Advanced warning of abnormal wear in high value, high mission critical assets, provides important options otherwise unavailable to decision-makers. With advanced warning of failure, a better understanding of the nature of the problem can be obtained, reducing uncertainty about maintenance decisions and enabling the scheduling of maintenance actions. Secondary damage may be avoidable by identifying and removing the worn parts.
To gain an understanding about the failure, the tribologist analyzes the wear particles generated during the wear process. Oil samples drawn from critical assets equipped with 3 micron absolute filtration (fine filtration) are not useful for wear particle analysis, because the particles have been removed by the fine filter.
While fine filters effectively extend the life of assets, they leave little evidence for the analyst who seeks to determine how far life is being extended. The next generation of wear debris analysis will focus on uncovering the treasure of data buried inside the filter.
Recent advances in machinery monitoring technology have demonstrated the ability to forecast wear related failures well in advance of conventional techniques. The method involves removing suspended particles from the circulating oil and analyzing their constituent chemical elements by x-ray fluorescence (XRF) spectroscopy.
The debris deposited in the filters can reveal the machine's state of health and condition. Conventionally, this information is lost when the filter is discarded. Recent findings from a study of F404 turbine engines in operational F/A-18 aircraft are presented in this article.
![]() |
Figure 1
|
What is XRF Spectroscopy?
In many ways, XRF spectroscopy is similar to atomic emission spectroscopy (AES) which has been commonly used in oil analysis for decades. Both techniques require the excitation of atoms followed by an analysis of the emitted light (UV-visible or x-rays). The rotrode AES method, however, excites the outer electron shells of the atoms using an electrical discharge to create a plasma, causing thermal emission, like the extreme temperatures of an argon plasma torch.
As the atoms return to the normal state, the excess energy is emitted as light. Each element emits light at different frequencies on the electromagnetic spectrum. The amount of light emitted at a given frequency corresponds to the concentration of the element present in the sample.
Conceptually, XRF works in the same way. The difference is that XRF excites the atoms with a bombardment of X-rays. In return, the atoms emit x-rays characteristic of the chemical element at an amplitude that corresponds to the mass of the chemical element in the sample. XRF spectrometers are commonly calibrated to report the concentrations of the reported elements present in parts per million (ppm).
Commercial XRF spectrometers, like television sets and computer monitors, are designed to be operated safely without any requirement for radiation certification of the operator, although familiarization instruction should be provided by the Original Equipment Manufacturers (OEM). The x-rays emitted by the x-ray tube within the spectrometer are extinguished when electrical power is removed.
The infrequent maintenance required by the instrument itself is best performed under service contract. The instruments themselves are robust, require little in the way of alignment, and are easily calibrated (see Figure 1).
XRF involves the excitation of electrons in the inner shells of the atom, nearer the nucleus. AES excites the electrons in the outer shell, which results in the emission of visible light. In a rotrode AES spectrometer, the particles are excited by a plasma generated by an electrical arc in a process which is limited to measuring particles ~<10 micron in size.
However, the inner shell excitation which occurs in an XRF spectrometer requires no arc or plasma, and results in high energy X-ray emissions. XRF is capable of measuring fine particles as well as plate metal samples. It is, however, limited by the depth from which x-rays can exit the sample material.
In the case of plate metal, a sample one-half inch thick will yield the same results as a thicker sample. This leads to a particle size effect, despite which XRF still produces large signals for large particles and small signals for small particles.
In addition to measuring the presence of dissolved metals and organometallics, XRF has been applied to measuring suspended particles in lubricating oils. On-line XRF sensors were developed in the 1970s with the intention of measuring iron concentrations in turbine engines.
But, the instrumentation available in those years was found to be unsuitable for use on operating engines. Several studies report the superiority of suspended particles measured off-line by XRF over atomic spectroscopy in the detection of failure modes involving large particles. In a study of Sea King helicopters, researchers reported that XRF warned of impending failure one sampling period earlier than atomic spectroscopy.
Others have improved the use of XRF by separating the particles from the oil on a membrane patch for analysis. By doing so, x-ray scattering and absorption effects caused by the oil are eliminated and the sample is concentrated, improving the test's sensitivity. In one study, researchers were able to detect wear rates of a single bearing, and observed a 100-fold increase in the generation of bearing wear when a load was applied.
