Choosing the correct lubricant for micromechanical parts is not easy, because the parts to be lubricated are very small. As a result, lubricants with specific profiles are needed, especially in terms of for-life lubrication, minimum quantity lubrication and single-application lubrication.
The oxidative and aging stability of the lubricants is one important aspect. Laboratory tests provide the necessary information to evaluate the long-term behavior of lubricants in field applications.
In the lab of Dr. Tillwich GmbH Werner Stehr, a method has been developed to simulate the aging stability of lubricants in an application-adapted procedure, where thin layers of lubricants are aged in contact with catalytic metals and oxygen at high temperatures.
This article combines the results of aging tests on different precision lubricants with the analysis of lubricant failures in micromechanical parts. The transferability of the laboratory results to the expected life of the lubricants under practical conditions is discussed.
Choosing a suitable lubricant for micromechanical parts is made more difficult by their typical requirements. Lubricating such parts is considerably different from that of conventional mechanical components. Because micromechanical parts are small and complex, relubricating the bearing or replacing the lubricant, for example, is out of the question from the start.
An important aspect for choosing a lubricant is the concept of for-life lubrication. In the case of micromechanical bearings, this means that the bearings are lubricated only one time during production with a minimal amount of lubricant, which sometimes amounts to a fraction of a droplet. This small amount must guarantee precise and safe function for the entire service life of the part, which may be several decades.
Evaluating the oxidative and aging stability of the lubricant plays a significant role in choosing the correct lubricant for bearings greased with for-life lubricants. Testing the aging stability should be designed in such a way that conclusions can be made regarding the long-term behavior of the lubricants in real technical parts.
The Dr. Tillwich GmbH Werner Stehr Company has developed a field-oriented procedure to test the aging and oxidative stability of thin layers of lubricants in contact with catalytic metals and high temperatures. This article discusses the simulation method, comparing test results with various lubricants for micromechanical applications. The transferability of the laboratory simulation results to the expected service life of the lubricants under practical conditions is also discussed.
Background
The aging and oxidative stability of a lubricant is generally determined by its chemical composition as well as the character and proportion of respective additives and stabilizing agents. Aging reactions are accelerated by bearing metals, which as catalysts, speed up oxidative reactions with oxygen.
In addition, higher ambient temperatures, wear particles or hostile environmental conditions and gases greatly influence the stability of the lubricants. The importance of evaluating the aging stability of for-life lubricants can be demonstrated by the cases of damage suffered under practical conditions where insufficient chemical stability of the lubricant led to a failure.
Lubricant Aging at High Temperatures
Figure 1 shows a scanning electron microscope (SEM) photograph of a failed sintered bronze bearing from a miniature ventilator. The bearing was lubricated with an ester-based fluid lubricant. As a result of increasing the application temperature from 80°C to 100°C, the ventilator failed prematurely in the component test.
In order to analyze the cause of the failure, the sintered metal bearing was broken at the center and cleaned several times with ultrasound and solvent to remove the adhesive lubricant. After sputtering the parts with gold/palladium, they were examined under the SEM and with energy dispersive analysis of X-rays (EDAX).
Figure 1. SEM photograph of a failed
sintered metal bearing
Dark layers can be seen clearly on the running surface
of the bearing’s cylindrical bore (diameter 2 millimeters)
that were not removed during the cleaning process.
At a higher magnification (Figure 2), the thick layers can be distinguished clearly, which seal the pores of the bearing surface, and therefore interfere with the function of the sintered metal bearing in terms of the oil supply and quiet running. The analysis of the layer demonstrated that it has to do with organic reaction products from the lubricant that was used.
Figure 2. Detailed SEM photograph of the
running surface of a failed sintered metal bearing
Lubricant Aging from a Hostile Environment
A similar failure took place in a spindle drive that actuates an air valve in a heating system. The drive with a spindle made of rustproof steel and a nut made of copper-tin alloy failed after operating for only 10 percent of its service life.
A polyalphaolefin (PAO)-based lubricant was used to lubricate the part. Upon an optical examination of the stuck part under the SEM, one could see that the flanks of the screw threads are almost completely covered with a thick, clod-like coat of material (Figure 3). No wear is detectable.
Figure 3. Detailed SEM photograph of the screw
thread flanks of a nut from a failed spindle drive
When the surface is magnified, one can see that the
coating has solidly adhered to the surface (Figure 4).
Figure 4. Detailed SEM photograph of the
surface of a screw thread flank
Due to the vacuum conditions in the SEM, the
organic layer chips away in places. Here, one clearly
sees the initial machined surface of the screw thread
flank surface.
No wear has occurred.
