The majority of chains used in industry suffer unnecessarily short lives. This leads many companies to forego chains all together and replace them with belts. In most cases, however, the problem is not the fault of the chains but rather the method in which they are lubricated.
The current chain lubrication practice consists of applying a heavy oil or grease to the outside of the chain. While this does a nice job of lubricating the sprockets and the outside of the chain, it does little to protect the most vulnerable area of the chain: the contacting surfaces inside the pin and bushing/ plate/ roller/ hook.
The majority of chains fail from the inside. They stretch or kink up due to wear and corrosion wear inside the pin and bushing area. To lubricate them properly, the lubricant needs to be engineered to penetrate and clean the inside of the chain, clean the inside of the chain (to remove contaminants and displace any trapped water that it encounters) and leave behind a heavy film of oil, grease or solid lubricant.
Figure 1. Types of Roller Chain and Where to Lubricate Them
A penetrating-type chain lubricant not only displaces water, but also cleans dirt and wear metals out of the pins of the chain and off of the sprockets. It is essentially an oil change for the chain.
The operating conditions (including load, environment, temperature and speed) must also be considered. Maximizing chain life requires attention to detail and the selection of a suitable lubricant.
The method of lubrication is equally important. Regardless of whether the application of the lubricant is accomplished manually or by use of an automatic system, the lubricant needs to be aimed into the pin and bushing area. Figure 1 illustrates where the lubricant should be applied to several types of chain.
Lubrication is required between the rollers and bushings, but other important areas to lubricate are the pin and bushing surfaces, which articulate with each other while the chain is under full load. To reach all of these surfaces, the lubricant should be applied to the upper edges of the link plates on the lower strand of the chain shortly before the chain engages a sprocket. Then, as the chain travels around the sprocket, the lubricant is carried by centrifugal force into the clearances between the pins and the bushings. Spillage over the link plates supplies lubricant to the interior and the end surfaces of the rollers.
Chain lubricants should have the following characteristics:
- Sufficiently low viscosity to reach the internal surfaces – a carrier solvent or penetrating component helps to achieve this without lowering the operating viscosity.
- Sufficient body to maintain the lubricating film under the bearing pressures – solid lubricants can help.
- Freedom from corrosive ingredients.
- Ability to maintain lubricating qualities under different temperatures, moistures, etc.
Tailoring the lubricant to the specific operating environment is helpful.
Dusty Environments
Chains operating in a dusty environment benefit from a product that is a combination of penetrating oil and lubricant. This dual-purpose lube is useful because the oil penetrates to the inside of the chain with oil but leaves the outside of the chain nearly dry. Penetrating oil alone doesn’t work nearly as well.
In extremely dusty environments, such as in a cement plant, a solvent containing antiwear additives (such as a fuel supplement) lubricates chains that would otherwise run completely dry. This extends the life of these chains without attracting dust or causing buildup on the chain.
Case Studies
Carbrook River Sands in Queensland, Australia, supplies a number of different processed sand products including filling sand for sidewalk paving blocks, bagged concrete and mortar mixes for export to places like Hong Kong, and refined filter sand for supply to water purifier companies around Australia.
The plant uses a forklift with a lifting capacity of two and one-half tons, which necessitates the use of a multiplate link-type chain. Working nearly eight hours a day in a dusty environment, these chains which were lubricated with engine oil would run dry after only a short time. Switching to a penetrating type of chain lubricant extended the life of the chain and prevented dust from sticking to the chain and working its way into the chain links.
Previous lubrication with engine oil in that dusty environment produced a fine grinding paste that obviously shortened the life of the chains. A replacement cost of $300 plus downtime was a costly inconvenience. The cost of lubrication is now reduced with an almost disproportionate increase in the life of the chains.
Wet Environments
In a humid environment (such as a pulp mill), or where chains are subject to water wash-down (such as food plants), it is imperative to displace water from the chain on a regular basis by using a penetrating type of chain lubricant. Regular oil and grease are nonpolar and therefore unable to grab onto the water and remove it. A polar organic solvent included in the formulation of the lubricant works best.
If the chain is running through and/or is immersed in water, a combination of penetrating oil and tacky grease is the best method. This forces the water out initially, and then seals the inside of the chain to prevent water from getting in.
Case Studies
Federal Beef Processors in Rapid City, South Dakota lubricated its drive chains on a daily basis. The company needed a USDA H1 food-grade lubricant that would last longer and resist the high moisture in the plant. By switching to a penetrating-type food-grade chain lubricant, the plant now lubricates the chains only once a week.
Atwater Foods in Lyonville, New York also achieved success using the same USDA H1 food-grade penetrating oil and lubricant in a similar chain application throughout its plant. Oscar Cotton, the lead mechanic stated “I’ve been working with equipment for 62 years, and this is the best lubricant that I’ve used. It penetrates faster than any other penetrating oil I’ve used.”
At Maple Leaf Pork in Brandon, Manitoba, Canada, a 1 km (3,280 feet) long quick-chill chain carries pigs through the quick-chill freezer at -45°C. On Monday morning at start-up, this chain would repeatedly jam due to water frozen in its links, causing four hours of downtime at the start of every week. A chain spray system with six nozzles was installed to spray a combination of air and three liquids into the pin area of the chain. Food-grade alcohol is applied to dissolve the ice, then a food-grade penetrating oil and lubricant is applied to displace the water. A synthetic food-grade oil with a pour point of -57°C (-70°F) is then applied to lubricate the chain effectively, even at -45°C. This solution has resulted in a savings of four hours of downtime per week.
A metal parts manufacturing plant in Western Canada was experiencing short life (three months) on a parts chain running through a water bath. By applying a synthetic penetrating-type chain grease via aerosol, the life was extended to several years.
At Schlumberger’s gas meter manufacturing plant in Owington, Kentucky, the parts washer conveyor chains were failing regularly at a cost of $4,300 each. The plant replaced a chain on each machine every three to four months, for a total of six to eight chains per year. It took two workers eight hours to change each chain at a cost of $11 per hour. The lubricant was changed to a penetrating type of chain lubrication, which penetrated into the chain and left behind a heavy-bodied (ISO 100) oil.
The results were dramatic. There was no rust showing even after 10 months service, while the previous lubricant showed rust in the first two to three hours after application. Lubricant consumption has been reduced from 15 drops per minute to two to three drops per minute. Schlumberger estimates that it has saved more than $31,000 per year in lubricant, labor and parts costs alone (downtime not included). Don Renfro, maintenance superintendent said “The chains are running the best they have in 18 years.”
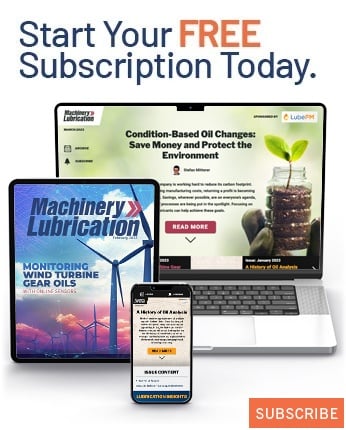