SES Technical, Inc. is contracted by LTV Steel's Cleveland Works to provide predictive maintenance services to all areas around the mill. These areas include each step of the production of flat rolled steel from the blast furnaces to the finishing mills, including such things as power generation and water treatment plants. It goes without saying that it is a very exciting place to be involved with predictive maintenance.
SES Technical takes a "hands on" approach to all disciplines of predictive maintenance. The same Field Engineer who collects the data performs vibration, infrared, and ultrasonic analysis. This allows the engineers to develop an understanding of the equipment and develop a familiarity with its maintenance history. SES has also applied this principal to oil analysis.
A weakness in many oil analysis programs is the poor link between the analyst making the recommendations and the maintenance personnel making the decisions. Oil test data is often analyzed by people with little or no knowledge of the equipment under investigation. This shifts the burden of interpretation to the maintenance personnel, who often have little or no knowledge about oil analysis test data. At LTV Steel, the same SES Field Engineer takes the sample, has it tested locally, analyzes the test data and coordinates with the maintenance manager to determine the best course of action for any exceptions found. This allows the data analysis to be performed by someone familiar with the equipment's history and operating parameters, as well as the test methods and performance. The results of this philosophy have been very positive with many success stories, especially the one described below.
The mill's basic oxygen
furnace (BOF), the focus of the present case study, contains a vessel in which
molten iron is combined with scrap steel followed by an oxygen purge to remove
impurities from the steel in the form of slag. The slag rises to the top of
the vessel where it is poured off and recycled.
![]() |
Vessel
Tilt Bearing on Basic Oxygen Furnace
|
This large vessel, over
20 feet in height, rests on two tilt bearings that enable it to rotate 360 degrees
to pour off the steel after the slag is removed. If one of the bearings fails,
the furnace is not able to function. Given the great size of these bearings,
replacement is time consuming, expensive, and results in substantial downtime.
Predictive maintenance is a must to ensure reliability of this critical unit
These bearings present a unique challenge for predictive maintenance (PdM).
In the majority of cases, with a critical piece of equipment, most, if not all,
of the PdM tools would be used. In this case, however, traditional vibration
analysis has little or no application because of the bearing's slow rotational
speed. The high level of radiant heat emitted from the furnace renders infrared
thermography ineffective for monitoring the bearings. That leaves only oil analysis,
which is also somewhat limited because the bearings are grease lubricated. The
difficulty in obtaining a representative sample, combined with a limited number
of available tests that can be applied to grease analysis, often makes the approach
less attractive. Achieving PdM success, in this case, is especially dependent
upon careful monthly sampling and the performance of spectrochemical and wear
debris analysis.
The following sampling procedure is carefully followed each time to ensure the
consistency:
- The vessel is rotated several times in each direction to thoroughly mix the grease.
- The sample is taken from the bottom (load side) of the bearing.
- Fresh grease is pumped through a fitting on top of the bearing to push the used grease out of a port at the bottom.
- A sufficient amount of grease is pumped through to flush the opening before collecting the sample.
In June of 1998, the monthly sample on one of the tilt bearings showed a sharp increase in iron. The iron level went from 120 ppm to 5218 ppm in four months (Figure 1). The system was re-sampled immediately to confirm the iron level. Upon confirming the out-of-limit condition, diagnostic analysis began.
Iron is typically considered a wear metal, even in a steel mill. Its presence in a bearing lubricant is likely to indicate corrosion and wear to the bearing elements or race. If the analysis were being performed by an outside source, the recommendation would probably have been to inspect the bearing for abnormal corrosion or wear.
In this case, however, the presence of a high iron content was not the result of wear or corrosion. While wear particle analysis did reveal a high level of laminar platelets, an indication of abnormal rolling contact wear, this is considered normal for bearings operating at very slow speeds and under extreme loads. The level of platelets did not corroborate the unusually high levels of iron found to be present in the spectochemical analysis. Also, no elevated levels of other wear elements were found to confirm a wear problem. It was therefore deduced that the high iron level was not a result of bearing wear or corrosion.
![]() |
Outside
view of Basic Oxygen Furnace
|
However, silicon and magnesium were found at high levels as well. These elements are usually found along with iron in slag. Given the configuration of the furnace and the signature from spectrochemical analysis, it was concluded that the most likely source of high iron level was slag contamination.
Examination of the furnace
revealed a warped furnace wall that, during the oxygen purge, exposed the bearing
casing to molten slag splashing from the vessel. The hot slag deteriorated the
bearing seal allowing slag to contaminate the bearing. Had the situation not
been discovered and corrected, the slag would have caused severe abrasion and
eventual failure of the bearing.
To protect the bearing from further contamination, a shield was fabricated
and installed.
An additional cooling fan was also installed to prevent further
warping of the furnace wall. Approximately 50 pounds of fresh grease was pumped
through the bearing to flush out all contamination. Daily oil samples were taken
for the first week to ensure no further contamination occurred. And, the system
was scheduled for a seal change and bearing inspection during a future maintenance
shut down.
This was a shining example of how the proper application of oil analysis can detect incipient problems, allowing sufficient time to deliver solutions before the occurrence of damage. A representative of LTV Steel estimated the savings associated with avoiding an unscheduled bearing change at $1.4 million dollars, proving once again that decisions supported by condition monitoring data put money on the bottom line.
SES Technical has found that by combining oil analysis expertise with machinery and application expertise, PdM efforts are more productive and more profitable. When the oil analyst and maintenance staff work side by side, more effective decisions can be made with the information obtained from lubricant testing.
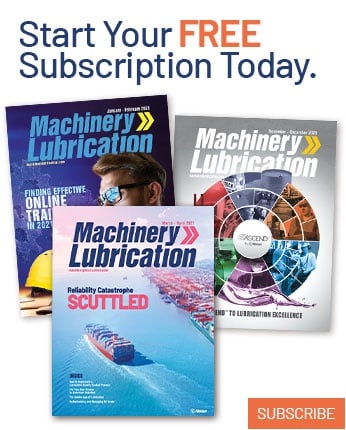