Exhaust gases from the heating unit condensed on
the spindle, which entered into the lubricant, led to
the rapid build up of organic layers, which caused
the spindle to stick.
Lubricant Aging Due to Wear Particles
When examining the damages to ball bearings from a failed turbomolecular pump in the SEM, organic layers were detected in the ball tracks, which could be partly attributed to the synthetic ester-based lubricant and the PTFE thickening agent (Figure 5).
Figure 5. Detailed SEM photograph of the ball
track of a failed ball bearing
The layer is built up in clods and is reminiscent of
solidified molten material. It adheres solidly to the
ball track surface, upon which no wear is visible
(Figure 6).
Figure 6. Detailed SEM photograph of the ball
track of a failed ball bearing
We agreed that the failure was caused by abrasive
particles in the phenolic resin retainer, which forms
a solid paste together with the applied lubricant.
Due to the increased internal friction of the lubricant,
heat was generated quickly in the ball bearing,
which caused the lubricant to finally gum up completely.
We agreed that the failure was caused by abrasive particles in the phenolic resin retainer, which forms a solid paste together with the applied lubricant. Due to the increased internal friction of the lubricant, heat was generated quickly in the ball bearing, which caused the lubricant to finally gum up completely.
Figure 7. Testing the aging stability of
thinly layered lubricants
Aging and Oxidative Stability
In lubrication testing technology, various testing methods are described, which should provide clues regarding the oxidative stability of lubricants. Nevertheless, evaluating the long-term stability of lubricants using the results of the laboratory simulation proved difficult because the testing conditions of the laboratory simulation deviate from actual application in micromechanical bearings.
In these tests, a relatively large amount of oil, from 20 milliliters to 2 liters, is artificially aged in respective containers in contact with oxygen, catalysts, increased temperatures and/or pressure. In the area of micromechanics and watch-making technology, a modified laboratory test has been set up based on the aging stability test according to Baader DIN 51554.1
In this case, 70 ml of oil was held in a 95°C glass container for 35 days. During this time, atmospheric oxygen was constantly stirred into the warm test oil with a glass stirrer connected to a copper spiral at a rate of 24 strokes per minute. The condition of the oil is monitored by weekly measurements of the viscosity, neutralization value, refraction index and optical aspects.2
When comparing the oil tests from failed parts with the results of laboratory simulations, it was repeatedly detected that different, somewhat more extreme oxidative reactions were triggered in the field conditions.3
If one considers the relatively small amounts of lubricant in a micromechanical bearing, it becomes apparent that there is much more metallic surface related to the oil amount compared to the laboratory test. The same applies to the effect of oxygen, which can attack the lubricant over a large surface.
In addition, we realized that aging is more severe when in contact with two bearing materials, for example, brass and steel, than in bearings made of only one material.
Therefore, it was not possible to directly transfer the results from the laboratory simulation. For these reasons, a test method was developed by the Dr. Tillwich GmbH Werner Stehr Company, which can simulate the oxidative stability of lubricants in a field-oriented procedure.
Aging Tests of Thinly Layered Oil
To achieve the most field-oriented simulation of lubricant conditions possible for a micromechanical bearing, the lubricants will now be time-lapse aged in thin layers on a large surface in contact with catalytic metals. These metals speed up the aging reaction as well as increased temperatures.4
In glass Petri dishes (internal diameter 70 mm, height 13 mm) with a surface area of approximately 38.5 cm2, there are 30 grams of mixed brass stampings made of CuZn39Pb2F49 (variable diameter 1 to 4.5 mm, height 1 mm), which cover the entire inner glass surface in one layer.
This metal layer with a large reactive surface will be evenly covered with 5 ml of oil (layer thickness approximately 2 to 4 mm). One-and-a half-grams of fine pinion wire chips will be spread out on the oil. In addition, 5 ml of oil set up the same way but without the metallic catalysts will be tested. Covered with a glass cover, the test oil will be put into a hot oven at 120°C.
Every two to six days, a minimal amount of lubricant will be removed from the test setup and examined for changes in the infrared (IR)-spectrum. Even slight changes can be detected in comparison to the new oil, for example, a decrease in the additive or the appearance of aging and oxidative products.
An aging test on a PAO, which was stabilized with a phenolic antioxidant, should serve as an example. The initial IR spectrum can be seen in Figure 8. The bands at wave number 3,650 cm-1 and 1,160 cm-1 can be attributed to the additives.
Figure 8. IR-spectrum of an additive PAO at the beginning of the test
(reference measurement)
Under the described conditions, the added additive is depleted within 25 days. Both bands at wave numbers 3,650 cm-1 and 1,160 cm-1 have disappeared (Figure 9).
