Years ago I was performing on-site oil analysis screening in a steel mill. My job was to collect oil samples from each of the 18 bar mill gearboxes and screen them for ISO particle count, ferrous density, moisture and viscosity.
To reduce the instances of particle settling, I would typically collect three or four samples at one time and proceed to screen them for particle count and moisture before collecting the next batch.
If the particle counts broke the target cleanliness code, I would then test for ferrous density. Otherwise, I would leave the samples to be screened for viscosity after the sample temperature had settled.
This bar mill is typical of most mills seen around the country. The mill is made up of a series of gearboxes, one after another, along the production line. The gearboxes are important in moving the steel through the process as it is transformed from steel bricks into rebar.
The steel empties out of the furnace as red hot slab and gets pressed and formed into long stocks of rebar. Due to the design of this mill, the first few gearboxes suffer more process punishment than the last few.
On one particular day, as usual, I started my sampling process with gearbox No. 1 through No. 4. When I tested the No. 4 gearbox, it exceeded the cleanliness target of ISO 18/16/13.
This was not unusual for this particular gearbox. In recent months, the particle count and the ferrous density for this gearbox had been creeping up. I had recommended ferrography exception testing and inspections on the gearbox each month prior to this. Each month my recommendations were dismissed.
Because the ISO cleanliness target was once again above the target, I then went ahead and performed a ferrous density test on the sample. The result was a staggering 90 percent ferrous particles in the sample.
I immediately located the maintenance manager and told him about the inevitable failure. Confident that action would ensue, I was impressed we had prevented any unscheduled downtime so far.
That weekend I bumped into the mill manager. I mentioned the problem with the No. 4 gearbox and he immediately called the maintenance manager to make sure the problem was going to be taken care of during the weekly scheduled downtime. He was confident that the problem was going to be fixed.
A week later, while on vacation, the mill manager received a phone call from the maintenance manager. Gearbox No. 4 had failed in the middle of the night and the plant suffered 27 hours of unscheduled downtime, which resulted in the loss of thousands of dollars in revenue.
It turns out that the inspection performed on the No. 4 gearbox (opening the inspection hatch and looking in) failed to bring about the proper maintenance activities.
Soon after that, the maintenance manager was dismissed from his duties at the mill and the rest of the plant equipment was added to the oil analysis program.
What is the moral of this story? Understand and appreciate the data on your oil analysis report. Your job may depend on it.
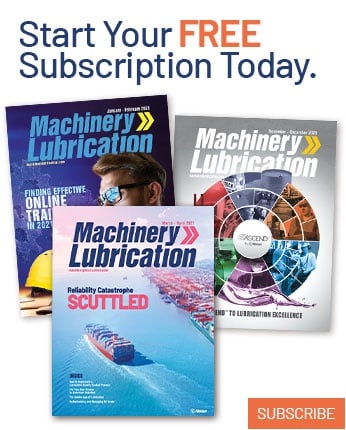