Inspecting new oil deliveries should be an important part of any lubrication program. Many incidents have been reported of customers receiving either the wrong oil, contaminated or degraded oil. The best way to prevent this from happening is to be aware of what could go wrong and inspect and analyze new oil deliveries. The following is an example of an incident that occurred at the Alcoa Mill facility in Lancaster, Pennsylvania.
The Facility
Alcoa is a leading producer of aluminum products for packaging, automotive, aerospace, construction and other markets. It has operating locations in 38 countries and approximately 120,000 employees worldwide.Its revenues were nearly $26.2 billion and Fortune magazine named Alcoa its “Most Admired” metals company.
The Lancaster facility is an aluminum rolling mill that produces mill finish and coated nonheat treatable aluminum coil.
How Well Does Your Oil Meet its Specs?
One of Alcoa’s main mill drive gearboxes was scheduled for an oil change just after an overhaul. The lubricant supplier had determined the appropriate type and grade of oil for the 600-gallon tank to be an AGMA 5, ISO 220 extreme pressure (EP) gear oil.
The oil tank was cleaned and the oil replaced as scheduled. Prior to turning over the gear set, the oil was circulated through a portable filter cart. Upon completion of all gearbox connections, the oil was allowed to circulate through the lubrication system to warm up the box prior to startup. Soon after startup, an oil sample was obtained along with a reference sample from an open drum. The oil analysis results were puzzling:
-
The viscosity reading in the gearbox was too high compared to the reference sample taken from the drum.
- The phosphorus reading (a primary component of the EP additive) was also too high compared to the reference sample.
A second sample was taken from the gearbox to verify the lab results of the initial sample. The results of the second sample were even more out of line from the baseline than the first, with an even higher viscosity, 324 cSt at 40°C, which indicates an ISO 320 oil. Also, the phosphorus reading was critically low. The only answer the laboratory could provide was that an incorrect oil was being used in the system. A partial drum of the oil in question was located onsite and sampled for comparison to the gearbox results. Fourier transform infrared analysis of the sample to the oil in the gearbox was almost identical.
Further Investigation
The in-house chemistry lab supervisor suggested locating the empty drums for the dates and batch number information so the refinery could be contacted. Unfortunately, the drums could not be located.
When the oil supplier was contacted to obtain this information, they admitted the oil had been repackaged because the original drums were in bad condition and had been sitting onsite for some time. They said they would be in touch with the batch number. An engineer from this same oil supplier in charge of a different region was also contacted for some insight. He stated that their products generally have a shelf life of three years, and any oils over that age should be fully tested before being placed in service.
An employee recalled that an additional order of ISO 220 oil had been sent to the cold mill oil cellar by mistake and was returned back to the warehouse for storage. These drums were labeled only with the supplier’s company tag and a product name sticker. No batch number or date was displayed. A sample was taken from each of the eight drums in storage to determine whether the oil was at fault. These were tested by both the commercial and in-house laboratories for viscosity. Only one of the eight drums came close to the correct viscosity readings of ISO VG 220.
Problem Resolved
The oil supplier contacted the facility that afternoon and stated that they did not have the batch numbers, but the oil had originally been packaged between 1991 and 1993 – at least 12 years old. Additionally, personnel discovered that the gearbox manufacturer recommended an AGMA grade 6, ISO 320 oil, not an ISO 220 oil. The supplier was asked to review the results of the eight drums sampled. They explained that at the time the drums were repackaged, some oils had gotten mixed up in the process.
The supplier agreed to replace the 12 drums needed for the gearbox and the eight drums located in the warehouse storage area. They also agreed that the facility would not accept any drums that did not have the original label affixed, batch number and date filled, or any drum over three years old. Finally, all new drums would be checked for viscosity readings prior to being accepted.
The issue of the reduced phosphorus mentioned earlier was also discussed. At the time the batches of oil were formulated, a dry powder additive was mixed into the base oil instead of a liquid that is currently used in the blending processes. There is a possibility that the filtering process may have caused this reduction of phosphorus level, but only if it was filtered down to a one to two-micron range. The filters used are in the nominal three-micron range. It is also possible that the solid undissolved additives settled out of the oil after sitting in storage for an extended period of time.
Lesson Learned
End-users play an important role in the quality of lubricants they receive, and lubricant deliveries are a significant part of the overall lubrication program. Be alert about the possible problems in new oil deliveries. Ensure quality by asking your oil supplier for a certificate of analysis and consistently inspecting new oil deliveries. Also, question and verify by documentation all lube recommendations your oil supplier may suggest.
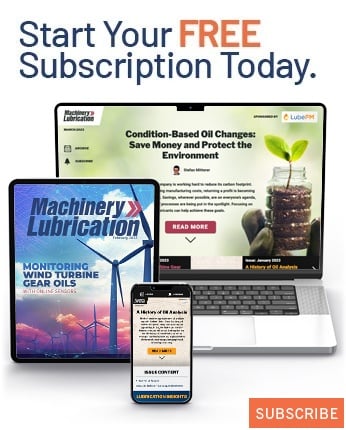