Editors Note:
Our first issue of Practicing Oil Analysis featured an article describing the remarkable success of Arizona Public Service in integrating oil analysis with vibration analysis. The reported fault detection efficiency from oil analysis was a surprise to many readers who sent in questions and comments asking for more detail. The following short article was prepared by the captains of this extraordinary program in response to these requests. Bryan Johnson has responsibility in lubrication and Howard Maxwell with vibration.
I think after reading the following paragraphs you will agree that what they have to say is of no small importance to the field of condition monitoring. - Jim Fitch.
A predictive maintenance program's success may be measured in many ways. The program goal should be more than to keep machinery from failing catastrophically. It should have a clearly defined strategy for success that provides PdM recommendations at the lowest possible cost to the facility. One type of success may be to remove a monitored piece of equipment just before it can catastrophically fail.
Predictive Maintenance Used to Plan Maintenance. 'Just in time' predictive maintenance can be a valid program strategy, this type of strategy may have a short-term benefit of maximizing run time prior to the repair.
A disadvantage is that it probably will increase the overall cost of the repair since more extensive or secondary damage to the machine or system may develop and that the repair often is performed as an emergent work activity. Although a correct repair recommendation has obvious benefits, it also has the effect of displacing previously planned work and often results in unplanned overtime charges.
The success of another predictive maintenance program strategy may be measured by the reduction in cost associated with a repair by minimizing the number of parts and man-hours needed to restore the equipment to satisfactory operating condition.
An example of this type of repair may be found in a gearbox. If a bearing begins to fail, some portion of the generated debris will remain in suspension in the bulk oil and can be expected to cause accelerated wear of the gears and other bearings.
An 'early wear repair' strategy may reduce the scope of the repair to the replacement of a single bearing set that would have minor damage. The principal additional cost of this strategy is the loss of some operating time that the old bearing may have provided.
Another strategy attempts to take the 'early wear repair' strategy further by performing each repair as a non-emergent work activity. This strategy attempts to schedule a Predictive Maintenance' repair recommendation as work integrated into planned plant work.
For this strategy to work, the Predictive Maintenance program must be able to forecast the need for a repair far enough in advance to allow the repair to be integrated into the normal flow of scheduled maintenance activities. In addition to reduced material and scheduler costs, this strategy tends to preserve evidence of the failure mechanism and improves the quality of the root cause of failure evaluations.
![]() |
Figure 1
|
The predictive natures of lubrication, vibration and thermography techniques can be used for more than avoiding a catastrophic failure. The technologies can be used to minimize the occurrence of emergent repair recommendations.
A program's philosophy should be to take advantage of the strengths of each technology to allow longer-term projections of available service life due to a degrading condition. An overall program goal should be to forecast as many repair recommendations as possible as routine scheduled work.
Each plant or facility will have planned operation cycles with clearly defined maintenance windows. At the Palo Verde Nuclear Generating Station, many scheduled maintenance intervals for given systems or equipment allow work to take place every 3, 6 or 18 months.
The challenge to the Predictive Maintenance Program is to provide reliable detection of degrading conditions that will minimize secondary machine damage, allow preplanning and place the repair into a routinely scheduled time slot.
Integrated PdM Technologies Extend Forecasting Capabilities. The challenge can be met by making use of the inherent strengths of each predictive technology used and through the integration of their resulting data. Anti-friction rolling element bearings are a common Predictive Maintenance repair recommendation. When a bearing failure begins, lubrication analysis should be the first technology to detect the degradation.
Micron sized wear particles are initially generated during many failures. These particles can be readily measured with oil analysis; however, due to their small size, the resulting defects do not cause sufficient energy to allow vibration detection.
Initial wear particles generated are in units of micron to sub-micron. As the bearing condition changes with time, so will the size and severity of wear particles and the defect size. This progression can be monitored with both lubrication and vibrational techniques once the defect-initiated energy level allows detection using vibration techniques. Integrated use of both technologies extends the period of time that the condition can be monitored.
