Santos is a major Australian energy company with assets of more than $5 billion and annual production of 57.3 million barrels of oil equivalent. The company’s business is oil and gas exploration and production, with interests in every major Australian petroleum province.
Santos is the largest producer of gas for the Australian market, supplying gas to all mainland Australian states and territories as well as selling oil and liquids to a number of domestic and international customers.
The core of Santos’ business is a majority working interest in the Cooper/Eromanga Basins oil and gas fields in central Australia. Santos produces gas, ethane, oil and gas liquids from the Basins, and is involved in production and exploration operations.
Case Study
The motivation to develop the greasing program cascaded from a strategy to optimize maintenance operating costs. In the past, the majority of greasing was completed on an ad hoc basis relating to vibration and/or noise. The equipment involved in the program included large and small electric motors, after-cooler fans and engine cooling fans - approximately 240 pieces of equipment.
With the targeted gas plant being only 10 years old, a formal preventive maintenance program for lubrication was crucial to enhance the life cycle of equipment. Several problems were recognized once the project was initiated. These included the following:
- low procurement of grease versus quantity of equipment
- no ownership of the greasing tasks
- many different types of grease used within the plant
- limited greasing equipment
- no formal training of personnel
These issues were solved through the following five-step approach:
1. Product requirement assessment. The operation worked with its lubricant supplier to complete an equipment audit of the gas plant. This involved identifying all the equipment to be included in the program and researching all of the particulars.
2. Detailed requirements development. The operation worked together with the lubricant supplier and original equipment manufacturers (OEMs) to determine the types of greases and calculate a suitable amount and frequency for each piece of equipment.
This task brought the inventory of grease types to just two, which resulted in a large cost savings due to bulk purchases, decreased contamination and fewer errors involving the application of the incorrect grease.
This task required considerable time, but formed the most crucial step by defining the foundation for the program. If any part of this difficult task had been flawed, all the effort thereafter would have been wasted and more failures inevitable.
3. Creation of “job plans.” The information in each job plan included:
-
equipment description and tag number
-
amount of grease
-
frequency
-
type of grease
-
part of the equipment being greased (such as DE bearing, fan bearing, etc.)
-
type of greasing equipment to be used. This is useful for climbing ladders because the selection of the wrong grease gun can waste time.
-
number of points to be greased
-
detailed procedures
Equipment
|
Lubricated Component
|
Grease Product
|
Amount
|
Desired Greasing Equipment
|
Export Compressor G
C-1000-50G |
Motor DE Bearing
|
Alvania RL3
|
180 grams
|
Automatic Grease Pump
|
Export Compressor G
C-1000-50G |
Motor NDE Bearing
|
Alvania RL3
|
60 grams
|
Automatic Grease Pump
|
Export Compressor H
C-1000-50H |
Motor DE Bearing
|
Alvania RL3
|
150 grams
|
Automatic Grease Pump
|
Export Compressor H
C-1000-50H |
Motor NDE Bearing
|
Alvania RL3
|
40 grams
|
Automatic Grease Pump
|
Table 1. Ballera Compressor Motors Monthly
Greasing Schedule; Export Compressor G and H
Equipment
|
Lubricated Component
|
Grease Product
|
# of Points
|
Amount
|
Desired Greasing Equipment
|
CO2 Train
Pump A P-1200-1A |
Motor DE and NDE
|
Alvania RL3
|
2
|
10 grams
|
Lever gun with hard extension
|
CO2 Train
Pump B P-1200-1B |
Motor DE and NDE
|
Alvania RL3
|
2
|
10 grams
|
Lever gun with hard extension
|
Cooler Fan
5800-K-001 |
Fan
|
Alvania EP(LF)2
|
12
|
5 grams
|
Lever gun with flexible hose
|
Table 2. CO2 Pumps and Nodal Engine
Cooling Fan Monthly Greasing Schedule
This information was recorded (Tables 1 and 2) and then attached to Maximo (asset management system). Too much information on the PM was viewed as detrimental, as the maintainer often would not read it in entirety and an important point could be missed.
It was also essential to set out the order of equipment to be greased with the best physical route in the plant. With the program being quite time consuming, the most direct route would help the end user become more time-efficient and therefore cost-effective. An attached map of the plant with the highlighted route helps new and existing personnel learn the location of each piece of equipment within the facility.
4. Obtain the right tools. Developing the program required new greasing equipment. The operation purchased manual grease guns in two colors - one for each type of grease - with flexible and hard hose extensions. Sometimes the grease fitting is not able to be reached with a hard extension piece, so a flexible extension is useful.
Each gun was fitted with an SKF grease meter and a pressure gauge to measure the exact amount of grease, and identify any line blockages (Figure 1).
Figure 1. Manual Grease Gun with Grease
Meter and Pressure Gauge
Other equipment included a ladder, nipple kit, tool box, customized grease gun carry bag (for climbing ladders), air compressor, hose reels with grease pump and digital grease guns.
There are numerous large high-voltage drives (3,500 kilowatts), which can require up to 200 grams of grease per month in each bearing. To simplify the greasing process, an air-powered digital grease gun (measures the amount of grease) was selected. It was important to contain the grease pump and grease drum in its own compartment, so contamination in a dusty environment is not possible (Figure 2).
Figure 2. Grease Drum and Pump Compartment
High-strength industrial rubber seals were used to reduce dust intake. A specialized trailer/skid (Figure 3) was produced in collaboration with Cooper-Standard Automotive Australia Tecalemit.
