Some equipment owners view oil analysis as a tool to help determine when to perform an oil change. Some view it in terms of the fault detection ability. Still others apply it to a strategy for contamination control and filter performance monitoring.
But the best strategy is to incorporate all these aspects of oil analysis together into one program, which will ultimately meet reliability goals. The key is to define the goals and design the program to achieve those goals.
The following case study is an example of how an effective oil analysis program has been used as a predictive maintenance tool in determining when an oil change was needed, a contamination issue arose or an abnormal wear condition was present.
Hydrogen Recovery Compressor
This case study relates to a hydrogen recovery system in a refinery application. The system uses three flooded screw machines for the first two stages of compression and a reciprocating compressor for the third stage of compression.
Table 1. Process Conditions
The first stage of compression uses two Mycom model MXG320 LLUD-M flooded screw machines, while the second stage uses one Mycom model MXG320 MUD-L machine. The hydrogen recovery system contains various gases that make reliable operation difficult (Table 1). Figure 1 illustrates the process.
The first stage where the first two compressors are used takes input streams from various units at 2 psig and 100°F. The various units yield a gas composition of mainly hydrogen, H2S, C1, C2, C3 and IC4 with lower amounts of other components.
Figure 1. Process Flow Diagram,
Hydrogen Recovery System
A suction drum is placed before the compressors to drop out any residual liquids. The gas is then compressed through the machines to a discharge pressure of 65 psig at 208°F. The gas is then cooled and other process streams enter the system.
The gases then go through another suction drum to drop out any residual liquids before entering the second stage. The second state compressor compresses the gases to 173 psig at 169°F. The flood oil is maintained at 140°F at the inlet to the compressors.
Lubricant Selection
Due to the severity of the process stream and the interaction between the process steam and the lubricant, a lubricant that has low solubility with hydrocarbons is required.
The oil recommended by the OEM for the compressor is a polyalkylene glycol (PAG) lubricant with an ISO VG grade of 100. The lubricant is a highly engineered product with H2S inhibitors, copper pacifiers, antiwear additives, rust and oxidation inhibitors, antifoam agents and other proprietary additives.
This oil is based on an ethylene oxide-type of PAG, which is soluble in water but insoluble in oil. Polyglycols have been used in these applications with great success and have been known for their good viscosity-temperature behavior, resistance to deposit and sludge formation at higher temperatures and their high thermal range.
Since the compressors were installed in 1993, repeated seal and thrust bearing failures have occurred (Table 2). The thrust bearing failures were related to the degradation of the lubricant and the design of the thrust bearing.
Based on process data and oil properties, the second-stage system was more susceptible to hydrocarbon dilution. The first stage should have seen only about one percent dilution, while the second stage could be as high as six percent. The lubricant was usually found to be heavily oxidized and the bearings showed signs of a corrosive environment.
The seals also appeared to have failed in part by lubricant failure. The original mechanical seals were an OEM seal design until a change was made to use a third-party seal for the application. At the time, machinery reliability engineers did not have a thorough understanding of lubricant degradation or the performance of the lubricant.
The OEM recommended that the oil be changed annually under normal operating conditions. Until 1998, documentation did not indicate that the oil was changed on condition or on a routine basis.
Beginning in 1998, the machinery reliability engineers began sampling the lubricants and changing the flood oil based on the condition of the oil. In 2003, the machines were sampled on a 30-day cycle. This sample frequency was chosen because of the strong process interaction.
These samples are taken under fresh air because of the process gases present, which hindered technicians from efficiently taking more samples on a regular basis. A sampling station was installed to allow a sample to be taken without the need for fresh air.
In 1998, a switch from the OEM-recommended lubricant was made primarily due to the high cost of the oil and increased oil change frequency. The new oil selected is similar in base stock and ISO grade (VG 84 cSt at 40°C).
This PAG oil was considerably less expensive and had many of the same physical properties, but lacked many proprietary additives.
A new change interval was established at six to nine months, and was driven by oil condition. The leading indicators used to monitor the condition of the oil are additive levels, acid number (AN), water, viscosity, pH, strong acid number (S-AN) and particle count (Table 3).
The strong acid test (ASTM D664) is used to determine the presence of strong acids. Water and H2S present in this process; if these components are co-mingled and heat is added, then sulfuric acid can form (a strong acid).
One of the characteristics with lube oil analysis is that it is only a snapshot of the oil condition. Between lube samples, the operations group usually adds makeup oil to the reservoir. These changes make the analysis more difficult and cause the sample results to fluctuate. The key is to look at the overall trend.
The analysis history shows that the use of the S-AN test is a good indicator of lubricant condition. AN looks at strong and weak acids, while S-AN looks only at the strong acids.
With an improved test slate and valid historical data points, new information was evaluated. This prompted a decision to take one of the compressors out of service proactively to avoid a catastrophic failure of the thrust bearings.
Vibration, lubrication and performance data indicated that increased wear was occurring. Increasing levels of tin, aluminum and antimony were signs of bearing wear. Casing vibration had increased slightly over time. This compressor had historically never run this long between failures.
Following the changes made to the lubricant brand, oil change frequency and monitoring, the second stage compressor had run without failure for four years. The annual cost savings for the second stage compressor was $30,000 (based on past failure data and standing oil change costs).
This does not take into account the operational downtime costs. Also, flood oil changes are scheduled during a planned shutdown instead of during an unplanned shutdown.
This case study highlights the key benefits of properly selected lubricants and a properly designed and deployed oil analysis program. The lubricants used in modern equipment are highly engineered and blended to extend lubricant life.
Thorough testing and analysis must be conducted to determine which lubricant is best for the application. This includes a holistic analysis of the process, temperatures, pressures and equipment operating conditions.
Technical Editor’s Note:
For a clear presentation of how to adjust data points to account for oil top-ups and losses, please refer to the article entitled “Understanding Time-dependent Limits” by Ashley Mayer.
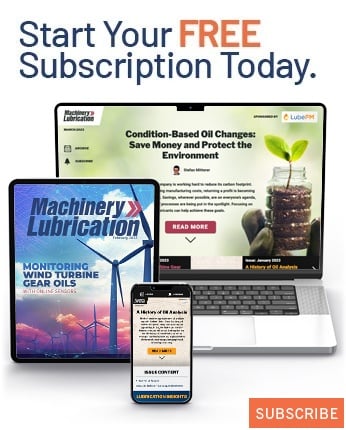