The analysis of power train lubricants for the purpose of detecting faults and abnormal wear patterns is a well developed practice in mobile equipment applications. However, these same techniques don't always transfer successfully into stationary equipment applications for many users.
In recent years new approaches and techniques have been advanced to substantially improve the detection of incipient and developing faults in bearings and gear units using wear debris analysis. The approach is more systemic as opposed to the application of any singular new or emerging technology.
It begins with improvements in the sampling process to enrich the data and proceeds through the use of specific strategies and tactics. After detection is confirmed, the final analytical phase involves wear particle identification using both classic and advanced techniques.
In researching and organizing this work it became apparent that, like so many endeavors, success depends far more on the quality of execution than the strength of the underlying technologies. This is observed from the fact that while a great deal of new knowledge and technology has been advanced, for the vast majority of industrial organizations employing wear debris analysis, very little has changed in either their tools or approach.
So too, it seems that some have found extraordinary success with even the most basic tools and techniques while others, having invested in state-of-the-art instrumentation, have expressed nothing but frustration and disillusionment.
Goal and Strategies of Wear Particle Analysis
One might say that there is a singular goal when it comes to wear debris analysis--to achieve the highest level of machine reliability at the lowest possible cost. However, in order to reach such an overarching goal, several subsidiary objectives must be systematically targeted and achieved.
These objectives will be referred to as "strategies" and, in sum, define the pathway for applying wear debris analysis in attaining machine reliability. The most important strategies are noted below:
Catch Faults EarlyIn order to minimize the cost of repair and overall business interruption that results from machine failure, problems should be detected at the earliest possible stage. This strategy is simple to understand. We know that problems can frequently be arrested "on the run" if they have not become too advanced or complex.
When little time is left, where a small condition anomaly has led to extensive internal surface destruction, few options remain including the quick fix. Conversely, early detection of failure at its incipient stage often leaves a low cost, planned, and manageable remedy.
Identify Precise Source of Fault The component or part that is ailing is often difficult to identify without tearing the machine down and conducting an internal state inspection. Many different technologies and analytical methods, besides wear debris analysis, play a role in isolating or localizing the problem to a single component or internal part. Often the wearing surface is only confirmed when the forcing function (described below) is ultimately identified.
Identify the Forcing Function Machines that are operated and repaired the same way will tend to wear out and fail the same way. When an abnormal wear condition has been identified, replacing the component (such as a bearing or hydraulic pump) without addressing the cause, or forcing function, will usually result in an identical future breakdown with similar consequences.
Treating symptoms instead of the cause is always wasteful and not best practice. Accordingly, activities that systemically seek out and correct conditions that lead to failure, including those behind any identified abnormal wear conditions, are the most dependable strategy.
Define the Remaining Operating Life
Good estimates of the residual life of operating machinery is always difficult, regardless of the technology deployed. Still, such information is considered valuable in defining the corrective measures and urgency. When combined with all available conditional information, wear debris analysis can assist in estimating how far wear has progressed and the minimal response time.
Wear Particle Analysis Tactics With the goal and strategies of wear particle analysis defined, it is time to look deeper into the details of how information about the health of a machine emerges from the oil and is interpreted by the analyst. It is often these details, or tactics, that will ultimately determine whether the program will realize true success.
And, it goes without saying that those who refuse to be bothered by such details will be met with a decidedly different outcome or destiny. These details will be referred to as "tactics" and are delineated below:
Improve the Quality, Trendability, & Density of the Data Very often we see wear metal data that fails to exhibit consistent or explainable trends. Sometimes the data appears to be fragile, moving erratically without any apparent reason. There are many times when other PdM technologies confirm a problem yet no measurable indication from wear metal analysis appears.
Much of this is found to be caused by poor data quality associated with either the sampling process or the analyses. In other cases the data is too weak or is lost in the noise range. Most of these problems can be overcome by employing modern techniques and tactics. Some examples:
False Positives This can occur due to accidental entry of environmental contaminants or cross contamination from another oil/liquid (either in the instrument, including its solvents/reagents, or from the sampling device). Contaminants entering during the sampling process from the work environment can be controlled by using sampling procedures that don't expose the inside of the bottle or its cap to ambient air. The Clean Oil Sampling method (ref. 1) and the use of properly cleaned sample bottles are recommended.
