Typically, there are two problems that can occur with poor sampling: either nonexistent problems are introduced by contaminating the sample while it is being extracted or a genuine problem is missed by not taking a representative sample.
I call this the Fighter Jet Syndrome. The former case is the Mirage, you think it’s there but it’s not. The latter case is the Spirit, you think it’s not there, but it is.
The subject of oil sampling is always a topical subject, In my experience, lubrication teams usually grasp the importance of good oil sampling, but are not exactly sure how to address the specifics. The good news is that instituting a quality oil sampling program in a plant is generally a relatively inexpensive exercise with high, short-term paybacks.
Figure 1. Drain Port Modification for Sample Valve
Sampling Procedures
There are three ways a sample can be extracted from an oil-lubricated component: through the drain port; using a drop-tube with a vacuum pump; and via a dedicated sampling point.
The latter option is preferred. It is not to say that one can’t get a representative sample from a drain port or by using a drop tube, but there are so many things that can go wrong with either of these methods that the chances of getting a good sample are considerably reduced. Drain-port sampling and drop-tube sampling are not considered best practice.
When managing an oil sampling program, it is necessary to remove potential sources of interference as much as possible. After all, it’s the manager who must deal with the consequences of inaccurate sampling, not the person who took the sample. The goal of an oil sampling improvement program should be to eliminate uncertainty from your oil sampling, and by implication that means eliminating drain-port and drop-tube sampling from the plant.
Here’s a good place to start improving sampling practices. Every time the oil is changed in a component, replace the drain plug with a sample valve incorporated with a static sampling tube (also known as a pitot tube).
Chances are if oil analysis has not been performed on the component, time-based oil changes are being performed on a relatively short interval, so the process of converting components to static-sampling-tube sample ports will take a couple of years at worst. Actually, an even better way of modifying the drain port is to replace the drain plug with a nipple-tee combination.
The nipple is threaded between the run of the tee and the component so that when the tee is fitted, the run of the tee aims straight into the component. Fit the sample valve into the other end of the run so the pitot tube enters the component without contacting static or dynamic components in the compartment.
Fit the original drain plug into the empty port (the branch) of the tee fit the original drain plug, or, even better, install a quick-connect fitting to aid the attachment of a portable filter cart. Such drain-port modification fittings can be preassembled, and fitment is as easy as unscrewing the drain plug and replacing with the modification.
Other Options
A drain port is not the only place a sample valve can be installed. Often there is an extra port on the component below the normal oil level, where a sample valve can be installed. It can even be fitted into the level-plug port with a pitot tube that is bent to protrude below the oil level. Of course, that assumes that a method of checking the oil level, other than opening the level plug, is available.
Mistakes
A common mistake is taking a sample from the oil reservoir in hydraulic and circulating systems. This is probably the second-worst place from which to extract the primary sample, being surpassed in mediocrity only by extracting a sample downstream from the filters. If wear-metal generation rates are needed from a sample, taking a sample from the tank is not best practice.
Wear metal particles get diluted in the tank – a gram of Babbitt metal wiped from a turbine bearing and diluted in 10,000 gallons of oil is undetectable. But if a sample is obtained from the drain lines before they empty into the tank, the concentration of wear metal is going to be much higher, thus abnormal wear can be expected to be detected sooner.
Always be Consistent
Another issue with sampling is the importance of consistency. It is not a good idea to trend sample results taken using different sampling methods. If you don’t believe me, then try this experiment: take a sample via the drain, take another one using a drop tube, and if possible take a third using a dedicated sample port, all simultaneously and from the same component.
Almost certainly you will see quite varying results in sample-point-sensitive parameters such as particle counts, ferrous density and moisture. Having dedicated sample ports enhances consistency from sample to sample.
If you haven’t instituted a world-class oil-sampling program, now is a good time to start. If a sampling program in place, maybe now is the right time to review it for compatibility with reliability goals. Don’t let a poor oil sampling program shoot your oil-analysis program from the sky.
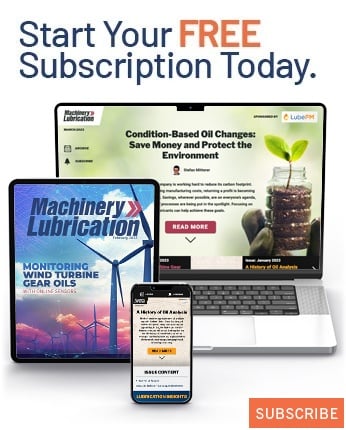