Figure 9. IR-spectrum of an additive PAO after 25 days
at 120°C in contact with brass and steel
Clear changes can be detected in the IR-spectrum after the test cycle of 32 days has run its course (Figure 10). New bands have appeared in the wave number range between 1,800 cm-1 and 1,650 cm-1, which can be attributed to the oxidative reaction of the lubricant. These are the carboxylic acid, saponification reactions with the catalytic metals and ester.
Figure 10. IR-spectrum of an additive PAO after 32 days at
120°C in contact with brass and steel
The changes that occurred in the laboratory test correspond to a large extent to those that were detected in the IR-spectrum in cases of failure under practical conditions.
If clear aging products are detected in the laboratory test, the test is ended. The change in viscosity and neutralization value of the lubricant are documented, as well as the optical aspect, such as the forming of sediment, silt or changes in color. In the following figures, test oils are shown after completion of the aging test of thin layers. In most cases, the color of the lubricant changes to dark brown. Some sediment forms but remains liquefied (Figure 11).
Figure 11. Thin layer aging test; the oil is still liquefied.
The lubricant can gum up completely in extreme aging
reaction cases. It becomes black and solid, forming a
substance with the metal particles similar to varnish
(figures 12 and 13). Such conditions are also seen in
bearings in field cases.
Figure 12. Thin layer aging test. The oil is
completely gummed up and has taken on a
solid state similar to that of varnish.
Figure 13. Incrustations of aged oil similar to varnish
Figure 14. Plate
Results of long-term tests within the bearing
system of an electromotor, which has been
lubricated by a standard mineral oil based
fluid grease. Temperatures of more than
80°C accelerated aging processes within the
lubricant. Severe oxidative reaction products
could be found on the bearing shaft, which
was covered by lacquer-like, hardly sticking
cracked oil. On the bearing plate the
lubricant has turned its color to black, and
the viscosity has increased by more than
500 percent due to the aging reactions.
Transferring Lab Results to Practical Applications
It is fundamentally difficult to transfer a laboratory simulation directly to a possible process under field conditions. This applies in particular to the simulation of aging and oxidative behavior of lubricants. Therefore, the results of the laboratory simulation should be presented relatively.
If all test results are assessed under the same conditions, a quantifiable statement can be made in a comparative analysis. Consider this example: lubricant A exhibits 50, 100 or 500 percent higher oxidation stability under these test conditions compared to lubricant B.
Calculating the expected life according to the so-called van’t Hoff´s Law also provides hints regarding the field behavior of the lubricant. It states that the reaction speed of a chemical reaction changes with the temperature in such a way that an increase in temperature of 10 K roughly doubles to quadruples the reaction speed.
For example, if a lubricant forms clear aging products after five days at 120°C, the same would take place after 10 days at 110°C, after 20 days at 100°C, etc., and accordingly after only seven years at 30°C. Therefore, the lubricant has an expected service life at room temperature (20 to 30°C) of approximately seven to 14 years.
These estimates were confirmed by experiences in the service sector of the clock industry. Clocks lubricated with conventional clock oils are sent in for repairs within this time frame and are overhauled by the clockmaker. The gummy oil is removed and the bearings relubricated.
Variation of the Test Parameters
The simple setup of the aging test also enables the test parameters to be altered according to the practical applications. The metallic substrate strongly influenced by the aging reaction can be easily replaced with another material, for example, real bearing parts, granular polymer, etc.
An increase in the test temperature is indicated where permanent thermal and oxidative liquids, such as silicone oils or perfluorpolyalkylether, are to be tested. Or the operating temperatures in the practical application are higher than the standard test temperature of 120°C.
Results of the Lab Simulation
Using the test method to accelerate the aging of thinly layered lubricants, easily comparable examinations of various lubricants could be performed. Implementing the test itself is relatively time-consuming. Depending on the stability of the oil, the test can last several months, during which the state of the oil is routinely monitored in the IR-spectrum.
Aging Stability of Lubricants
Figure 15 shows the summary and comparison of the results of the aging tests for thin layers of several important lubricant groups. The days are listed up to the breakdown or gumming of the lubricants at a test temperature of 120°C.
Figure 15. Aging behavior of various micromechanical lubricants;
results of the laboratory simulation (thin layer test)
The aging stability of paraffin-based mineral oils is low. After a maximum of five days at 120°C, the test oils are already severely aged despite being specially equipped with oxidation inhibitors.
