The ability to trend and evaluate data is essential in the proper use of oil analysis technology.
By definition, the term “trend” means to show a tendency. Typically this means either a tendency to increase, decrease, or remain the same or steady. A version not commonly discussed and one I’d like to focus on, is the repeating trend. A repeating trend can be defined as having a tendency to repeat a previously recorded trend.
An oil analysis report typically includes the current sample results and information regarding the equipment being sampled, the lube used, and any other information provided at the time of sampling. Some reports include historical information ranging from the previous sample to as far back as five or six samples.
A common misconception is that the data relayed on an oil analysis report is all that is needed to make proper decisions. This could not be further from the truth.
A high-quality evaluation takes into account the entire data history for a specific component, including the data history for a component that may have failed performing the same function for the same equipment train (such as a centrifugal pump replaced with a new/rebuilt centrifugal pump).
This will help to spot a repeating trend and allow for accurate evaluations of the most recent data. Additionally, more knowledge can be gained concerning how to evaluate other similar components that may run under similar conditions.
Table 1. Data Analysis Indicating
Contamination
Consider the data found in Table 1. The iron and silicon made an initial increase in October 2003. The following scheduled quarterly sample confirms this finding with another increase in the two elements. At this point, a recommendation was made to utilize portable filtration to remove the excessive wear and external contamination.
Additionally, it was recommended to check for possible sources of external contamination, particularly around seals and breathers, and to make the appropriate repairs as needed. The following scheduled samples indicated a condition that was obviously getting worse. Had this level of contamination and wear been allowed to continue, catastrophic failure would have resulted.
The recommendations were executed. The lubricant was filtered with media rated at Beta(6)³100. The open vent was replaced with a desiccant-style breather to arrest any external contamination. The areas around the seals were kept free of process debris buildup.
As time passed, the site received a new maintenance manager and a new reliability engineer. The oil analysis program was able to continue with normal regularity.
However, in an effort to reduce maintenance costs, it was decided that the use of desiccant breathers was not necessary with the addition of route-based filtering. As seen in Table 2, the equipment sampled achieved a normal level of wear after the previous maintenance was performed.
Table 2. Data Analysis Indicating a
Normal Wear Rate (with the Exception
of January 2006)
What plant personnel did not realize was that the oil report they were using as their justification included data only from October 2004 through July 2005. With the regular inspection route for oil levels performed on a weekly basis, the desiccant breather was removed shortly before the October 2005 sample.
If the entire oil analysis history had been considered on-site before this decision was made, the October sample likely would not have resulted in a cautionary alarm. Because the January 2006 sample confirmed a contamination and adverse wear condition, the analyst’s recommendation was nearly identical to the previous maintenance performed in 2004.
Upon comparison, the data can be seen as a repeating trend in Figure 1.
Figure 1. Example of a Repeated Trend
When a repeating trend is spotted, the situation can be arrested by learning what maintenance was previously performed. At this point, it can be determined whether those procedures were adequate or if other steps should be taken. In this case, the procedures taken during the first adverse condition were adequate to control the adverse condition.
These procedures can quickly be implemented to prevent this component’s condition from deteriorating. It’s important to realize that the data collected from an analyst is a helpful tool if the appropriate information is provided.
Whether an oil report is supplied with just the most recent sample data or with all available historical data, it is important that the evaluation should consider all data available for the equipment.
Additionally, search for data in graphical form. Many laboratories will include graphs on the front or back of the oil reports. While the tabular data is likely to be limited in timeframe, the graphical data should include all historical sample data. These graphs can help in properly identifying repeating trends.
Read more on oil analysis best practices:
Is Oil Analysis a Waste of Time?
Statistical Techniques to Simplify Oil Analysis Data
How to Interpret Oil Analysis Reports
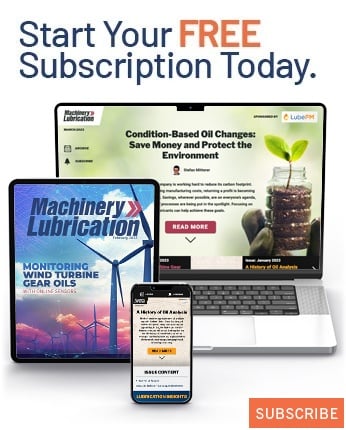