Additionally, sampling pumps and probes need to be handled carefully using proper procedures to avoid the slightest mixing of the current sample with previously sampled oils. This can occur, for instance, when a tube is removed from a vacuum pump leaving residue behind on the seal which carries over to the next tube that is inserted. For live zone sampling, sampling taps must be thoroughly flushed in advance.
One of the most common causes of false positives occurs when bottom sediment is pulled into sample bottles. This can result in the repository of old debris being misinterpreted as current wear metal production.
False Negatives The main culprit here is the sampling process as well. Sampling needs to be performed in such a way to maximize data density. This means that samples taken in quiescent zones of fluid compartments or dead fluid legs will exhibit low levels of wear metals.
Samples taken when a machine is at rest or during periods of abnormally low loads may show false negatives. Wear particle flyby will occur in hydraulic systems if samples are taken from high velocity lines in laminar flow, 90-degrees from the flow path. In such cases the larger wear particles (greater than five microns) may not enter the bottle at all or in diminutive concentration.
When it comes to wear metal trending it is always a mistake to sample downstream of filters, allowing important data to be stripped from the oil prior to sampling. Equally corrupt is the common process of sampling large centralized reservoirs such as with steam turbines, paper machine lubes, and hydraulic systems. The large volumes of oil in these tanks will dilute wear metal concentrations to levels often below instrument detection limits.
The process of sampling live-zone return lines and bearing drain headers is greatly preferred. In the laboratory, a failure to properly agitate a sample can lead to false negatives. And, it is well known that some elemental emission spectrometers have poor sensitivity to particles larger than five microns, a size range associated with advanced wear.
Normalizing Data With elemental and ferrous density analysis the level and trend of wear metals are distinctly influenced by both the age of the oil and the makeup rate. During normal operation, oil is often lost to combustion or leakage, which carries wear metals with it. The new makeup oil will effectively dilute the concentration of the debris that remains.
Additionally, because most laboratory elemental spectrometers are biased towards particles smaller than filters typically remove (say, less than five microns), stabilized concentrations of wear metals often never occur. Unlike particle counting and ferrous density analysis, with elemental spectroscopy material balance is not achieved between generation and removal (filtration, settling, centrifugation, etc.).
Therefore, where there is continuous rising wear metal levels, even with normal wear conditions, the true add-rate may be missed or understated. Time-based plots of wear metal trends can help reconcile the influence of oil age to better represent rate-of-change (changing slope). Reporting wear metals per 100 hours on oil is yet another way to normalize.
Reducing Data Noise Unfiltered or poorly filtered oil eventually results in growing concentrations of wear debris. The problem is mutually compounding in that the dirtier the oil the more contaminated the oil continues to become from internal wear debris production and destruction to contaminant exclusion seals.
While it is always good advice to maintain clean lubricants from a proactive maintenance standpoint (affirmative action) it is equally good advice for predictive maintenance (early wear detection). A failure to do so usually leads to the alarm signal effectively being "lost in the sauce."
This concentrated debris results in a high noise threshold, and when an incipient wear signal occurs it will write "in the noise" and be lost (signal-to-noise is less than 1:1). This is a persistent problem with splash-fed gearing, crankcase lubes, and bath lubricated bearings.
Conversely, a clean oil provides not only a healthy and unabrasive lubricating environment but also allows the wear signal (incipient debris generation) to write above the noise level (signal-to-noise is greater than 2:1 for example).
When the fluids are maintained clean and if sampling is carried out in live zones (before filters, on bearing drain lines, and at turbulent fluid zones) the early detection of wear anomalies is typically achieved. There is often a need for the routine use of portable filtration systems or retrofitted side-loop filters.
Define Wear Debris Composition
Once confidence can be established in the concentration and quality of the wear metals in the oil, appropriate alarms and limits can be set. These can be based on statistical information that characterizes past normal and abnormal wear metal histories. Alarms can also be based on rate-of-change as previously described.
In cases where a cautionary limit has been tripped the response may be nothing more than more frequent sampling and paying closer attention to other non-conforming or spurious data, including temperature and vibration. If cautionary alarms are consistently reported or there is any single critical alarm, wear particle analysis is triggered.
In order to localize the source of wear metal production, information on composition is important. There are a great many modern methods and technologies to accomplish this. However, too often they are not widely understood and either not deployed or infrequently deployed.
