Today’s business climate makes it important for customers to get the most from their bearings; namely long bearing service life and low noise performance. These requirements mean that techniques are needed to help ensure that the necessary lubricant cleanliness levels and conditions are being met.
To fulfill these needs, a new product, the SKF BeQuiet+ tester, has been developed. It assesses the quality of the lubricant with regard to cleanliness and damping characteristics. Lubricant manufacturers use the test rig as a tool for their lubricant development as well as for production control.
The BeQuiet+ is also recommended to bearing producers as a means of selecting the best lubricant on the market and for incoming batch control, and to end-users as a way to verify the lubrication quality in service.
Clean Greases are Important
The use of clean lubricants for rolling bearings is essential for a long bearing life. In the case of grease lubrication, many factors can affect the degree of cleanliness during operation, but a clean grease for the initial lubrication as well as for relubrication will always be required.
Also, in applications where the bearing fatigue life is not at stake (because of low loads), the need for clean greases can still be extremely important. For example, clean grease is needed to help ensure low bearing noise, which is required for many electric motor applications.
Because field fan bearings are expected to run extremely quiet, it is clear that the electric motor manufacturers require bearings with the lowest possible vibration level and no disturbing noise. This application calls for extreme cleanliness and low noise grease.
Bearings in automotive gearboxes are expected to run as long as the car lasts. Such bearings are exposed to foreign matter in the gear oil, often originating from the gears, which adversely affects the bearings. The particles being over-rolled damage the raceways producing “dents” and raising the stress level at their edges. This promotes an aging process leading to surface distress (noise increase) and finally to bearing fatigue failure.
Noise Generation in Bearings
Particle Over-Rolling
Because the film that separates the mating surfaces in the rolling contact is thin (usually less than 1 micron) it is clear that any particles larger than the film thickness can disturb smooth operation.
Figure 1. Noise Recording on a “Dirty” Lubricant
Figure 1 shows a recording of the vibration peaks of an unclean lubricant. The vibration peaks are recorded by filtering the short duration effect of the particles’ over-rolling from the total signal. The over-rolling of larger particles can lead to permanent raceway dents (Figure 2).
Figure 2. Over-rolling of Large Particles
The over-rolling of brittle particles can damage the bearing surface (Figure 3). If this occurs, then the overall signal will increase in time, indicating that the original high bearing quality is actually lost because a lubricant with insufficient cleanliness was used.
Figure 3. Over-rolling of Brittle Smaller Particles
Experience has made it clear that particle over-rolling can be split into four distinct quality classes: dirty, noisy, clean and quiet. This classification can be defined as follows:
-
Dirty. The hardness and size of particles is such that over-rolling leads to permanent damage, resulting in increased overall noise and reduced bearing fatigue life.
-
Noisy. The hardness and size of over-rolled particles may damage the bearing surfaces, which results in a noticeable increase in overall bearing noise but not to the degree that the bearing fatigue life is adversely affected.
-
Clean. The hardness and size of over-rolled particles will produce noticeable vibration peaks, but there is no permanent damage to the bearing surfaces.
-
Quiet. The highest degree of cleanliness due to only a few particles causing vibration peaks.
Lubricants classified as “dirty” are rare in the delivery condition; however, depending on the application, this condition may develop during operation. There are a few greases on the market that, due to their thickener type or solid additives, fall into the “noisy” classification. Typical examples are some calcium-complex greases that contain large particles of calcium salts, which produce small permanent dents (Figure 1).
The majority of today’s greases are classified as “clean.” Typical examples are polyurea greases where large agglomerates of the thickener can be present. These greases can produce large vibration peaks, but because the hardness of these particles is low, the over-rolling will not cause noticeable dents (Figure 4).
Figure 4. Noise Recording on a “Clean” Grease
Only a few greases can be classified as “quiet.” Typical examples are lithium soap greases, which are produced in a clean environment and by a process that filters out undue particles and produces a fine soap structure. In each classification, different levels can have further distinguishing quality grades.
Influence of the Lubricating Grease
A comparison of the damping characteristics of different lubricants should be made on the same bearing mounted in an identical manner. When these precautions are taken, the lubricant with optimum damping characteristics can be successfully selected. Many factors within the lubricant contribute to the damping characteristics.
As Figure 5 illustrates, the important factors for oil are the viscosity, the base oil type and the applied additive types. A clear trend of increasing damping at increasing oil viscosity can often be found (Figure 5).
Figure 5. Effect of Oil Viscosity on Damping Characteristics
For greases, the damping characteristics can be quite erratic, probably because the type of thickener and its microstructure will also affect these characteristics. Moreover, additives that influence wettability and possess a strong surface attack can become dominant.
The BeQuiet+ Grease Noise Tester
The importance of this damping effect was one of the main reasons SKF upgraded its earlier version of the BeQuiet instrument. The new instrument, the BeQuiet+ (Photo on page 30), enables lubricant manufacturers to develop lubricants with the highest damping characteristics. For the bearing producers, this new tool is equally important for selecting grease with highest damping characteristics.
In addition, the BeQuiet+ tester can classify the grease into one of the four classifications discussed earlier. One of its most important capabilities is its ability to develop, improve or identify quiet greases.
The BeQuiet equipment incorporates a unique test procedure and includes an unusual degree of automation. Its fully automatic procedure consists of repetitively dosing the lubricant to the test bearing and recording the vibration level and peaks. The whole sequence, illustrated in Figure 6, is PC-controlled through dedicated software.
