Stress wave analysis (SWAN) provides real-time measurement of friction and mechanical shock in operating machinery. This high-frequency acoustic sensing technology filters out background levels of vibration and audible noise, and provides a graphic representation of machine health.
By measuring shock and friction events, the stress wave analysis technique can detect wear and damage at the earliest stages, prior to increased vibration, and can track the progression of a defect throughout the failure process. This is possible because, as the damage progresses, the energy content of friction and shock events increases.
This “stress wave energy” is then measured and tracked against normal machine operating conditions. Several types of aircraft and industrial gas turbine engines were tested to demonstrate stress wave analysis’s ability to accurately detect a broad range of discrepant conditions and characterize the severity of damage.
What is Stress Wave Analysis?
Stress wave analysis is a state-of-the-art instrumentation technique for measuring friction, shock and dynamic load transfer between moving parts in rotating machinery. These events produce structure-related ultrasound waves (stress waves) that are detected and analyzed electronically by the stress wave analysis system.
An externally mounted sensor on the machine’s housing detects stress waves transmitted through the machine’s structure. A piezoelectric crystal in the sensor converts the stress wave amplitude into an electrical signal, which is then amplified and filtered to remove unwanted low-frequency sound and vibration energy (Figure 1).
The output of the signal conditioner is a stress wave pulse train (SWPT) that represents a time history of individual shock and friction events in the machine, such as those influenced by lubrication. A digital processor then analyzes the stress wave pulse train to determine the peak level and the total energy content generated by the friction or shock event. The computed stress wave peak amplitude (SWPA) and stress wave energy (SWE) values are displayed and stored in a database for comparison and historical trending with normal readings. Stress wave analysis measures even minor shock and friction events that occur between contact surfaces. The level and pattern of anomalous shock events become a diagnostic tool.
The digital analysis of stress waves consists of computing both the amplitude and the energy content of detected stress waves. The amplitude (or peak level) of a stress wave is a function of a single friction or shock event’s intensity. The stress wave energy is a computed value (the time domain integral) that considers the amplitude, shape, duration and rates of all friction and shock events that occur during a reference time interval. In a spalled bearing, for example, the peak level of the detected stress waves is primarily a function of the spall depth, whereas the stress wave energy is a function of spall size (Figure 2).
Figure 2. Stress Wave Energy (SWE)
Because stress wave analysis can detect stress waves at a lower energy than other diagnostic tools, it can usually diagnose problems early. In most cases, during early component fatigue, the energy released between the contact surfaces is too small to excite gearbox or engine structures to levels significantly above background vibration levels. Fatigue is observed only when catastrophic failure or extensive secondary damage occurs. However, with stress wave analysis, stress wave energy can be detected and analyzed early in the failure process (Figure 3).
Figure 3. SWE Operating History
As machine parts come in contact with the defect, even at the earliest stages, shock and friction events generate stress wave energy. Stress wave analysis detects and measures this energy at damage levels well below the degradation required to excite vibration sensors, and before sufficient damage has occurred to activate metal chip detectors in lubrication systems.
Case Histories
Case History No. 1: Roller Bearing Roller End Wear
The benefits of stress wave analysis technology vs. vibration analysis were clearly demonstrated during the monitoring of an industrial gas turbine in a power generation application. Stress wave analysis indicated that there was damage from either the No. 1 or No. 2 roller bearing. A spectral analysis from the sensor in that location showed the spectrum to be riddled with 105.8 hertz (Hz) and harmonic spectral lines.
According to the bearing defect frequency tables, the cage rotational frequency relative to the stationary outer race of the No. 1 and No. 2 bearings was 105.8 Hz. Thus, it was apparent that a bearing defect was present, and that the probable root cause was roller end wear. Spectral content was strongest from sensors close to the No. 1 and No. 2 bearings, and subsided the farther away the sensors were positioned - further evidence that there was bearing damage.
This turbine was also equipped with oil debris and vibration monitoring equipment. Niether of these conventional monitoring systems indicated there was a problem. This is typical of early levels of damage that do not release enough kinetic energy to excite the structural dynamics of the machine’s stiff spring-mass system, or generate enough debris to be captured by chip detectors.
However, because Stress wave analysis filters out background noise and vibration, the signal-to-noise ratio is high enough to detect problems while they are small, so the machine can be safely operated until a repair can be efficiently scheduled. In this case, a disassembly inspection was scheduled to coincide with previously planned downtime.
Figure 4
The teardown and inspection did in fact confirm damage on the No. 2 bearing, just as predicted several months earlier by the first SWAN indication. The photo in Figure 5 clearly shows roller end wear, as suggested in the initial diagnosis. In addition, abrasive wear on the race shoulder was reported.
Figure 5. No. 2 Bearing Showing
Roller End Wear
Case History No. 2: Labyrinth Seal Wear
Data was collected from a large industrial gas turbine at an electric power utility for five months before it was removed from service for a scheduled overhaul. During this period, there was no indication of a problem with any of the gears and bearings, but a sensor located on the low-pressure turbine (LPT) did show a significant increase in friction levels (Figure 6).
