Oil whirl is probably the most common cause of subsynchronous instability in hydrodynamic journal bearings. Typically, the oil film itself flows around the journal to lubricate and cool the bearing. This develops an average speed slightly less than 50 percent of the journal surface speed (Figure 1).
Normally, the shaft rides on the crest of an oil pressure gradient, rising slightly up the side of the bearing somewhat off vertical at a given, stable attitude angle and eccentricity. The amount of rise depends on the rotor speed, rotor weight and oil pressure. With the shaft operating eccentrically relative to the bearing center, it draws the oil into a wedge to produce this pressurized load-carrying film.
Figure 1. Oil Film Within a Journal 1
If the shaft receives a disturbing force such as a sudden surge or external shock, it can momentarily increase the eccentricity from its equilibrium position. When this occurs, additional oil is immediately pumped into the space vacated by the shaft.
This results in an increased pressure of the load-carrying film, creating additional force between the oil film and shaft. In this case, the oil film can actually drive the shaft ahead of it in a forward circular motion and into a whirling path around the bearing within the bearing clearance.
If there is sufficient damping within the system, the shaft can be returned to its normal position and stability. Otherwise, the shaft will continue in its whirling motion, which may become violent depending on several parameters.
Oil Whirl Instability
Oil whirl demonstrates the following characteristics:
1. Oil whirl can be induced by several conditions including:
-
light dynamic and preload forces
-
excessive bearing wear or clearance
-
a change in oil properties (primarily shear viscosity)
-
an increase or decrease in oil pressure or oil temperature; improper bearing design (sometimes an over design for the actual shaft loading)
-
fluid leakage in the shroud of blades and shaft labyrinth seals (so-called “Alford force” or “aerodynamic force”)
-
change in internal damping (hysteretic, or material damping, or dry (coulomb) friction)
-
gyroscopic effects, especially on overhung rotors with excessive overhang.
Any of these conditions can induce oil whirl after a disturbing force induces an initial rotor deflection.
2. Sometimes machines exhibit oil whirl intermittently due to external vibratory forces transmitting into the unit or from sources within the machinery itself. In these cases, these vibratory forces have the same frequency as the oil whirl frequency of that bearing and can contribute just the right magnitude of disturbing force at just the right tuned frequency to set the shaft into the whirl motion.
This vibration transmits from other machinery through attached structures such as piping and braces, or even through the floor and foundation. If this occurs, it may be necessary to either isolate this machine from surrounding machinery, or to isolate the offending machine itself.
3. Oil whirl is easily recognized by its unusual vibration frequency which is generally 40 percent to 48 percent of shaft RPM. (Reference 2 states that pure oil whirl occurs at 43 percent of shaft speed, but that the instability may occur at the first critical speed.)
4. Figure 2 shows the development of oil whirl just after the shaft is brought up to speed. Note that the shaft went into whirl at a machine speed of approximately 1,800 RPM and remained in whirl until about 4,000 RPM.
At this point, note that the shaft 1X RPM speed entered resonance, which actually generated sufficient force to overcome oil whirl. However, once the machine passed through resonance, whirl once again occurred just above 5,200 RPM.
Figure 2. Development of Oil Whirl
Just After Startup; Followed by Oil Whip
from 9,200 to 12,000 RPM 3
5. Oil whirl is considered severe when vibration amplitudes reach 40 to 50 percent of the normal bearing clearance. At this point, corrective action must be taken.
6. Temporary corrective measures include changing the temperature of the oil (thus, the oil viscosity), purposely introducing a slight unbalance or misalignment to increase the loading, temporarily shifting the alignment by heating or cooling support legs, scraping the sides of or grooving the bearing surface to disrupt the lubricant wedge, or changing the oil pressure.
7. Permanent corrective steps to resolve the oil whirl problem include installing a new bearing shell with proper clearances, preloading the bearing by an internal oil pressure dam, or completely changing the bearing type to oil film bearings that are less susceptible to oil whirl (including axial-groove bearings, lobed bearings or tilting pad bearings).
The tilting pad bearing is a good choice because each segment or pad develops a pressurized oil wedge tending to center the shaft in the bearing, thereby increasing the system damping and overall stability.
Oil Whip Instability
Oil whip occurs on those machines subject to oil whirl when the oil whirl frequency coincides with and becomes locked into a system’s natural frequency (often a rotor balance or critical speed frequency). For example, refer to Figure 2.
When the rotor speed increased to just above 9,200 RPM, its speed increased to 2X its first balance natural frequency. At this time the oil whirl which was approximately 43 percent of RPM, was brought into coincidence with this critical speed. The oil whirl was suddenly replaced by oil whip - a lateral forward precessional subharmonic vibration of the rotor.
At this point, the oil whip frequency remains the same, independent of the rotor RPM. Note that the oil whip frequency never changed even though the machine continued up in speed to 12,000 RPM. When a shaft goes into oil whip, its dominant dynamic factors become mass and stiffness in particular; and its amplitude is limited only by the bearing clearance.
Left uncorrected, oil whip may cause destructive vibration resulting catastrophic failure – often in a relatively short period of time.
Dry Whip
Dry whip occurs in journal bearing machines subjected to either a lack of lubrication or the use of the wrong lubricant. When this occurs, excessive friction is generated between the stationary bearing and rotating journal. This friction can excite vibration in the bearing and other components.
This kind of vibration is called dry whip. Dry whip can also be caused by journal bearings having excessive clearance as well as those having insufficient clearance.
The dry whip condition is similar to rubbing a moistened finger over a dry pane of glass. It will generate a frequency specifically dependent upon the shaft and construction materials, geometries and lubricant properties. Normally, this frequency will produce a high squealing noise similar to that generated by dry rolling element bearings.
The frequency content itself will not be an integer multiple of the machine speed. When dry whip is suspected, it must be taken care of quickly in order to prevent a potential catastrophic failure. And when dry whip is suspected, both the lubricant itself and the lubrication system should be closely inspected and the bearings should be checked to ensure they have proper clearances.
References
- Berry, James E. “Applications of Time Waveform Analysis.” Analysis II – Concentrated Vibration Signature Analysis and Related Condition Monitoring Techniques. Chapter 6, Pages 6-72 to 6-75, 2002.
- Mitchell, John S. “An Introduction to Machinery Analysis and Monitoring.” Tulsa, Okla.: Pennwell Publishing Co. Pages 141-151, 172-204, 1981.
- Bently, Donald E.; Zimmer, Siegfried; Palmetier, George E.; and Muszynska, Agnes. “Interpreting Vibration Information from Rotating Machinery.” Sound and Vibration magazine. Volume 20, No. 2. Pages 14-23, February 1986.
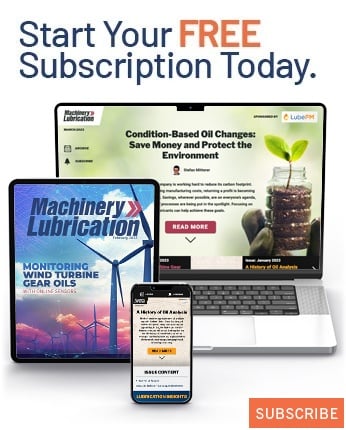