A large municipal bus fleet engineering manager was perplexed. With six different bus depots, each operating buses with engines of the same model and age under similar service conditions, using the same oil and fuel supplier, why was only one of the depots routinely showing elevated soot levels from more than 90 percent of the engine oil samples?
After some deep thought, he had a list of more than 10 items, some likely, some not so likely, to explain this strange phenomenon. Could this one depot have received a delivery of bulk oil that had not been properly formulated? How about the fuel? Had a batch of bad fuel been delivered? Maybe it was the air intake system. Was this one depot doing anything different from the other depots?
Armed with his “hit-list,” the engineering manager set off to the depot in question to discuss his theories with the maintenance supervisor. Walking through the maintenance shop, he witnessed one of the lube technicians just about to complete a routine oil change and at the same time, take an oil sample. The manager decided to stop and observe how the samples were being taken.
The bus was driven into the shop and the engine covers removed; however, what happened next was almost too much for the manager to comprehend. The lube tech, sensitive to the need to take the sample with the oil still hot, took a large screwdriver and proceeded to puncture the full-flow oil filter. The sample bottle was filled from the stream of oil emanating from the filter. The bottle was then capped and ready for shipment to the lab.
When questioned, the lube tech explained that the oil filters must be drained of oil ready for disposal, and that this method allowed him to save time. He could accomplish two tasks simultaneously - taking an oil sample and draining the filter!
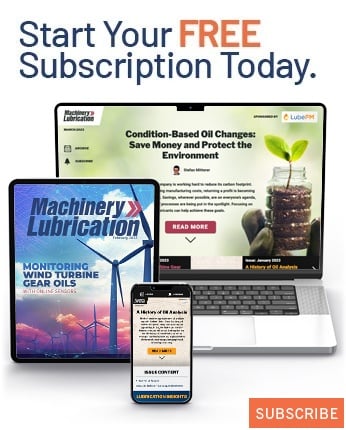