Figure 6. Labyrinth Seal Wear
The erratic nature of the stress wave energy readings and the absence of any clear indication of damage to gears or bearings, plus the fact that lube changes had no impact on the stress wave energy, led maintenance and engineering staff to the conclusion that some sort of rubbing (or similar constant wear mechanism) was at fault. A thorough disassembly inspection conducted during overhaul revealed the cause to be excessive wear to the faces of the labyrinth seals in the LPT area.
Case History No. 3: Seeded Fault Engine Test (SFET)
A series of discrepant conditions was intentionally built into a Pratt & Whitney F100-PW-100 engine, which was then operated over a range of operating conditions to test the detection capability of various diagnostic techniques. (Author’s note: This test was sponsored by the Joint Strike Fighter program.)
-
Bearing Race Damage - When two shallow grooves were cut across the full width of the No. 1 bearing race surface, SWAN clearly indicated the discrepant condition. The SWPT spectral lines indicative of repetitive friction and impact shock events were present only in the discrepant bearing; had large amplitudes (15-20 db); and occurred at predictable roller passage frequencies and harmonics that were easily calculated from bearing geometry and speed (Figure 7).
The total stress wave energy (friction and shock energy) in the discrepant bearing was about 14 times greater than that of the baseline example. This large change in stress wave energyE, when significant physical damage is present in bearings, is a key requirement in achieving high diagnostic accuracy (high probability of early fault detection and low probability of false alarm for a predetermined alarm threshold). The appearance of spectral lines at predictable frequencies for a given fault condition, and the absence of significant spectral lines in the stress wave spectrum of a healthy machine are essential for accurate fault isolation, after a discrepant condition is indicated by an order of magnitude increase in stress wave energy. -
Oil Degradation - Oil degradation was evident as a severe distortion of the stress wave amplitude distribution histogram, and a modest increase in the overall friction (stress wave energy). All the data in Figures 8 through 10 are from sensor location 2, which is closest to the No. 2 and No. 3 bearing pair. The No. 3 ball bearing is the most heavily loaded bearing in the engine, and is therefore the most sensitive to oil degradation.
The histogram in Figure 8 was acquired on September 30, before any oil degradation testing began. It shows a statistically normal, bell-shaped distribution of friction events that is typical of properly lubricated bearings. Oil degradation testing began on October 3, by closing the oil cooler bypass valve in stages that gradually raised the temperature of scavenged oil to 350°F. The histogram shown in Figure 9 was taken during this testing.
The SWE increased only by about 37 percent, but the amplitude distribution shifted dramatically. At this point in the testing, the majority of the friction events had a peak amplitude of more than 5 volts. (The tape recorder used in this test saturated at 5 volts, so all friction events with a peak amplitude of 5 volts or more are counted in the 5-volt bin, causing the high count at exactly 5 volts in the histogram.) Oil degradation testing continued on October 5, 7 and 8 with oil temperatures reaching 350°F on October 5 and 450°F on October 7 and 8.
During this time, there was no significant change to the histogram or the stress wave energy. At the conclusion of testing on October 8, the oil was drained and replaced. The histogram in Figure 10 was taken on October 13 when testing with fresh oil resumed. It shows a return to the normal distribution that is representative of healthy lubrication. The stress wave energy remained slightly elevated, and might have represented some minor wear, due to the hours of operation with degraded oil. -
Foreign Object Damage (FOD) - Stress wave analysis demonstrated the capability to detect “hard” FOD, without being oversensitive to “soft” FOD, as well as the ability to indicate how deep into the engine the hard FOD occurred. This level of detection and discrimination is necessary to support the objective of reducing the maintenance burden associated with boroscope inspections.
The data shows that it is possible to build a stress wave analysis-based FOD detector that will indicate when a hard FOD event has occurred, and how deep into the engine the resulting boroscope inspection needs to be performed. Figure 11 shows the time domain SWPT signal, which illustrates the difference between several different examples of hard and soft FOD.
Figure 7. Bearing Race Damage
Figure 8. September 30 (Good Oil), SWE = 16153
Figure 9. October 3 (Degraded Oil), SWE = 22175
Figure 10. October 13 (Good Oil), SWE = 21941
These case histories document the ability of the Stress Wave Analysis technique to:
- detect a wide variety of gas turbine discrepant conditions with a high degree of accuracy,
- isolate the root cause of detected faults,
- quantify the extent of damage for trending and projection of remaining useful life.
Stress wave analysis is a new diagnostic and prognostic tool for the engine maintainer’s toolbox. It is superior to vibration analysis for detecting and quantifying discrepant conditions that generate friction and shock. This includes not only localized fatigue damage to bearings and gears, but also includes lubrication problems, abrasive wear, abnormal dynamic loading and foreign object damage. The basic analysis tools in stress wave analysis provide accurate detection, quantification and fault isolation through an easy-to-use graphical user interface.
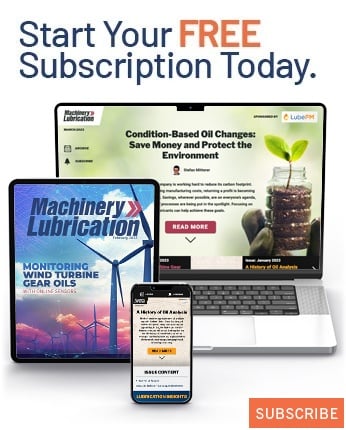