each machine and sampling location, get them. Likewise, be sure samples are adequately agitated before testing. Hand shaking samples is both tedious and ineffective. Then test quickly, before particles get a chance to settle out of the fluid.
Beyond sampling and sample preparation, we need to design our sampling system with machine condition monitoring in mind. In the past, when only oil analysis was used to schedule oil changes, sampling location was not quite so important. Modern oil analysis programs, however, focus also on evaluating the machine's condition. Here are some tips:
• Locate your primary sampling location on the return line, before filtration. This enables you to maximize the density of the information desired (machine component information), while minimizing disturbance of the data due to filtration, settling and dilution. Locate your primary sampling port at the common return for all components in the chain. This will serve as your routine sampling location.
• Locate secondary sampling points at various locations in the system as shown in the figure. These ports will be primarily used "on-exception" when the primary location reveals a problem. These secondary ports serve as diagnostic sampling locations.
As a matter of routine, draw samples from the primary sampling location. This location will identify any dirt coming in with new oil, ingesting through faulty seals or breathers and confirms the filter's ability to maintain a material balance between ingressed (ingested and generated) particles and removed (e.g., filtration) particles to within the target cleanliness level. This location will also enable you to assess homogenous properties of the oil. Most importantly, it gives you he earliest and clearest view of abnormal wear that is being generated by the working components. When an alarm is encountered, employ the following diagnostic sequence:
1. Confirm the integrity of the sample. This should always be your first step in addressing non-conformance with oil analysis.
2. Test the oil on the pressure side ahead of the working components. This step quickly tells you if the problem is on the money side of the machine (business end) or on the support side of the machine (reservoir, breather, filters, etc.). Often, the problem will be self-evident at this juncture.
3. If the problem is on the support side of the machine, inspect breathers, new oil cleanness, filters, the reservoir, etc. Secondary sampling ports will enable you to determine filtration efficiency and produce a "field beta" filtration ratio.
4. If the problem is on the money side of the machine, employ secondary sampling to look at each component independently. If all components are generating a high level of wear, your problem is likely lubricant related (wrong, degraded, depleted additives, water contamination, etc.) or load/alignment related. If the problem is localized to a single component, you have the problem pinpoint. Further, analysis and diagnostic efforts can be effectively directed towards the bad actor. Required maintenance tasks can be scheduled with precision and confidence.
5. Note, there are cases where the secondary sampling ports can become primary, routine monitoring ports. If a particular component has a history of poor reliability, or if the machine is super-critical, it might make sense to monitor each component individually.
While not suitable for every machine, this approach is excellent for those critical machines upon which the plant depends so heavily to keep profits flowing. It balances diagnostic rigor and economics by streamlining the employment of secondary sampling ports, using them on-condition only. Try this approach and you will soon be making high confidence, on-target decisions and recommendations from your oil analysis data.
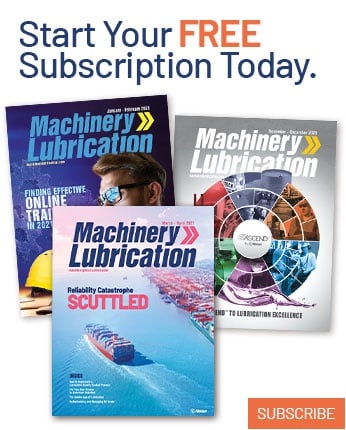