In all the examples of the application of XRF described above, the only particles available for analysis were those circulating in the oil or released to the oil just before sampling. With the fine filtration used in today's critical machinery, the particles that could provide insight about a machine's condition are being captured by the filter and are no longer present in oil samples, and therefore are unavailable to the analyst.
The valuable information is being discarded along with the spent filter element.
While the use of fine filtration clearly extends the operating life of machinery, up until now it is not been clear how long the life is being extended for any given machine. This results in schedule-based maintenance instead of the preferred condition-based maintenance.
However, if the wealth of information stored in the filters could be successfully accessed and analyzed, considerable insight into the machine's health can be achieved. The capture of that information is the focus of the JOAP-TSC study discussed below.
The JOAP-TSC Study of F404 Filters
The Joint Oil Analysis Program Technical Support Center (JOAP-TSC), a technical support function within the U.S. Department of Defense (DoD), undertook a research project to analyze the debris held in 189 filter canisters from F404 engines on F/A-18 aircraft. The study was conducted according to the following procedure:
• Mechanics pulled filters from the engines (normal interval of 200 operating hours), marked the filters and submitted them to JOAP-TSC for analysis.
• Particles were recovered from each filter by immersing the filter in an ultrasonic bath for five minutes.
• The particles were collected on a membrane filter patch and fixed in place with a thin polymer wash for analysis.
• The membrane patches were analyzed for 18 elements simultaneously with a commercially available XRF spectrometer (Spectrace 6000).
• The values reported by the XRF were recorded in a database.
• The data for each individual element was assigned a severity index value from 1 to 5. Level 5 corresponds to higher levels of metal production.
• The results were compared with the metallurgy of the engine components using a decision tree to identify the engine module containing the failed component.
• The findings at the module level were compared to corresponding inspection findings for the aircraft as recorded in the Aircraft Engine Maintenance System (AEMS) database.
Traditional wear particle analysis is employed to provide critical failure warning; XRF monitoring also serves this function. The F/A-18 mechanics recorded which engines had failed due to oil-wetted parts. In every case, filters from these engines displayed elevated levels of iron, nickel and titanium, the elements found to be major indicators of overall health in this engine type.
Other elements provide specific information in the analysis process. Table 1 illustrates that over 60% of the filters from failed engines were classified as Level 3 or above.
![]() |
Table 1 - Identifies the percent of normally operating, recently failed and high operating time machines operating at each level of severity according to the wear index.
|
A wear monitoring device should also be capable of identifying a normally operating machine. Table 1 illustrates that, in 85% of the cases, normal engines (so identified by the mechanics) had low levels (Level 1) of metal in their filters. It should be noted that none of the failed engines showed up with Level 1 for the major metals. Thus, the Level 1 indication from the XRF monitor is useful as a health monitor.
The technique also effectively detects the presence of dirt (silicon) in normally operating machines. Left unattended, dirt expedites the on-set of wear and failure. In addition, XRF detects the particles produced by the corrosion of components such as housings.
Table 1 also reports the data recovered from engines which had undergone scheduled replacement of oil-wetted parts due to high operating time. In the absence of effective condition monitoring, replacement schedules must be sufficiently conservative to meet system reliability requirements. The high operating time data clearly indicates that a significant fraction of the high time engines were indeed experiencing advanced wear, with 14.1% generating Level 3 and Level 4 concentrations of the major metals.
However, nearly half of the engines receiving component replacements were at Level 1, suggesting that many of the components were replaced unnecessarily. As a health monitor, XRF can assist in determining the suitability of maintenance deferrals on specific machines.
![]() |
Table 2 - Describes the by-element warning provided along with the corresponding level of severity.
|
Another interesting finding in this study is the amount of forewarning provided before failure (Table 2). A few machines submitted more than one filter prior to a recorded failure. The analysis of these filters provides interesting insight about what might have been detected, had the program been operational.
Warning times in the hundreds of hours were available from the XRF results. The warning time provided by the signaling element depends on the metallurgy of the failing component and the wear mode.
