One of the most common questions I'm asked when teaching lubrication courses is "are synthetics any good?" Oftentimes, the basis for this is question is a specific machine or group of machines, where a conversion from mineral to synthetic has either recently occurred, or is being planned. In doing so, the questioner is looking for validation of a decision that he or she has made, or advice on whether such a change is warranted for machines currently using a conventional mineral-based lubricant.
No Magical Solution
First, let's set the record straight. No lubrication problem due to poor system design, poor PM practices or lack of fundamental contamination can be solved by the use of synthetics. The notion that selecting a different lubricant can some how magically make up for under- or overgreasing, inattention to lubricant condition or an inadequate breather or filter is fundamentally flawed. But for those machines where these issues have largely been resolved, are synthetics truly better? The answer to the question is - "it depends".
For those dissatisfied with this apparent cop-out, let's look at the facts. For machines to run at optimum performance, they require the lubricant to provide certain fundamental performance properties. In addition to separating moving surfaces to prevent wear, these include minimizing internal friction, preventing corrosion, resisting breakdown due to high localized or bulk operating temperatures, removing or suspending contaminant such as soot or water, and in a hydraulic system, providing the force necessary for motive power.
![]() |
|
|
Ultimately, these fundamental performance properties can be related back to the chemical and physical properties of the oil: properties such as viscosity and viscosity index, wear prevention (for example, four-ball wear testing), oxidation resistance, foaming tendency and demulsibility. In selecting a lubricant properly, the diligent lubrication engineer carefully examines the design and operation of the machine (bearing type, speed, load, operating temperature, etc.) and decides the minimum performance requirements for a given machine under these "normal" machine operating conditions.
So the question becomes not whether a synthetic is any better than the equivalent mineral oil, but rather, which lubricant provides the best overall combination of performance properties, based on the assessment criteria?
There are numerous applications where synthetic lubricants can and should be used. But in each instance, it is because the available mineral oil-based lubricants from which the plant has to choose are not able to meet the prescribed physical, chemical or tribological requirements for the machine in question.
Pros
Needless to say, synthetic lubricants provide an array of improved performance in certain key areas. These include generally better oxidation resistance, which can translate into longer life; higher flash or fire points, important in high-temperature and fire-resistant applications; better cold-temperature fluidity, important where low-temperature start-ups are required; and in some cases, lower internal friction, which can result in lower energy consumption and better natural solvency, helping to prevent the formation of deposits.
Cons
But synthetics also have some drawbacks, the most obvious of these being costs. Depending on the type of base stock, the cost for a synthetic lubricant may be anywhere from three to several hundred times the cost for the equivalent grade and class of mineral oil. Because many synthetics are made from raw materials extracted from crude oil, their cost is no more or less immune from increases due to increasing crude oil prices.
But cost isn't the only downside. Some synthetic lubricants such as certain types of phosphate esters are hazardous, requiring special care and attention when handling and disposing. Yet others have a limited ability to dissolve additives, making formulation and additive suspension under less-than-ideal conditions difficult, while yet others are incompatible with petroleum-based products, requiring care and attention when storing, handling and dispensing. And increased solvency is not always a good thing - particularly when a mineral oil has been in use for some time and the removal of deposits can result in seal leaks.
Figure 1. Advantages and Disadvantages of Synthetic Lubricants
So you see, it really does depend. If you require one or more of the enhanced performance properties listed in Figure 1, and that property cannot be met by a conventional mineral oil - even a premium product - then you really have no choice but to use a synthetic. But if you can achieve the level of performance required with a mineral oil, chances are, cost or one of the other downsides with synthetic lubricants listed above makes a mineral oil a much wiser choice.
As always, this is my opinion. I'm interested in hearing yours.
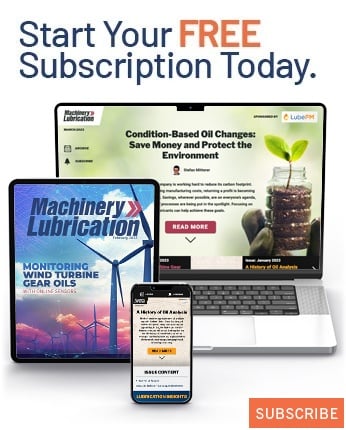