Designing a best-practice lubricant storage and dispensing room is one of the first steps in achieving lubrication excellence.
Several readers met the challenge of transforming their lubricant dispensing methods to best-practice. Here is one such company who has achieved a world-class lube room.
Since 2003, John Hyser has worked to upgrade the lube rooms in the Coors facility where he is employed. Through its vendor partnership program with ChevronTexaco, Coors is attempting to achieve a world-class lubrication program, beginning with lube storage and handling.
In striving to improve the lube room to adhere to best practices, Hyser implemented numerous changes to existing equipment and applied additional changes allowing for quality and easily understood regulations pertaining to the items in the Coors lube room.
Some of these changes included improving the wall tank system, changing oil containers and funnels, providing display sample liquids and used gearboxes for practice, displaying an information board and factory map, and constructing a master lube identification tag station and lubrication list.
Out With the Old, In With the New
In the packaging area, the wall tank system did not adhere to best practices due to cross-contamination issues. The old tanks had been in place for more than 20 years and a considerable amount of sludge had built up in the bottom of each tank. Hyser and his team worked to install desiccant breathers and new tanks as well as separate pumps, transfer hoses and drum stingers along with quick-connect couplings where needed. The improved wall tank system is shown in Figure 1.
Figure 1. Improved Wall Tank System
Before implementing the upgrades, Hyser was using plastic one-gallon jugs due to the low cost, and was supplying the jugs to others in the plant at no cost. During an audit, Hyser found more than 30 plastic jugs on one packaging line that were being kept in locations where possible contamination could occur. Hyser decided to follow a trend that was already occurring in the Coors plant and switched to the Oil Safe lube containers.
Packaging teams now have to purchase the containers from the in-plant storeroom, therefore budgets do not allow for excess containers around the lube room. The containers are now kept in one specific area, with covers over the grease gun tips and container spouts (Figure 2), and are no longer left out on the equipment or in unsafe areas.
Figure 2. Tips of Grease Guns
and Containers are Covered
Another handling improvement made was to use disposable paper funnels and latex or vinyl gloves for oil handling use (Figure 3). Hyser felt this improvement was necessary because the practice of avoiding contaminating the metal funnels by storing them in plastic bags was not being strictly followed by plant personnel, and funnels were found covered in dust, rust, broken glass, etc.
Figure 3. Clean Disposable Funnels
Replace Metal Ones
Practice Makes Perfect
A discarded gearbox has been set up in the lube room for oil sampling practice. Mechanics and operations personnel can now practice drawing an oil sample, through either the sample port or drop tube method, in a safe environment free from distraction. Even the practice sampling equipment is kept in plastic baggies (Figure 4), which promotes the importance of avoiding contamination.
Figure 4. Oil Sampling Practice Station
Clean samples of the different oils used in packaging are also displayed, allowing operations personnel to view the correct ways the oils should appear in the sight glasses on their equipment (Figure 5). If the samples are not completely filled, it is also possible to gain an assumption concerning the viscosity.
Figure 5. Examples of How Oil Should
Appear in Sight Glasses
Master Lube List and Lube Identification Tags
Hyser set up the Coors master lube list ID tag station that contains tags for the different oils and greases used in packaging. Tags are prepunched and cable ties are available for easy attachment to secondary lube containers, grease guns or equipment. Health hazard tags are also available. The 5-S placard on the wall demonstrates how to locate the information needed to fill out the hazard tags.
Other posted information includes why identification tagging is important and why oil-safe containers are being used. The master lubricant list is posted in the lube storage area.
After the ID tag has been attached to the equipment, all the user needs to remember is the “black box” number when procuring the lubricant. This eliminates possible confusion concerning which lubricant to use. All grease kegs, oil tanks and drum pumps in the lubricant storage area are tagged with similar tags that are already on the equipment. Therefore, the user can identify which lubricant to use. The lube list also indicates which areas use a particular lubricant and the equipment it is used in.
Entering the Lube Room
Upon entering the lube room, Hyser has posted a 5-S, visual factory map of the lube room, which provides a diagram of what lubricants are used and where they can be located (Figure 6).
Figure 6. Map of Lube Room Poster on Door
Last but not least, Hyser asked himself “what lube room would be complete without an information board offering good advice and tips on best practices?” Therefore, Hyser has designated a large wall area in the Coors lube room that displays tips and articles that people can also use at home.
Coors is still ID tagging its equipment and lubricant dispensing equipment to ensure the correct product goes into the appropriate machine. They are using 5-S and visual factory enhancements for organizational purposes. Hyser and his team frequently meet to discuss lube issues and the lubrication best practices committee regularly updates the master lube list as new lubes are added or old lubes are no longer used. The Coors master lube list is used in the Golden, Memphis and Shennandoah plants.
Clopay
After winning the 2003 Lube-Room Challenge, Clopay’s lubrication program has gained world-wide recognition. Scotty Lippert, the planned maintenance technical and lubrication systems leader, was interviewed, questioned and visited by dozens of companies wanting to learn how this world-class program worked. Since 2002, Clopay hasn’t rested on its laurels.
They’ve continually improved their lubrication program and are now the model plant for other Clopay plants. Scotty was gracious enough to send us some updates revealing more lubrication-related modifications and improvements his team has made (Figures 7,8,9).
Figure 7. Fast-disconnects are attached for
filling and draining with stainless locking
ball valves, colored ID tags, sight glasses
and labels.
Figure 8. Cart on wheels is stocked with
only stainless-steel pipe and fittings
for accessorizing gearboxes.
Figure 9. Colored Label with Written
Description, Sight Gauge and Oil Sample
Port Combination.
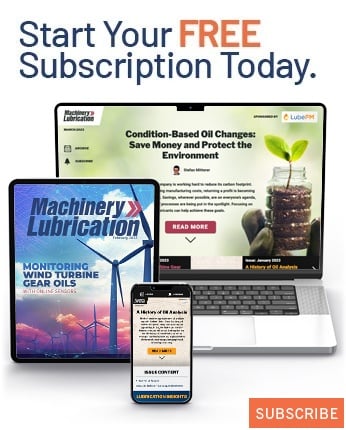