By knowing the machine metallurgy and what the dominant wear metals are, there is improved precision in defining the corrective action, including timing. Below are a few methods that have been reliably applied to “breaking the code” on wear particle composition:
Elemental Spectroscopy Most laboratories utilize inductive coupled plasma (ICP) and spark-arc emission spectrometers. In many industrial applications the particle-size bias of these instruments sharply limits precision in quantifying levels of active wear metals. However, on an exception basis, more advanced techniques are sometimes employed to greatly improve the range of sensitivity with large particles.
These include acid dissolution, microwave digestion, and rotrode filter methods. If wear particles are collected on a membrane or glass substrate, then x-ray diffraction, x-ray fluorescence, scanning electron microscopy and other modern instruments can be used to assess elemental constituents.
Magnetic Flux and Induction The use of a powerful magnet can be very instrumental in identifying the presence of ferro-magnetic debris. Ferrogram makers often combine gravitational deposition with magnetic deposition to distinguish the composition of wear metals. The alignment and location of the debris are examined.
Other methods separate the magnetic debris in advance and then transfer two groups of particles (magnetic and non-magnetic) to two membranes for analysis. Still yet, it is not uncommon to introduce a moving permanent magnet under the filtergram during microscopy.
Those particles that "flicker" are either magnetic or have impacted particles that are. Magnetic induction technology provides for the detection of conductive metals in oils and offer promising performance in wear particle analysis.
Heat Treatment and Optical Methods Many labs commonly apply a variety of optical tricks to help define the composition of wear metals on ferrograms and filtergrams. These include staining particles with colored transmitted light and doing analysis under crossed polars by using two polarizing filters with mutually perpendicular polarizing planes.
Even filtergrams can be examined using transmitted light by applying a clarifying solution to heated nitrate membranes. Reflected metallurgical lighting can be useful where free (reflective) metal particles are present.
The procedure can be assisted by a common heat treatment process if the particles are on a glass substrate. Some metals and alloys will change color or hue from the heat (typically 330 degrees C for 90 seconds) while others do not. For example, the color change for low-alloy steels results from a refractive oxide surface film that forms on the particles under heat, projecting a blue tempered hue.
Other white metals may appear brighter (e.g., aluminum) or develop a mottling color after heat treatment. Lead-based bearing alloys can melt and puddle depending on temperature and composition. Because of the many variations in color, light, and heat effects in identifying particle composition, advanced wear particle atlases are becoming increasingly useful to the microscopist.
Impaction Testing and Chemical Microscopy Some particles are difficult to identify on ferrograms and filtergrams based on appearance alone. In such cases it may be necessary to use mechanical and/or chemical destruction methods.
Chemical microscopy is widely used in forensic science to identify compounds on clothing, skin, and bullet holes for instance. It is now one of the methods deployed to identify wear particles and other debris found on ferrograms. There are many different chemicals that can be applied. For instance, diluted sodium hydroxide will attack aluminum (a fizz results) while nitric acid turns bronze to verdigris.
Impaction testing can be applied to larger particles. Using a pointed tool the particles in question are pressed against the ferrogram or membrane. The result is examined under the microscope. Hard rigid particles will remain intact. More friable particles will crush while others may deform plastically or simply smear under the load.
Elemental Families The exotic metallurgy found in modern machinery will usually consist of numerous elemental composites. When a surface wears the major elements appear (e.g., iron, lead, copper, or aluminum) and in many cases the companion elements (sometimes called minor and trace elements) may also be present in the oil.
The relative concentration of the wear metals helps identify the composition of particles and the likely surface(s) they emerged from. Again, knowledge of machine metallurgy is very important to the successful application of the method. Babbitt for instance can be of many different grades, each with different concentrations of lead, tin, copper, and antimony.
So too, there are many different alloying metals in bronze and brass. Elemental families can also be used to identify tribological pairs and the destructive penetration of clad surfaces. For instance, the presence of iron and chromium (family members) in a diesel crankcase oil emerges from the frictional contacts between the rings and liners.
Particle Shape & Texture The experienced microscopist can compile huge amounts of minute pieces of information to identify the composition of wear particles. In addition to color, light effects, heat treatment, magnetism, etc., the shape and texture of wear particles can contribute important pieces of the puzzle.
For instance, to a trained eye, shape and texture can be used to distinguish between elastomer debris, coal dust, and magnetite, all black in color. Still, not all materials can be identified by shape and texture–the approach often suggesting more what the particle isn't than what it is. The best interpretations result from practice, training, and the availability of reliable reference material such as a wear particle atlas.
Patterns and Combinations The more data and information available to the analyst the more reliable and complete the interpretation. By using companion tests, sometimes performed on an exception basis, one might change a conclusion as the information and facts build.