An oil program allows the viewing of wear particles using a microscope. The size and shape of the particles provide information about the wear mechanism taking place within the bearing. A wear debris analysis of magnified particles used in conjunction with data obtained from vibrational analysis and machinery operating conditions improve a PdM program's ability to forecast when a failure would be expected to progress to secondary damage and/or become catastrophic. Many of these forecasts can be made months in advance.
Figure 1 shows a pie chart of several recent bearing repair recommendations. At first glance it may appear that neither the lube nor vibration program were very successful at monitoring the bearing condition; however, this is not the case.
The available maintenance work outages were reviewed to determine when the repairs could be made as non-emergent work. The repair opportunities guided the date that the repairs were scheduled under the program goal of minimizing secondary damage and avoiding a catastrophic failure.
Of the bearings replaced, the lubrication program identified only 40%. These bearings all had clear evidence of damage using lubrication test methods such as Spectroscopy wear metals analysis and microscopic evaluation of wear particles.
The available routine repair windows for these bearings were typically every 18 months. The analysis estimated the remaining life for these bearing to be less than 18 months. The bearings were inspected and had clear, but infant damage that would not have readily presented itself using vibrational techniques. In other words, the bearings were replaced before the vibration indications would have begun.
If these bearings had been allowed to run to failure, all of them would have shown vibration symptoms before the failure.
The vibration only identified bearings in the Figure 1 chart were typically grease lubricated. Used grease samples present challenges to a lubrication monitoring program and are not widely tested. These repair recommendations were generally forecasted to allow reliable operation of at least 3 months.
The portion of Figure 1 identified by both the lubrication and vibration programs were typically oil lubricated bearings. They were identified as having degrading conditions and monitored over a time period of several months prior to scheduling the repair. These bearings had available maintenance repair opportunities of 3 to 6 months. Most repair recommendations were implemented on a planned basis. More extensive damage was found in this group of bearings than those repaired with lubrication data only.
The fractions in Figure 1 do not suggest that the vibration program and lube programs are only successful 60% of the time. The real interpretation is that for bearings monitored by the lubrication program (oil lubricated), the success rate is near 100%. The vibration program success rate would have been near 100% except for the longer range forecasting ability of the lube program, which corrected the bearing conditions prior to additional degradation.
The data does suggest that there is a portion of the failure history of a bearing that lube techniques can detect that current typical vibrational techniques can not. This indicates that there is potential for advanced vibrational technologies to push the 'predictability envelope' of bearing failures.
All of the bearing repairs were considered program successes. While some of these were 'just in time' repair recommendations, most were made allowing the work to be routinely scheduled. Finding extensive damage as a result of a Predictive Maintenance repair recommendation may indicate that the condition has not been effectively monitored as the degradation has progressed.
'Just in time' predictive maintenance is a necessary component of a program strategy; however, a PdM program should not be 'surprised' to find a late stage degraded machine condition. It is possible in many industrial settings to monitor a degrading condition over a period of several months and optimize the cost of the repair. The highest quality strategy is one that has the lowest overall cost. When considering a program strategy, consideration should be given to recommendations that reduce the frequency of emergent work.
References:
Maxwell, Howard and Johnson, Bryan; "Vibration and Lube Oil Analysis in an Integrated Predictive Maintenance Program"; Proceedings of the Annual Meeting of the Vibration Institute, June, 1997.
Editor; "Oil Analysis Success at a Power Generation Station"; Practicing Oil Analysis, July/August 1998
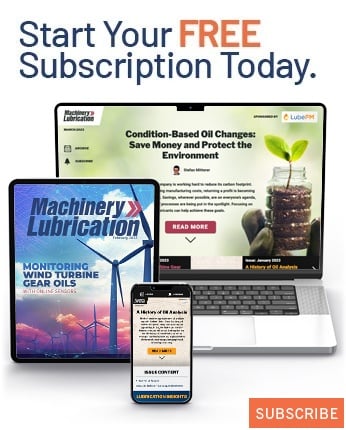