Designing a best-practice lubricant storage and dispensing room is one of the first steps in achieving lubrication excellence.
Several readers met the challenge of transforming their lubricant dispensing methods to best-practice. Here are a couple of the "Honorable Mentions" who have achieved a world-class lube room in their facilities.
Green Triangle Forest ProductsPaul Brooker, condition monitoring coordinator at the Green Triangle Forest Products plant, uses colored stickers to organize the equipment in his lube room in efforts to diminish the cross-contamination of oils. Brooker has attached colored stickers to each gearbox on-site and has coordinated oil containers to display the same color as the gearbox in which is it used(Figure 1).
Figure 1
FordIn 1992, at the Ford Cleveland engine plant No. 2 in Cleveland, Ohio, Paul Babyak and his team designed and constructed an oil room in conjunction with the Duratec V6 engine program. There are seven color-coded 660-gallon totes that store five bulk lubricants used in the plant. These are mounted on standard tote stands where a complete pump station has been added (Figure 2).
Figure 2
The totes are filled through six hose reels placed outside the building in a closed compartment and piped to the top of each tote. Additionally, each tote is equipped with a three-micron air breather and an ultrasonic fluid level detector, as shown in Figure 3. The ultrasonic detector is wireless and has a range of approximately 100 feet from the base station, which is located in the oil room.
Figure 3
The Ford plant has eight lube trucks which are filled by driving them into the oil room directly to the oil-dispensing hose reels. What is unique about this system is the installation of a credit card-type dispensing unit similar to pumps at gas stations (Figure 4).
Figure 4
Once the desired lubricant has been selected, the corresponding hose reel nozzle is connected to the appropriate quick-disconnect fitting on the oil truck reservoir (Figure 5). Each lubricant has a unique quick-disconnect fitting to prevent cross-contamination of lubricants.
Figure 5
In addition, Ford Cleveland engine plant No. 2 has a small side room where gear oils and miscellaneous lubricants are stored. All of the gear lubes are purchased in five-gallon pails to reduce waste in an attempt to make this oil room world-class.
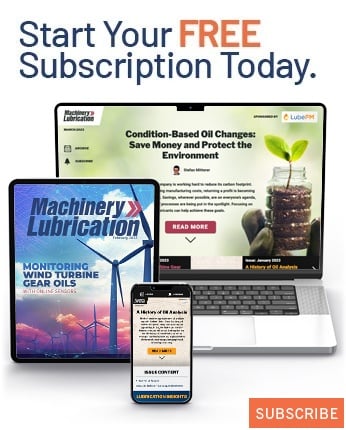