An example is the case where low levels of ferro-magnetic debris are detected using ferrous density analysis. However, when the oil is then tested using spectrometric analysis, a large amount of iron is present. One might view this as an impossible contradiction. Instead, it could be due to the presence of stainless steel particles or common non-magnetic ferrous oxides such as goethite (rust).
A lock-step trend is a pattern where two or more parameters trend in unison; both in direction and rate. For instance, the trend of a "wear cause" is seen in lock-step with the trend of the "wear effect." Additionally, the introduction of certain contaminants over time might show lock-step trends as in the case of silicon and aluminum from road dust.
Define the Wear Mode
Much can be concluded from the wear debris about machine condition once the composition has been identified. However, the mechanism of wear and the forcing function may remain unclear. Attempts to make repairs or correct problems that don't remove the cause of the failure will inevitably repeat history. This often is the case when an oil or bearing is changed prematurely due to non-complying conditions.
Little information is offered on the wear mode or root cause using elemental analysis alone. However, when combined with ferrous density and analytical ferrography a pictorial story often emerges. The most important of the tools is the microscope used by an analyst trained in tribology. By observing particle size, shape, and texture, various common wear mechanisms can be seen.
For instance, curls and ribbon-shaped particles come from abrasive wear. Large two-dimensional particles can be the product of rolling contact surface fatigue. These methods will not be further discussed, as there is already extensive literature on their use.
Often the root cause presents itself in the oil, making the interpretation of the wear mode a simple exercise. Water contamination explains red iron oxides, while silica dust is often the root cause of cutting wear and platelets. Other lubricant-related root causes that might define the wear mode include wrong oil, high TAN's, fuel dilution, additive depletion, and oxidation.
Sometimes companion technologies can detect the root cause first, such as vibration analysis, in revealing unbalance and misalignment. Evidence of this is then confirmed using microscopic analysis.
Define Severity and Residual Life The application of wear particle analysis to define remaining useful life is still very much evolving, with much yet to learn. There is good evidence that the rate-of-change in wear metal production is either dependent on the intensity of the forcing function or the overall advancement of the condition itself.
In analytical ferrography, experience with past problems can be invaluable in recognizing current abnormal wear conditions and the severity thereof. Many labs keep past ferrograms on file for each machine. These ferrograms provide a quick reference to the wear particle patterns that characterize normal and abnormal conditions.
Additionally, a number of grading systems, using image comparitors, have been established by different organizations to help simplify the process. One such chart employs the influence of wear particle size and concentration. The direct reading ferrograph also offers large and small particle concentration scaling.
Multi-clad journal bearings, such as those commonly used in diesel/compressor crankcase applications and some turbo-machinery, can be monitored using sequential trend analysis. The wear penetration depth can be estimated based on the sequence stage (clad) of wear metal production.
Summary
There are many excellent case studies that have validated the successful application of wear debris analysis in industrial machinery. For these organizations the benefits and savings emanating from increased machine reliability is very real. Success in effectively implementing such programs using wear particle analysis depends on many assorted goals, strategies, and tactics.
Together they form an important plan that, perhaps, depends more on technique and less on technology. For well-engineered programs, wear particle analysis may be the most penetrating and early warning system of all maintenance technologies in use.
References
1. J. C. Fitch, "Clean Oil Sampling, How to Sample Oil Without Opening the Bottle," Practicing Oil Analysis, July/August, 1998.
2. J. C. Fitch, Learning Oil Analysis-Mastering the Data, Noria Corporation, Tulsa, Oklahoma, USA, 1999.
3. Analytical Ferrography Training Notes, Predict DLI, Cleveland, Ohio, USA, 1997.
4. Jian Ding, Wear Particle Atlas, CD ROM, Lubrosoft, 1998.
5. Komatsu Oil Wear Analysis (KOWA) Procedure Manual, 5th Edition.
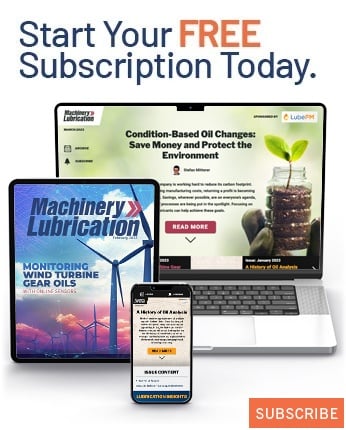