A number of months ago I was invited to participate in a planning meeting for re-engineering oil analysis at a large industrial plant. Shortly after taking my seat, introductory remarks were made by the superintendent of maintenance to set the stage for the work ahead. To my surprise we were told to develop a strategy that would allow machine repairs to be carried out on a scheduled basis in-stead of the predominantly unscheduled practices of the past.
Why was this a surprise to me? After all, isn't this what predictive maintenance is designed to do; forecast impending failure? And, wouldn't it be a wonderful thing to always be able to plan repairs, avoiding the costly business interruptions that accompany breakdown maintenance? Many would answer yes to both questions but let's take a more critical look at the situation.
What the superintendent was referring to is known in some circles as "just-in-time" maintenance. It is wrench-driven, same as before, but replaces firehouse emergent repairs with a managed activity of scheduled repairs. It is clearly more civilized, even eliminating the unpleasant element of surprise.
So what's missing? How could it be improved? Let's start with timing. Many machines wear (fail) slowly over a period of months or years. It is typically a silent process, liken to slow progressive disease. Left alone and wear debris turns to shrapnel and vibration builds to a drum roll. The condition of the machine is no longer a mystery; we are approaching failure. But why let failure grip the machine at all?
There's an alternative with a big return. Timing relates to the zone of detection. When will the problem be detected – when it's a cause or when it's an effect? Are we approaching crash and burn and a major repair, or is it a minor problem that can be arrested on the run? By choosing early-detection instead of just-in-time there are fewer problems to correct and those problems that do arise have simple solutions.
Oil analysis offers many opportunities to target early detection. It's simply a matter of defining your strategy and choosing your weapon. This issue of Practicing Oil Analysis is chock-full of tips and tactics for harnessing the benefits of early detection. So if you want to turn your program into a feisty profit center, spend time with:
NASA Langley–Cost cutting onsite oil analysis strategies for proactive and predictive maintenance.
SiliconEnemy Number One–Interpreting the most destructive element found in used oils.
Arizona Public Service–Real success from applying penetrating fault-detecting technologies.
Feature Lab, Engineered Lubricants–This lab applies cutting-edge technology in monitoring additive attrition and wear metal production.
Port of Tacoma–Big savings from monitoring and controlling the beastly little particles in oil.
X-Ray Fluorescence–Learn how to detect faults and failures early with this promising technology.
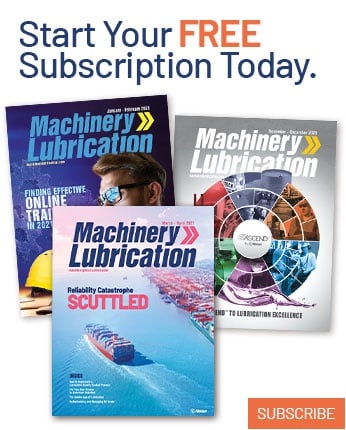