With the recent push for better contamination control, maintenance personnel have become familiar with terms such as beta ratio, ISO cleanliness and offline filtration. Oil analysis results show that there is a drive to achieve a higher level of cleanliness in equipment.
It has been proven that oil cleanliness is tied to improved machine reliability. This drives interest in contaminant control and removal measures. This column focuses on the contaminant removal measures for a particular gearbox.
The use of portable filtration and the installation of hard piped (kidney-loop) filtering methods is on the rise. When utilizing these practices, it is important to understand that they affect more than just the level of cleanliness.
All too often a client reaches a targeted level of cleanliness on a piece of equipment and then increases the oil sampling interval from 30 days to 180 days or even longer. This can be a catastrophe waiting to happen!
Case Study
Consider the failure of a highly critical gearbox. At the time of the failure, the oil analysis program was certainly not one of world-class status. The facility was fortunate that few failures had occurred since the decline of the program. This gearbox finally decided it had served long enough.
During a routine lubricant and filter change, the client noticed a large amount of metal wear debris on the filter. An internal inspection revealed a broken gear tooth. Because it was a filtered gearbox, the client sent an oil sample from the sump as well as a filter sample to the lab for failure analysis.
The results of the oil sample were alarming at first, because no adverse conditions were readily obvious. Generally speaking, while it is not possible to establish alarm levels based upon a single oil sample, it is possible to create generic alarms based on similar equipment.
For example, in this case spectrometric analysis would not have exceeded any alarm limits, but the ISO cleanliness level was high considering the level of filtration fitted on this unit.
It was obvious that some evidence of failure must exist in the lubricant, given that this was indeed a mechanical failure of the gearbox. A request was made for the laboratory to perform analytical ferrography on this sample to determine the root cause of failure. Even with in-depth analysis, a final conclusion could not be made.
The level of abrasive wear noted in the ferrographic report indicated a wear mode requiring minor maintenance (filter replacement, breather inspection/ replacement, viscosity adjustment) rather than that of a failed system. The level of abrasive wear noted on the ferrogram was consistent with the amount of dirt debris noted in the AES analysis.
Additionally, a normal amount of ferrous rubbing wear was visible at 400X magnification. Some ferrous cutting wear, which would be a result of the abrasives found in this sample, was also observed.
Given the results of the regular oil analysis test slate and the analytical ferrography that was performed, the probable cause of failure could not be determined.
The decision was made to run wear metals testing on the oil trapped in the filter. This oil told a completely different story (Figure 1).
Figure 1
As expected, spectrometric analysis differed significantly between the sump sample and the filter sample, which can be explained by several factors. First and most important is the sampling method. This gearbox sump was sampled via drop tube sampling. Drop tube sampling is not consistent with best practices because it is difficult to obtain a representative sample.
It is likely that this gearbox had been shutdown long enough for wear debris to settle to the bottom prior to sampling. Secondly, the aftermarket submicron filtration resulted in the removal of severe wear debris which results in a higher concentration of these fines in the filter sample.
Analytical ferrography was also performed on the filter sample. Wear particles in excess of 30 microns were observed from the filter, and abrasive contamination as large as 125 microns was present. These results suggested that the failure was caused by excessive environmental contamination. In this case, the contamination was most likely entering the system via steel mesh-style breathers.
The system filter element in this application contained the secrets behind the failure. The lubrication technician deserves credit for noticing the wear debris on the filter and doing something about it. Without the critical information trapped in the element, this critical component could have run to failure with no detection until the failure.
When applying filtration to equipment, it is important to realize that all particulate matter will be reduced, which will eventually result in a lower level alarm for the filtered unit. Additionally, stretching out an oil analysis interval in an attempt to cut costs can quickly and easily result in a large penalty at a later date because of missed opportunities.
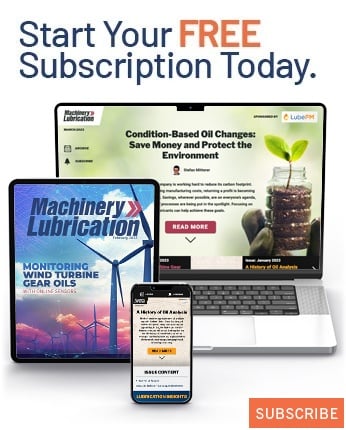