The data from this study allow us to make the following conclusions about XRF filter debris analysis:
• Machine wear is identified at the onset of impending failure, allowing a significant advance warning for planning and action.
• Normal operation can be readily identified.
• Destructive contaminants can be identified to enable corrective action.
• The difference between normal and abnormal operation is sufficient to drive condition-based verification of component replacement schedules on a machine-by-machine basis, avoiding wasteful maintenance and reducing the likelihood that at-risk equipment is operating under the assumption it is healthy.
Implications to Maintenance Management and Future Directions for XRF.
This demonstration suggests that, by employing a new procedure for XRF spectroscopy, better maintenance and operations scheduling decisions are within grasp. Machines that are experiencing unexpected wear can be identified for maintenance in advance of a failure that results in downtime or creates safety or environmental hazards.
Conversely, machines due for a scheduled component replacement under a conventional maintenance program can be kept in service until such time that conditions suggest that maintenance is warranted, avoiding unnecessary maintenance expense and the introduction of problems during the course of performing intrusive maintenance actions. At the bottom line, maintenance will operate more efficiently and effectively.
Likewise, operations will be served by reliable equipment, allowing availability objectives to be met.
Presently, the sample handling process described in this paper is manual, typically performed in a laboratory. The XRF instrumentation itself is programmed to carry out its measurement and data reduction tasks semi-automatically. There are numerous benefits to bringing this technique on-site, or even on-line for critical systems. Low volume programs can utilize more labor-intensive manual systems.
On-line systems, not yet available, would offer the advantage of continuous monitoring and protection. Of course, to identify an abnormal situation, the normal state must be known. And, to identify a failure, a knowledge of the machine's failure profile is required. A high quality monitor like XRF filter debris analysis, together with a well-characterized machine profile, will enable the best assessments of remaining useful life. These conclusions and inferences are enhanced when the profile data is drawn from the full range of actual operating and environmental conditions.
Conclusion. XRF filter debris analysis is an effective technology for analyzing particulate contaminants in oil lubrication systems. It will enhance management's ability to more effectively plan maintenance and operations. XRF complements current trends toward fine filtration, longer life cycles, lower labor costs and reduction of unnecessary replacements, while offering a path toward affordable readiness through condition-based maintenance.
The XRF debris analysis method described herein is widely applicable to a variety of rotating and reciprocating machinery and fluids in both military and civilian applications.
XRF Filter Debris Analysis Benefits:
• XRF filter debris analysis fills an important gap left by atomic emission spectroscopy and analytical ferrography/patch microscopy techniques.
• It recovers the data formerly lost by the use of fine filtration, while retaining the extended machine life offered by the fine filters.
• XRF analysis of the debris in the filter provides a thumbprint of what has happened since the last filter change.
• The deposition of particles onto a membrane patch allows XRF to quantify the elemental particle debris without interference from the oil.
• The XRF analysis of particles deposited on a patch or a slide ferrogram adds an objective component to the normally subjective analysis of particle size and morphology.
• XRF analysis of debris from filters yields long lead times prior to the onset of failure.
REFERENCES:
Humphrey, Gary R., "Characterization of Debris from F404 Engine Oil Filters by Energy Dispersive X-Ray Fluorescence", Joint Oil Analysis Program Technical Support Center, JOAP-TSC-TR-96-02, June 1996.
Whitlock, R., Churchill D. and G. Humphrey "The Path to Affordable Long Term Failure Warning: The XRF-Wear Monitor," Proceedings of the JOAP International Cindition Monitoring Conference, April 19-24, 1998, Mobile, Alabama.
Whitlock, R., Humphrey, G. and D. Churchil "Filter Debris
Analysis Using Commercial Equipment Today," Lubrication Engineering (forthcoming).
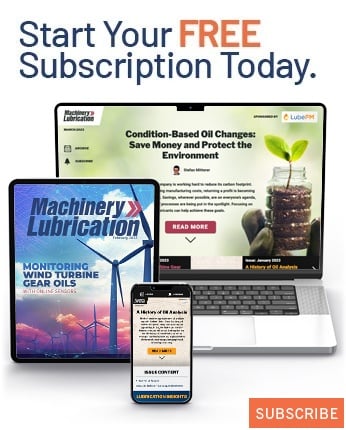