PAOs, polyglycols and dicarboxilic acid ester have a clearly better aging behavior. Equipped with an optimized additive package, they are destroyed after approximately 20 to 30 days under our test conditions. Several representatives of the trimellitate esters group are thermally stable. They reached a test duration of 90 days at a temperature of 120°C.
Perfluoropolyalkyl ethers and silicone oils achieved the best aging results. Even at 120°C and 150°C they are not destroyed within a time frame of more than two years under the chosen test conditions.
The viscosity of the silicone oils merely increases in a range of 1 to 10 percent compared to the initial value. Silicone oils can be exposed to constant temperatures between 120°C and 150°C depending on their chemical composition; perfluoropolyalkyl ether up to 260°C.
Influence of Lacquer and Adhesive Vapors
A modified aging test reconstructed how quickly the ambient conditions of the aging and oxidative reaction in a lubricant can accelerate. In this case, the Petri dishes containing the test lubricant were not covered with a glass cover, but instead were left open in another bigger specimen glass.
In addition, another Petri dish with a phenolic adhesive was included. This adhesive should be used in the field to attach the part housing. The hardening specifications of the phenolic adhesive were followed precisely.
The specimen glass containing both Petri dishes, with the test lubricant as well as the phenolic adhesive, was closed airtight and placed in the hot oven at 120°C.
At this point, the atmospheric oxygen contained in the specimen glass and possibly the phenolic adhesive vapors that arise at the gaseous phase were a part of the aging reaction. Two synthetic esters were tested, as well as a PAO-based lubricant and a perfluoropolyalkylether.
Figure 16. Aging behavior of various micromechanical lubricants;
results of the laboratory simulation (thin layer test)
Figure 16 shows the results of this aging test compared with the results of the standard test method at 120°C without the influence of phenolic polymer. Without the influence of phenolic polymer, the aging stability of the four oils is different. The achieved test time varied from 30 to more than 130 days.
The phenolic polymer vapors influence the aging behavior of the lubricants to a certain extent. The synthetic ester I is completely aged after only 12 days, which is only one-third of the stability under normal conditions.
By comparison, the influence of vapors on the synthetic ester II is lower. The oil is destroyed after 87 days. The behavior of the PAO-based oil is astonishing. The phenolic polymer vapors improve its oxidative stability compared to standard test conditions. The perfluorpolyalkylether-based lubricant behaved absolutely inertly. It was not attacked throughout a time frame of more than 130 days. It was decided to discontinue the test.
With the field-oriented test method to simulate the aging and oxidative stability of thinly layered lubricants in contact with catalytic metals and high temperatures, a procedure is available to evaluate the application of for-life lubricants for micromechanical parts.
To a large extent, the laboratory simulation test conditions are consistent with those of actual bearings, so that a good correlation is achieved between the laboratory results and field experiences.
Editor’s Note:
The implications of this research for large grease-lubricated machine applications are these: Popular test methods for grease oxidation and work stability incorporate bulk-like conditions that may not effectively emulate the actual conditions that the grease experiences in the real world (multi-metal, thin film, dynamic shearing conditions). We may have a poor understanding of just how the grease really behaves (rate of degradation, rate of worked consistency change) once in service, despite the fact that we believe our assumptions from the test results.
References
- DIN 51554: Testing of mineral oils. Test of susceptibility to aging according to Baader.
- Glaser, G. and Tillwich, M. “Tribologie in der Uhren- und Feinwerktechnik” (Tribology in Clock and Precision Mechanics). Handbuch der Chronometrie und Uhrentechnik (Handbook of Chronometry and Clock Technology), Volume II/9b, Ch. 8.4. Publisher: Prof. Dr. Günther Glaser, Stuttgart, 1987.
- Tillwich, M., Stehr, W., Dresel, W. and Stubenvoll, M. “Schmierstoffe in der Feinwerktechnik” (Lubricants in Precision Mechanics). Schmierungstechnik und Tribologie (Lubrication Technology and Tribology), Volume 29, 5/1982.
- Beyer-Faiß, S. “Schmierstoffe in der Feinwerktechnik.” Tribologie und Schmierungstechnik (Tribology and Lubrication Technology), Volume 50, 5/2003.
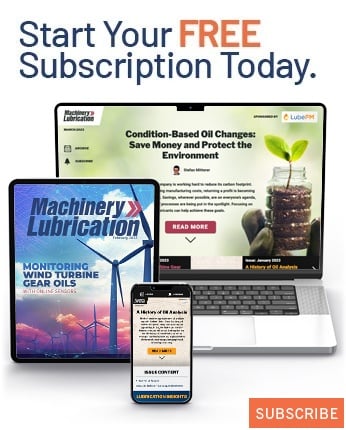