Northrup Grumman - Newport News (NGNN) was asked to perform equipment modernization, which involves modifications to the variable restrictor manifolds on SEAWOLF Class submarines.
The trim and drain engine room control valve manifold was removed from USS SEAWOLF for modifications to meet the equipment modernization requirements. The task involved removing the valve manifold, reworking it to meet the requirements and installing the modified manifold on USS CONNECTICUT.
Figure 1. Valve Interface Ports C3, C2
When NGNN and Sargent Controls received the manifold, a visual inspection revealed extensive damage to ports C2 and C3. NGNN and Sargent Controls recommended to Naval Sea Systems Command (NAVSEA) that the manifold be scrapped and replaced for USS CONNECTICUT. The scrapped manifold was forwarded to the Naval Surface Warfare Center, Carderock Division (NSWCCD), NSWCCD for failure analysis.
Visual Inspection
The subject manifold controls internal hydraulic system actuators TD-12 and TD-16. Examination of the valve interface port revealed extensive damage to ports C2 and C3. Figure 1 shows ports C2 and C3. Figure 2 shows a closer view of ports C2 and C3. The lower portion of valve interface ports C2 and C3 contained extensive damage.
The damaged surface appears sponge-like and is typical of a corroded surface. An interface between sound metal and damaged metal runs parallel to the horizontal axis of the manifold. The sponge-like appearance stops at the hydraulic fluid passage. This structure was found only in the lowest portion of the fluid system in the as-installed configuration.
Figure 2. Valve Interface Ports C3 and C2
The manifold was sectioned horizontally, following the centerline of the hydraulic fluid passages (Figure 3). The hydraulic fluid passages of the bottom side of C2 and C3 contained patches of corrosion similar to the damage seen on the valve interface ports as seen in Figure 4.
A dark green substance was present over the bottom surface of these passages. The C3 passage contained a large amount of this substance. The upper halves of the hydraulic fluid passages in the manifold are clean and free of corrosion.
Figure 3. Cross-section of HP-576 Manifold
Figure 4. Bottom Side
of HydraulicFluid
Passages from Valve
Interface Port C3
Inlet Showing Corrosion
Analysis
The manifold is to be manufactured from 6061 aluminum in accordance with QQ-A-200/8, QQ-A-250/11, or MIL-A-22771. A chemical analysis was performed on the manifold material and the results determined that the manifold meets these requirements.
Mechanical testing was performed on the manifold material to verify compliance with the standards mentioned above. The results of the mechanical test determined that the manifold meets the mechanical property requirements.
Valve interface port C2 was examined in a scanning electron microscope (SEM). Figure 5 shows the surface of the degraded area at 50X magnification. Energy dispersive X-ray analysis (EDXA) of this section is shown in Figure 6.
EDXA reveals the presence of aluminum and silicon in the base metal; and sodium, chlorine and potassium which indicate seawater contamination. Sulfur and phosphorous are also present on the corrosion surface. While sulfur and phosphorous are present in seawater, the quantity of sulfur and phosphorous exceed the expected level when compared to other seawater contaminants.
Figure 5. SEM Micrograph of Valve Inlet Cross-section (50X).
Red Box Indicates Area Where EDXA Spectra of Figure 6
was Tested.
Figure 6. EDXA Analysis of Valve Inlet Surface of the Area
in the Red Box of Figure 5
The surface of the pit seen in Figure 5 was magnified to 1,000X. Figure 7 shows the surface of the pit at 1,000X magnification. In comparing the surfaces of Figure 5 with Figure 7, the higher magnification reveals a rough surface, filled with pockmarks. EDXA of this magnified region reveals the presence of only aluminum and phosphorous (Figure 8).
Figure 7. SEM Micrograph of Valve
Inlet Cross-section (1,000X)
Figure 8. EDXA Analysis of Valve Inlet
Surface of the Area in the Red Box
EDXA was performed on the dark green substance present in the bottom of the hydraulic fluid passage. Results of the EDXA are shown in Figure 9. The dark green residue consists of aluminum and phosphorus, with small traces of sulfur.
Figure 9. EDXA Analysis of Dark Green Substance
from Hydraulic Fluid Passages
A summary of analysis findings is as follows:
-
C2 and C3 valve inlet port surfaces are corroded.
-
There is a definite interface between the corroded and noncorroded material. It runs horizontally, with the corroded region beginning at the bottom of the valve inlet port surfaces and extending upward to the hydraulic fluid passage.
-
The corroded surface extends along the bottom of the hydraulic fluid passage.
-
A dark green substance is also present along the bottom of the hydraulic fluid passage. EDXA of the dark green substance shows that it is composed of aluminum and phosphorous with small traces of sulfur.
-
EDXA of the corroded surface shows unaccountable sulfur and phosphorous.
Failure
The conclusion, based on the appearance of the degraded surfaces of the C2 and C3 valve inlet ports, indicated the surface was experiencing localized corrosion. It must be noted, however, that 6061 aluminum does not generally corrode in the presence of internal submarine hydraulic fluids. Additionally the presence of an aluminum-phosphorous corrosion product is not consistent with normal aluminum alloy corrosion mechanisms.
A significant observation is the horizontal interface between the degraded aluminum and the sound aluminum. This interface orientation is noteworthy because it stops near the bottom of the hydraulic fluid passages on the vertical surface.
The degraded material continues horizontally along the bottom of the hydraulic fluid passage. Based on the orientation and location of the degraded material, it is concluded that a fluid interface exists between the hydraulic fluid and a foreign fluid.
NAVSEA determined that actuator assessments were performed on USS SEAWOLF prior to removing the manifold from service.