Figure 6. Sequence of BeQuiet + Testing
This procedure disregards the fact that ingress of dirt particles from the environment can disturb the measurement results, thus making it possible to use the same bearing for different tests without dismounting. This can be advantageous for determining the damaging characteristics of dirty lubricants by following a sequence for testing reference lubricant, test lubricant and finally the reference lubricant again.
Similar advantages are found when comparing lubricants’ damping characteristics. A logical advantage of the BeQuiet+ test procedure is that it reduces operating costs; in bearing consumption as well as operator time.
Machine Description
The semiautomatic BeQuiet+ tester was developed for laboratory use. A cabinet incorporates the PC, the loudspeaker, the keyboard and the screen, and includes some room for tools, the calibration unit and a printer. A second cabinet incorporates the electrical installations, the pneumatics and the actual measuring unit. All important parts of the machine can be accessed from the front.
The BeQuiet+ has the following main components:
-
A high-quality spindle rotating at 1,800 rpm
-
A special adapter to hold the test bearing, which features the grease inlet and outlet and an inlet for compressed air
-
A test bearing, which is a 608/QE4 type ball bearing
-
A pneumatic loading device for the test bearing with 30N
-
A grease dosage unit comprised of a linear actuator driven by a speed-controlled servo-motor which acts on a disposable syringe that contains the grease sample
-
The QTC MEB 95 electronics with the SKF Peak Detection Algorithm to identify the vibration peaks and damping factors
-
A special interface and program to carry out the measurements in a fully automatic way, as well as to store the observed peak data and evaluate the results
-
A printer/plotter
-
A network LAN
Functional Description
The rig is able to measure the specific disturbances caused by the over-rolling of particles, called vibration peaks. The key component of the rig is the proprietary SKF Peak Detection Algorithm, which enables these vibration peaks to be singled out from the total bearing vibration signal.
The number of peaks and their intensity are used to assess the quiet running behavior in a quantitative way. The user is then able to compare the result with a definable target.
In a further step, the grease damping characteristic is also measured. The idea is to relate the bearing noise of the greased bearing in certain frequency bands to the bearing noise in reference conditions (slightly oiled).
Reliability and Fast Analysis
Efforts have been made to achieve a high degree of automation and to minimize the risks of other contaminants adversely affecting the result. The key to the BeQuiet+ is the use of controlled grease dosages and peak measurements on a single test bearing of special low noise quality.
The entire process is controlled by dedicated software on a personal computer, which also stores all peak data and vibration levels and subsequently evaluates the results producing either tabular reports or line charts.
The BeQuiet+ equipment allows different measurement modes. In addition to the peak measurements, the grease damping characteristic is also identified. The bearing noise obtained in reference condition is related to the bearing noise in grease condition.
Grease Quality Classes
The outcome of the peak measurements of a greased 608/QE4 bearing are shown in microns per second (µm/s) and given in:
- Percent of the peaks = 5 µm/s (5 µm/s was the limit of the previous BQ1 class)
- Percent of the peaks = 10 µm/s (10 µm/s was the limit of the previous BQ2 class)
- Percent of the peaks = 20 µm/s (20 µm/s was the limit of the previous BQ3 class)
- Percent of the peaks = 40 µm/s (40 µm/s was the limit of the previous BQ4 class)
The classification of grease noise is then set in GN classes in the following way:
- GN0: > anything worse than GN1
- GN1: > 95 percent of all peaks are = 40 µm/s
- GN2: > 95 percent of all peaks are = 20 µm/s
-
GN3: > 95 percent of all peaks are = 10 µm/s
> 98 percent of all peaks are = 20 µm/s
100 percent of all peaks are = 40 µm/s -
GN4: > 95 percent of all peaks are = 5 µm/s
> 98 percent of all peaks are =10 µm/s
100 percent of all peaks are = 20 µm/s
In particular, the following assessments can be made with the test rig:
- Determination of the quiet running classification of lubricants in terms of particle over-rolling
- Determination of any permanent bearing damage due to particle over-rolling
- Determination of the lubricant’s damping characteristics
- Comparison of lubricants with regard to their damping characteristics
A logical advantage of the BeQuiet+ test procedure is that the operating cost is reduced to a minimum, both in terms of bearing consumption as well as operator time.
BeQuiet+ is Put to Practical Use
The Krytox Technical support lab, which is part of the Krytox Performance Lubricants business unit of the Dupont Chemical Solutions Enterprise business, provides technical assistance to Krytox customers, supports the production unit and develops new products for its customers. The lab uses the SKF BeQuiet+ tester to monitor the noise in its test grease.
The test grease noise levels are compared with the noise levels of the standard grease. In addition, the number of peaks detected in the test grease along with their intensity is used to provide quantitative noise levels. A grease damping measurement, which relates the greased bearing noise to certain frequency bands of a dry bearing, can also be performed when necessary. The test rig automatically adds and removes the test grease to allow multiple (100) measurements of noise in a precision 608 size bearing.
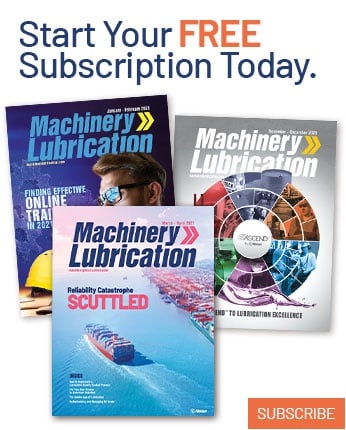