Figure 3. Greasing Trailer/Skid
The trailer was designed so that the top skid could be unclipped, lifted off the frame and placed on the back of a four-wheel drive utility car for field-greasing applications. Therefore, weight and size restrictions were important aspects that hindered a basic design solution.
The final design allowed versatility through various weight and space and optimization methods. Utilizing every space through most select placement and calculating weight at the design stage was time-intensive, but became imperative for a practical final product.
The final design weighed 700 kg (comprising all equipment) and the nominal size was 1,500 mm x 1,000 mm x 1,000 mm. Some features include a roof rack for extra storage, hinged doors with industrial seals, gas struts for rear service door, skid with forklift access, silent block mounts for compressor vibration dampening, fuel fill point on top of skid and support legs.
The skid/trailer and equipment was also clearly marked with the specific grease types and safety tips such as “release pressure when changing grease drums” and “open side door when starting compressor.” This was an important step for equipment longevity and personnel safety.
5. Training. The final step of the implementation process involved training (practical and theoretical) for personnel (utility staff) responsible for maintaining the program. It was important to use company staff to promote a sense of ownership and responsibility over the program. The training was provided by the lubricant supplier in cooperation with the equipment supplier.
All theoretical grease topics were covered with special attention to safety and troubleshooting. The job plans were validated during the training stage, and as the staff members were trained in the gas plant, the actual job plans were used and updated accordingly.
Training included a requirement to walk the plant, as this technique identified safety concerns due to exposed rotating shafts, faulty connections, incorrect grease application, noisy and/or high-vibration equipment and errors within the job plans. The trainees integrated theory and practical knowledge and noted:
-
some faulty connections to the cooling fan of a gas engine, which saved an inevitable failure
-
missing safety barriers around high-speed shafts, which could cause serious injury
-
high noise and vibration issues on some critical electric motors, which became inherently important when analyzed further
-
identification of a high-pressure reading on the gauge, which ended up being a blockage problem
-
incompatible grease applied to a bearing requiring flushing of the extension lines
These were key last steps in the conclusion of the implementation stage, which in turn created an error-free program that allowed a smoother handover transition for site staff.
Implementation
It took approximately six months and a considerable amount of money to fully develop and implement the whole program. This included the time and costs of other projects identified throughout the implementation stage, which ended up being quite substantial.
While it seemed like a large financial and time cost, the benefits were viewed as being more than compensatory by ensuring a cost-effective and productive facility for the future. After only a short time into this program, there had been no reactive maintenance involving grease-related failures, which saved operating costs within the maintenance department.
The end users were involved throughout all stages of development, which resulted in strong support for the program. The end users’ ideas were valuable, as they usually brought with them a great deal of experience in the facility. They were also able to assume ownership, which provided the backbone for the program’s success.
Responsibility for the program recently transferred to the site maintenance supervisor. This role includes a number of duties such as updating the program with new equipment, regular inspection of grease equipment, ensuring the completion of all job plans and striving for continuous improvement.
This formal greasing program was a tremendous step toward reducing equipment failures and associated maintenance costs. The program was well-received by all staff (management and interdepartmental site personnel), and has become an integral part of the optimized operation of the Santos gas plant as well as a template for lubrication program development at other company locations.
Procedure
-
Use caution and safety when working around moving equipment and when using a grease gun, especially around the shaft area.
-
Be careful when loading grease into the grease gun to ensure that contaminants are not introduced. If using a cartridge, be careful when removing the metal lid to ensure that no metal slivers are introduced into the grease.
-
Make sure the dispensing nozzle of the grease gun is clean before using. Pump a small amount of grease out of the dispensing nozzle, then wipe off with a clean rag or lint-free cloth before attaching to the grease fitting.
-
Ensure the grease drain (hole at bottom of grease box) is clear and not blocked.
-
Clean dirt from all grease fittings before attaching the grease gun. Inspect and replace damaged fittings. Also clean the grease fitting after applying grease.
-
Ensure the proper grease is used at every grease point. Applying the wrong grease can cause an incompatibility problem which can quickly cause bearing failure.
-
Do not rush the application of grease, as this can lead to oil bleeding in the feed line. Instead, apply using a constant force. Also, if the action is too fast, grease will leak at the labyrinth seals instead of the grease box due to excessive pressure. After every 15 grams is injected, wait 20 seconds before injecting next supply. The newly injected grease pushes the used grease to the slinger ring which expels it in the grease box.
-
If the motor is not running, do not inject any grease. NOTE: Inject only the full specified amount once the motor is running again. Do not close the work order until this has been completed.
-
When finished, remove any excess grease from area.
-
Calibrate grease guns regularly to ensure the proper delivery volume.
-
Store grease guns unpressurized in a clean, cool, dry area and in a horizontal position to help keep the oil from bleeding out of the grease. Cover the coupler to keep it free from dirt and contaminants.
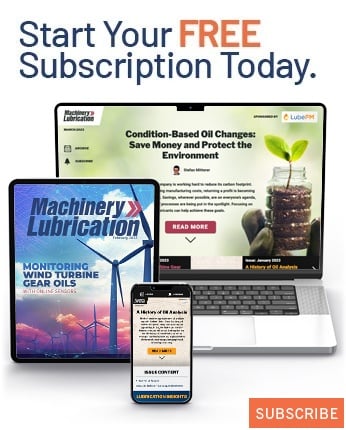