Demand for Jet-Care International’s helicopter engine condition monitoring program is rapidly growing in the United States as manufacturers and operators recognize its potential to diagnose a problem before becoming an expensive maintenance issue.
“Unscheduled engine removals are unwelcome,” said Jet-Care founder and president David Glass. “Even the most advanced power plants are susceptible to wear and erosion. Our value to operators is in being able to identify situations before they become expensive or contribute to operational delays.”
In the past, year Jet-Care has seen an increase in operators and maintenance organizations selecting the company due to its proven quality, expertise and dedication. These include service centers, law enforcement, fire departments, offshore oil and emergency medical services.
Jet-Care is based in Cedar Knolls, New Jersey and has a sister company, Spectro, in the United Kingdom and Switzerland. Together, they are monitoring the health of more than 13,000 engines in more than 72 countries. With a 30-year history in fluid analysis, Jet-Care has an incomparable amount of experience, providing the technology, data quality, timely response and cost effectiveness necessary for today’s competitive engine business environment.
United States Coast Guard Kittyhawk
Partnerships for Success
All three of the company’s laboratories routinely analyze samples from major original equipment manufacturers (OEM) and operators. OEMs such as Honeywell, Turbomeca, Williams International and Pratt and Whitney have given their approval to Jet-Care facilities. Other long-time helicopter clients include CHC Scotia, Bristow, McAlpine Helicopters, Bond Air Services, Bond Offshore, FB Heliservices and The Queens Flight.
Taking Care of Business
Commenting about the Eurocopter Mexico contract, Eduardo Mendoza, Eurocopter Mexico’s quality manager, said “Jet-Care’s software enables us to have a historical knowledge about the aircraft we manage. We receive detailed information via the Jet-Care ECHO program. With it, we can view the results and review the trends for each piece of equipment we monitor. This improves our reactive skills toward our customers better than ever.”
“We provide our customers with more than just numbers and graphs, but analysis borne of an extensive knowledge of helicopters and aircraft engines,” Glass said. “Our experience with both wet chemistry and debris analysis helps our customers efficiently maintain their engines.”
Reporting Software
Operators are taking advantage of Jet-Care’s oil analysis reports through Jet-Care’s Engine Condition Health Online (ECHO™) software. The reporting program allows operators to receive a small data file from Jet-Care by e-mail. Once samples have been analyzed it enables users to review the alert category and results, trend the data. The system offers fast response trending. If concerns are raised from a specific analysis result, Jet-Care immediately warns operators by telephone. Technicians are available 24/7/365 to speak to operators.
Fleet operators have found ECHO useful in comparison studies that allow them to make long-range plans regarding overhaul, maintenance, parts procurement and other planning and purchasing decisions. In addition, a chief engineer responsible for a diversified fleet with aircraft in different locations, for example, can forward graphs and results to key personnel requesting data on an engine’s condition.
Eduardo Mendoza
Contamination Check
Jet-Care’s oil analysis program provides a highly reliable means of checking the metal content and other contamination within the oil system. Jet-Care uses the industry’s most advanced techniques and equipment including scanning electron microscopes (SEM) and inductively coupled plasma (ICP) spectrometers and analyzes down to one part per 100 million.
“Studying turbine engine oil for microscopic metal debris, oxidation and other contaminants allows operators to detect potential problems early,” said Peter Smith, Jet-Care’s head of technical services. “This prevents excessive wear in one subassembly from damaging others.”
He said taking oil samples and trending raw data on a routine basis allows helicopter flight departments not only to save on engine maintenance costs, but also to search for signs of imminent failure, making it possible to schedule aircraft availability around any aircraft on ground (AOG) issues likely to arise.
Smith explained the benefits of rotorcraft engine fluid and chip analyses. “We are constantly looking for changes in the elements of oil that are related to wear, for example, in casings and bearings. Magnesium can accumulate in a casing or titanium in a shaft. We look for hydraulic fluid contamination and fuel in the oil and we check for viscosity. Leaks in a fuel-cooled oil cooler can be found from changes in viscosity. We also look at wear elements in the oil and the physical properties of the oil.”
Smith said chips are basically anything visible. “We might be able to tell customers it’s from the gearbox or the shaft. We can see if the material doesn’t belong in that gearbox and if the customer should be concerned. Sometimes we see debris that has oxidized. That could indicate that it’s debris from an old failure. Because this a nondestructive test that is repeatable, we can inform a customer if there is new damage.”
Editor’s Note:
This article originally appeared in Rotorhub’s Industry News.
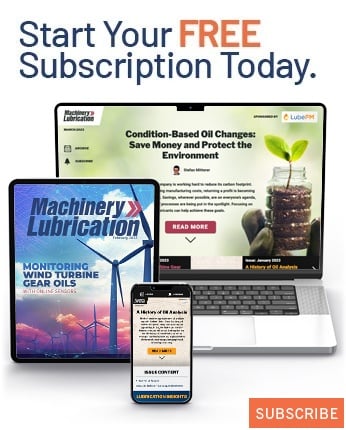