Experts agree that the best way to overcome a catastrophic machine failure is not to have one. However, those in the maintenance field understand that machine reliability comes at a price.
Monitoring key performance indicators of machine reliability alone may fail to control wasteful and ineffective expenditures that were half-heartedly intended to reduce failure and downtime.
To the other extreme, initiatives that slash current maintenance expenditures without considering long-term reliability consequences are frequently a penny wise and a pound foolish.
For most companies, you are what you measure. Metrics shape and define an organization. We’ve all been subject to various measurements since the days of our childhood.
Those early experiences ranged from the winning score of our little league baseball game to the painfully serious day we brought home a low grade on a school report card.
We’ve learned that what counts is what is measured, as well as its logical corollary … what gets measured gets done. I envy the person who first spoke those words.
I’m always curious to see the charts and graphs posted on the bulletin board outside a supervisor’s office. A quick glance at these measures pretty much defines the performance goals of the group that he manages.
An astute manager will carefully align charts and graphs to those metrics that trigger his annual bonus and increase his prospects for promotion. Even wiser business leaders consider long-term business opportunities and design strategic goals and metrics to maximize shareholder value, employee morale and brand loyalty.
Modern maintenance strategies involve the deployment of many performance metrics directed at optimizing (not maximizing) machine reliability.
A well-conceived maintenance dashboard is a command post of key performance indicators, some leading indicators (what’s going to happen), and some lagging (what did or is happening). It broadcasts those measures that are the most important at a macro level but enables greater detail and specificity on command.
A reliability command post should report good news and bad news in near real time, depending on priority (risk, criticality, etc.). I’ve always believed in getting bad news fast while it is still manageable.
The most serious “code red” alerts should be quickly enunciated to planners and schedulers to allow prompt interventions to be carried out on the fly. Afterward, make a habit of performing root-cause failure analysis to ensure that the offending cause is not allowed an encore.
So for those of you who are metric manics, be careful what is measured. Most people are programmed to work to the metric. Selecting the right mix of metrics has the potential to produce stellar performance. However, if you make metric mistakes, you sadly risk unrealized goals or even disaster.
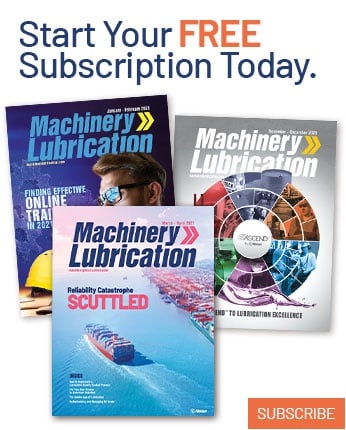