When the maintenance department at Rio Tinto Energy America’s (formerly Kennecott Energy) Antelope coal mine needed a new lube truck, they decided to take a different approach: designing their own. The result was a highly efficient truck that maintains high-quality lubricant cleanliness.
The old lube truck, typical for mining
operations, did not provide much
opportunity for contamination control.
A typical mining lube truck: all
equipment is exposed to the elements.
Teamwork
The truck was designed by a group of approximately 10 employees, including mechanics, lubrication technicians and engineers. With a $300,000 budget, the team was under tight restrictions, but managed to accomplish their task under budget. Rich Wilson, master mechanic who was vital in the design of the truck said, “Those who use it should be the ones to figure it out.”
In the new lube truck, dispensing is directed away
from the dust cloud created by the rear wheels.
Lubrication technicians work in adverse environmental conditions around the clock to ensure mining equipment is serviced according to plan. Along with equipment operators, technicians provide the first line of defense against equipment failure. Often working in subzero temperatures at night, these unsung heroes keep the wheels and gears turning. The team at Antelope coal mine shows pride in the work they perform each day.
Reaching Goals
The lubrication excellence team set out to accomplish two goals. Initially, they wanted to clean up the bulk storage units to guarantee clean lubricants are delivered to the preventive maintenance (PM) bay and the field lube trucks. Second, the team wanted to ensure the delivery of clean lubricants to equipment in the field via lube trucks.
To begin the process of cleaning up the lubricants, reliability engineer Danny Sparling designed a filtration system for the bulk lubricant storage compartments. A kidney loop pump with a five-micron filter was put in place with cross-tank suction and return lines. Engine oil samples were taken before and after the filtration system was implemented. ISO numbers before filtration were 22/19/12. After filtration the ISO dropped to 17/11. Cleaning up the bulk-stored lubricant was imperative to extend engine life. The first goal of the lubrication team was complete.
The Design
The process of designing the truck took approximately six months. Craig Softley, maintenance planner, said, “We sat down to collaborate ideas five or six times before placing the final order.”
The new lube truck is ready for service.
The old lube trucks were built with the lubrication compartments located on the back of a flatbed truck where the hoses were often subjected to the dirty mining environment. The new truck incorporated a “house” design that would protect the lubricants from the elements.
The truck is designed to hold the major lubricants used in modern heavy mining equipment. Antifreeze, 15W40, 30W, 50W, two compartments for used oil and a grease compartment line the walls of the truck’s house. A translucent roof was installed to improve visibility.
A pressurized reel compartment was mounted to ensure warm air is pushed out of the compartment, limiting the entrance of dirt and dust. Hose reels were kept on the back of the old truck, and the team found this caused “boiling dust” from the rear wheels. On the new truck, the hose reel was moved to the side in the front, away from the rear to avoid road dust. In addition, filters were installed before every hose reel, resulting in final/endpoint filtration.
Mining is a dirty and dusty environment, and controlling outside contamination is difficult. The team requested two-micron beta-rated air filters be installed on each of the storage compartments. Initially this was believed to be adequate, but after several days of operation, coal dust and other contaminants were found deposited near the breathers on top of the storage tank.
Investigations found the source of this contamination was coming through door seals and other small openings on the body of the truck. A positive vent was added with a high-efficiency particulate filter to limit ingress of contaminants.
Employee Satisfaction
The improvements are not limited to clean lubricants. The group who designed the truck have a personal commitment that is exhibited in their work. Wilson said, “The guys are proud of these trucks. They take care of them.”
Lube technician Rod Erickson, who has worked at Antelope for two and a half months said, “I really like the ride. It’s smooth and has plenty of power coming out of the pits.”
Wes Meeks has been employed at Antelope since 1999 and was promoted to lube technician three months ago. The biggest change he noticed was the addition of lube technicians to each crew. The technicians shadow each other to ensure every piece of equipment is serviced. “It’s efficient in the field when it’s time for PMs,” Meeks said.
Wilson, Erickson and Meeks agree that if the truck was redesigned, they would make one addition. “If we had to go back, the one thing we would change is designing the truck to have the capacity to carry fuel,” Meeks said.
Clean Lubricants
A properly designed lube truck ensures clean lubricants are delivered to equipment in the field. Results of samples taken off the truck at the dispensing outlets are shown in Table 1. In the case of the 15W-40 oil, cleanliness was maintained and the hydraulic fluid actually got cleaner.
Table 1. Cleanliness at Dispensing Outlets
Clean lubricants mean longer component life resulting in lower operation costs. This is the part of the competitive edge that makes mines profitable.
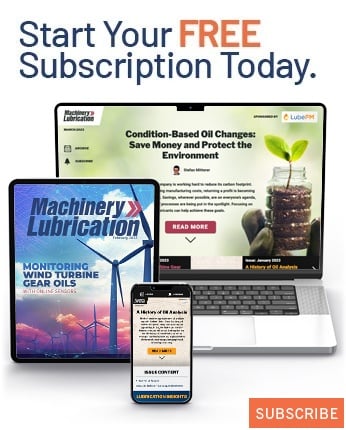