The vibration data acquired on a small helical gearbox with three shafts supported by tapered roller bearings indicated symptoms consistent with impending bearing failure. The vibration pattern that helped to identify the problem as lubrication-related is discussed in this article.
Fault Frequencies
Both inner and outer race bearing faults were present in the spectrum (Figures 1 and 2). Random impacting of high magnitude was indicated in the time waveform (not shown). An alarm showed that lower-order harmonics dominated the spectrum, and their magnitudes suggested bearing fault in an advanced stage.
Figure 1. Harmonics of inner race bearing defect frequency M=BPFI.
Figure 2. Harmonics of outer race bearing defect frequency L=BPFO.
Figure 3. Noise modulating by bearing cage frequency J=FTF.
The modulation of a random signal by the cage frequency was also observed in the PeakVue data (Figure 3). It has been theorized that due to dry operation, both the inner and outer races wore out to a point that the round geometry of the races had been compromised. In addition, insufficient lubrication caused increased friction between the rollers and the cage. Because of being subjected to modulation by the cage, friction became apparent in the PeakVue data.
After removing the gearbox from operation and disassembling it, the entire space in the gearbox filled with grease, used mainly in open gears, but the lubricant was completely washed out from the bearing areas (Figure 4).
Figure 4. Grease has been washed out from the bearing areas. Bearing outer races are unevenly worn out.
Results of Metal Wear
The diagnosis was confirmed by observing the damage sustained by the input shaft bearing. Extensive wear was present in the outer race (Figure 5). A rough surface was not the only result of the metal wear. A groove up to 0.015-inch deep also developed in the path of the rollers.
Figure 5. A groove up to 0.015-inch deep is present in the outer race.
The inner race exhibited a similar pattern (Figure 6). No pitting or spalling was observed on the surface. The cage was also excessively worn out and broke off in several locations. This, along with the smaller inner-race diameter, compromised the separation of the rollers (Figure 7).
Figure 6. Worn surface on the inner race. A groove developed in the path of the rollers.
Figure 7. Cage is damaged. No lubricant is present.
An observant reader may ask why grease was used in a gearbox instead of oil. Consider this wintertime scenario: In attempting to warm up the room, you turn up the thermostat instead of shutting the door to retain the heat. Dealing with a symptom instead of the root cause is still a common approach to solving problems.
In this case, the lubrication scheme was designed as an oil splash-type, but over time, the shaft seal started to leak. To prevent oil from escaping, lubricant flow properties have been adjusted for the leaking seal by draining the oil and filling the entire space of the gearbox with grease.
While there was some grease still left in the bearing area, it operated almost satisfactorily, possibly slightly hotter, than normal. But once the initial charge was depleted, the lubricant could not be delivered, even with the excess grease in the gear casing. The same is true for the lubrication of the gears.
Making lubrication modifications without considering the lubrication scheme could be detrimental to you and your equipment.
About the author:
David Gluzman is a Certified Reliability Engineer (CRE) with Temple-Inland Corporation, a manufacturing company focused on corrugated packaging and building products. Gluzman also holds Machine Lubrication Technician Level I and Level II certifications through the International Council for Machinery Lubrication.
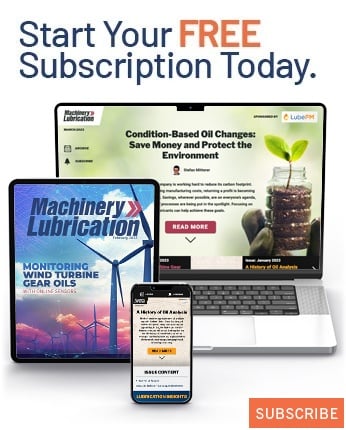