TD-16 operates off of valve interface ports C3 and C2. TD-16 was found to have degraded pinion T-seals. NAVSEA identified two scenarios: one where seawater could leak through the pinion T-seals and into the hydraulic fluid, and other where fresh water could enter the hydraulic system if a leak occurs in the propulsion fresh water cooling system.
Both of these scenarios provide an explanation of how a foreign fluid could enter the hydraulic system.
Figures 8 and 9 show the presence of phosphorous and sulfur in the degraded areas. Figure 6, however, also shows small amounts of sodium and chlorine in the corrosion product. This indicates the fluid contaminant was likely seawater or a combination of seawater and fresh water, as these elements would not be present if the corrosion was a result of fresh water alone.
Due to its higher density, seawater would displace itself to, and occupy, the lower portions of the hydraulic system. C2 and C3 ports are the low points between the manifold and the TD-16 actuator.
Therefore, the conclusion implies that seawater contamination of the hydraulic fluid settled in the C2 and C3 ports of the manifold (Figure 10). When the seawater contamination levels rose to the extent that the port cavity could no longer hold the foreign fluid, it spilled into the manifold’s hydraulic fluid passage. This scenario provides a plausible explanation as to the location of the defects in the manifold.
Figure 10. A Proposed Failure Scenario
A dark green substance was found on the surface of the manifold’s hydraulic fluid passage. EDXA of the substance (Figure 9) shows that the substance is composed primarily of phosphorous and sulfur. Figures 6 and 8 also show high levels of phosphorous and sulfur in the degraded area. The presence of phosphorous and sulfur, without a reasonable alternative source, are indications of a process known as microbiologically influenced corrosion (MIC).
Gregory Kobrin, in reference No. 1, claims that MIC is localized. This is evident in the locations where corrosion has and has not occurred. Kobrin further states that a covering deposit almost always accompanies MIC cases.
This is evident in the dark green substance located in the manifold hydraulic passages. Finally, he states that sulfate reducing bacteria (SRB) use phosphorous to store energy, and that SRBs break down sulfates into sulfides. Internal hydraulic fluid contains an additive package to increase the fluid’s effectivity, prevent fluid foaming and increase the healthy life of the hydraulic fluid.
These packages are rich in phosphorous and contain sulfinates. SRBs will break down sulfinates into sulfides with the same vigor as they break down sulfates. These sulfides tend to initiate corrosion.
Therefore, the degraded regions will tend to show high levels of both phosphorous (from the stored energy) and sulfur. Both are present in Figures 6, 8 and 9. Based on this information, it is likely that the cause of failure of the manifold is MIC.
Unfortunately, it is difficult to be certain that MIC is the root cause of failure. Without isolating and positively identifying the microorganisms in the system, this conclusion is based on secondary evidence that supports MIC. Furthermore, 6061 aluminum is known to pit when exposed to seawater. Although seawater pitting of the aluminum does not support the evidence presented herein, it cannot be eliminated as a root cause or contributor to failure.
Corrective Actions
MIC degradation is the result of microbiological growth in the hydraulic system. This growth lives at the water-hydraulic fluid interface and exudes a by-product that is highly corrosive to the base material of the manifold.
To eliminate MIC, the microbiological growth must be eliminated. To eliminate the growth, one must either eliminate the water-hydraulic fluid interface by preventing water from entering the system, or use a biocide in the hydraulic fluid to prohibit biological growth when the water-hydraulic fluid interface is present. In order to eliminate the seawater pitting of the aluminum, seawater must be removed from the system.
While it is encouraged that water be eliminated from the hydraulic system, practical execution of this recommendation is almost impossible. NSWCCD recommends that SEAWOLF class maintenance requirements cards (MRC) be modified to require semiannual hydraulic samples to be taken from ships service and external hydraulic systems for additive testing and water monitoring. This is similar to current OHIO class and LOS ANGELES class requirements.
NSWCCD recommends that the in-service fleet support office develop a hydraulic fluid-friendly biocide to eliminate MIC degradation of hydraulic system components. Reference No. 1 discusses the merits of biocide use in hydraulic fluids.
The biocide could be an additive to the hydraulic fluid or flushed through the system during availabilities. Either solution would need to assure the biocide is compatible with the materials in the hydraulics system. By utilizing a biocide in the hydraulic system, future cases of MIC can be minimized.
Conclusions
NSWCCD has determined the hydraulic manifold has most likely degraded from microbiologically influenced corrosion. Seawater pitting of the aluminum may also contribute to the failure.
The degradation on the manifold is the result of seawater penetration into the hydraulic fluid. The microbiological growth resided at the seawater-hydraulic fluid interface. NSWCCD recommends that the in-service fleet support office develop a hydraulic fluid biocide additive or implement biocide flush treatments to known contaminated systems to prevent future occurrences of this degradation.
Editor’s Note:
NAVSEA Headquarters (author Charles Boyle) recognizes the invaluable assistance and noteworthy technical expertise of the engineering staff of NSWC-CD Philadelphia in the preparation of this article on the effects of microbiologically influenced corrosion in hydraulic components.
Reference
- Kobrin, Gregory. A Practical Manual on Microbiologically Influenced Corrosion. NACE International. Chapter 5. 1993.
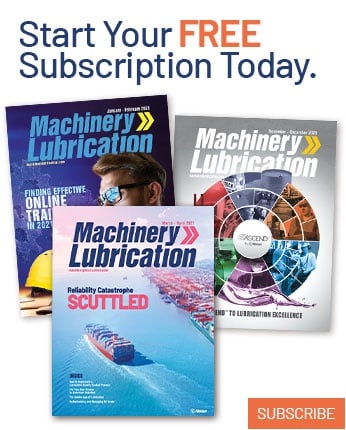