Throughout my employment with Noria, I have presented many oil analysis training courses. Typically during my courses - and this is something I welcome - an attendee will approach me with a stack of oil-analysis reports from his laboratory needing help on how to interpret them.
“How are they testing for water?” “Why aren’t they doing ferrous density on the gearbox?” “What method are they using for acid number?” These are just some of the questions that usually come up.
How are the Tests Conducted?
As far as the question of “why aren’t I getting such-and-such test?” is concerned, that’s because either the laboratory cannot do it, or more likely, you haven’t requested that the laboratory actually do it. It’s the user’s responsibility to determine which tests are needed, which is the primary reason oil analysis training is needed. And regarding how the tests are performed, that’s anybody’s guess.
I’ve studied many reports for customers, and the simple fact is that no one at the plant knows exactly how his tests are being performed. Looking at their reports, I often don’t find that information either.
Quality of Data
One of the concerns with oil analysis results is in the quality of the data. Many oil analysis users are not aware that their test results can vary significantly depending on which laboratory is performing the test, and which test method they are using.
Consider the moisture content test, for example. Reports can list the conclusions as a yes/no, as a percentage, or in parts per million (ppm). To obtain the yes/no result, either the crackle test or Fourier transform infrared (FTIR) was likely used. For the outcome to be a percentage, the test could possibly be FTIR or a derivation of the calcium-hydride test.
It might also have been a Dean and Stark distillation. For the results to be shown in ppm, Karl Fischer was likely used, although it could also be a calcium hydride test. If it was Karl Fischer, it’s possible the test could have been coulometric or volumetric. Was co-distillation used? In many cases, co-distillation should have been used, but probably wasn’t.
These are vital questions that need to be answered. One cannot expect to make hair-trigger decisions if the quality of data is insufficient. Unfortunately, many oil analysis users are not aware of the standard of their analyses or their repeatability. It is often assumed that they are good. Sometimes that assumption is valid, other times it is not.
Testing Procedures
The time is overdue for the oil analysis industry to develop specific standard test procedures for used oils. Given the absence of standards, what test procedures are currently being used? Most test procedures in the industry originate in the lubricant manufacturing industry, and were designed as quality-control tests for the production of new lubricants.
These tests are capable of subpercent precision. For example, the ASTM D445, the standard test for the kinematic viscosity of transparent and opaque liquids (and the calculation of dynamic viscosity), has a repeatability of 0.11 percent. For used oil analysis, it does not matter if the oil is 32.000 cSt or 32.035 cSt in most cases.
The bath of an ASTM D445 test (for 40°C) must be maintained at 40°C ± 0.02°C. This is a close tolerance which requires sophisticated equipment to maintain. As a result, a true ASTM D445 is costly.
So, what happens next? The test gets modified, not with the objective of reducing the accuracy, but with making the test cost-effective for oil analysis. The problem, however, is that all laboratories modify the test individually. As a result, oil analysis users cannot be sure of how closely their test results compare to the true D445 standard.
It is interesting to note that until recently, the ASTM D445 method ascribed the applicability of its test to base oils and formulated oils, but not to “previously-used formulated oils”. Fortunately, this has since changed. But because this test was not originally designed for used-oil analysis, it was a good reason for used-oil analysis laboratories to modify it, and that is exactly what has happened.
And kinematic viscosity is just one example of the vital used-oil analysis tests needed.
Final Thoughts
I have a commercial oil analysis laboratory background; therefore, I have some understanding of the issues at stake.
As for standardizing commercial labs, there are some concerns, which include: industry standards could restrict them to a lesser degree of service than they want to provide customers; industry standards could restrict them to a lesser degree of flexibility in determining the appropriateness of tests; or standards could enforce a degree of industry compatibility they are neither willing nor able to provide, likely for cost reasons.
These are all valid concerns, yet I believe these hurdles have been faced in the evolution of other industries. The airline industry confronted it and the development of that theory led to reliability-centered maintenance (RCM).
Here’s the good news: in another article in this issue of Practicing Oil Analysis, Bryan Johnson of APSC – Palo Verde shares some exiting news about the development of standards in our industry. The CS96 In-Service Lubricant Testing and Condition Monitoring Services Industry Support is a subcommittee of ASTM D02, and is making great progress in developing the standards our industry needs. If you have something to contribute, please get involved!
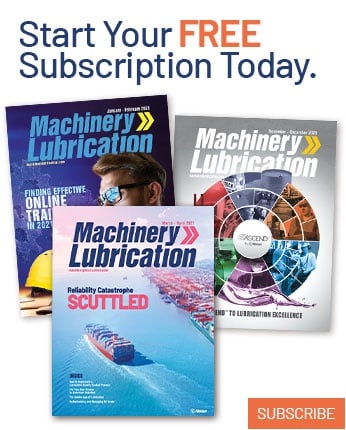