Utilizing predictive technologies is a common maintenance practice today. While some technologies are suited more for a particular application than others, there are applications in which the criticality of a component may warrant the use of multiple technologies to maximize the ability to catch a potential adverse condition.
When a program uses multiple technologies, the collaboration of these technologies is essential to properly identify potential failures.
Figure 1 shows an example of the different results that can be obtained by using multiple technologies compared to the original technology based solely on oil data.
![]() |
![]() |
![]() |
In this example, there is a sample interval of nearly three months. In the sample dated 11/30/05, the ISO cleanliness level dropped dramatically and is near the target level of 16/13. The iron, however, increased over this time. The overall rate of change in the iron was similar to the February to May interval. Regarding the 90ppm amount, the iron was still below the initial alarm value as well as below what had historically been observed in this gearbox (Figure 2), the results may not appear alarming to the untrained eye.
Figure 2. Gearbox Alarms
When viewing oil analysis data, one aspect to consider is the maintenance performed between samples. When looking at the recent maintenance on the gearbox, it shows the lubricant was changed prior to the 9/8/05 sample and offline filtration was performed prior to the 11/30/05 sample. The lubricant change explains the significant drop in the iron value (108 ppm to 50 ppm) and the improvement in cleanliness level. The trouble is that after offline filtration occurred, the cleanliness level improved even more, yet the iron value experienced a rate of increase equal to (even a bit higher than) that of the previous quarterly sample.
Given this information, vibration readings were brought in for evaluation. Figure 3 shows the changes that occurred from April 2005 until October 2005. The values prior to April 2005 are consistent with the readings seen for April, May and June. The increases in the area are from about 35 times running speed to 70 times running speed.
Figure 3. Changes in Vibrations
Upon seeing this data, it was assumed that while the filtering process appeared to have improved the overall cleanliness, a severe wear condition was taking place in the gearbox. Consider for a moment what the iron value may have been if the offline filtration had not occurred.
The next step in the clarification process was to order additional testing for wear confirmation. In this case, analytical ferrography was requested with the expectation of seeing bearing fatigue and abrasive type wear. Figure 4 shows the types of particles found in the analytical ferrography examination.
Figure 4. Wear Particles Found in Ferropraphy Exam
The laboratory comments for the slide examination were:
Moderate amount of ferrous rubbing wear less than 10 µm. Moderate amount of red and black oxide up to 35 µm. Moderate amount of abrasives (silica/dirt and environmental contaminants). Minor amount of metallic spheres less than 8 µm and spalling wear (fatigue) from 10 to 30 µm.
The fatigue particles noted in the analytical ferrography report confirm the evaluations performed via vibration analysis and the standard oil analysis test slate. The presence of red oxides indicates the likelihood of rust formation due to a previous presence of water in the gearcase reservoir.
With all of this data, it was with 100 percent confidence that the client understood the situation of the gearbox. This defect was found at an early stage, giving the client ample time to make arrangements for the replacement of the gearbox at a time that reduced overall production impact.
The severity of this situation and the criticality of the gearbox to the operation resulted in the decision to bring in other technologies to monitor the gearbox during the failure process. Currently, this gearbox is also being monitored with ultrasound and thermography. Both technologies established an initial baseline after the failure was identified. The data from these technologies helps identify the various stages of failure as well as enables one to observe sudden changes. The vibration analysis interval has been moved from monthly to biweekly with oil sampling going from a quarterly to monthly basis.
When asked to summarize the level of satisfaction with using multiple technologies, our client had this to say:
“Multitechnology asset health monitoring has provided us with the information to pinpoint and confirm asset defects. In this case, we detected a problem even before the asset was in alarm using vibration analysis. Ultrasound and thermography confirmed the defect. Tribology not only confirmed the defect, it has closely monitored the progression and given us the information needed to make a sound business decision.”
Think of your predictive program as an old classic car sitting in the garage. If it’s just sitting there in pieces waiting to be put together, then there is nothing to brag about. On the other hand, once all of the right parts are acquired and the car is put together and running smoothly, you can truly reap the benefits of your labor. You’ll find success once you’re traveling down the road.
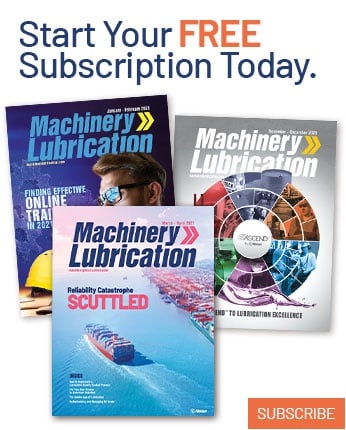