Petroleum base mineral oils have some limitations, depending upon the type of base stock used, the level of additives blended, and the operating conditions encountered. The main service difficulties within mineral oils are:
-
The presence of waxes, which can lead to poor lubrication at low temperature.
-
Poor oxidation stability at continuously high temperatures, which can lead to sludge and acid buildup.
-
The dependence of viscosity on temperature, which can cause the base oil to thin excessively at high temperature.
-
A natural high temperature application limit of about 320°C (608°F), above which the base oil decomposes and begins to coke (turns to a sooty substance). Under severe operating conditions, such as extremely high temperatures, or in very cold operating climates, the difficulties noted above are important factors in the selection of lubricants. Very often, the only solution is the selection of a synthetic oil.
Examples of the effective use of synthetic oils are described below:
Conventional and Synthetic Oil Case
A northern Canadian diesel truck fleet was experiencing cold starting difficulties at temperatures that were consistently below -25°C (-13°F). Another critical problem was that once started, it took a minimum of 1:45 (one minute, forty-five seconds) for the petroleum base SAE 15W/40 oil to provide full flow lubrication and fully 3:15 (three minutes, fifteen seconds) for a petroleum base SAE 30 oil to fully lubricate the rocker arms of the engines.
The solution was the use of a partially (50%) synthetic lubricant with an SAE 0W/30 viscosity and an API service classification of SF/CD. Cold starting is no longer difficult, full pressure lubrication is achieved within .20 (twenty) seconds, and at operating temperatures, the oil viscosity behaves much like an SAE 30 grade lubricant.
Petroleum Base Oil vs Fully Synthetic Oil
A construction equipment contractor was experiencing premature turbocharger failures when certain engines were operated under full load conditions and used around the clock. Investigation through oil analysis and diagnosis of the failed components revealed that the failures were caused by coking of the petroleum base oil within the turbocharger oil passages, thus restricting oil flow and resulting in bearing failure.
The initial cause of the oil coking condition was excessive temperatures within the turbocharger housing.
A fully synthetic diesel engine oil was selected of the same viscosity as the original conventional oil and installed. Premature turbocharger failures did not reoccur and oil operating temperatures dropped by about 8°.
A heavy truck fleet was experiencing high fuel costs in combination with what it felt was premature differential gear and bearing failures, using a good quality 80W/90 gear lubricant. Field testing with a semi-synthetic gear lubricant with a wider viscosity range of 75W/90 reduced the failure rate and provided a fuel economy improvement of over 3%.
These are just a few examples of how synthetic oils may solve a problem in transportation or heavy equipment. Examples of the use of synthetics in industrial equipment can be found in Chapter 22 of The Practical Handbook for Machinery Lubrication.
The most difficult decision to make, and one which requires great care, is how to choose a synthetic lubricant.
Synthetic lubricants are made from a number of different chemical bases, and several classes of compounds have been developed to provide base fluids for commercial synthetic lubricants, among them;
1. Alkylated Aromatics
2. Olefin Polymers
3. Dibasic Acid Esters
4. Neopentyl Poly Esters
5. Poly Glycols
6. Phosphate Esters
7. Silicones
8. Silicate Esters
9. Fluoro Carbons
10. Poly Phenyl Ethers
This is an excerpt from The Practical Handbook for Machinery Lubrication.
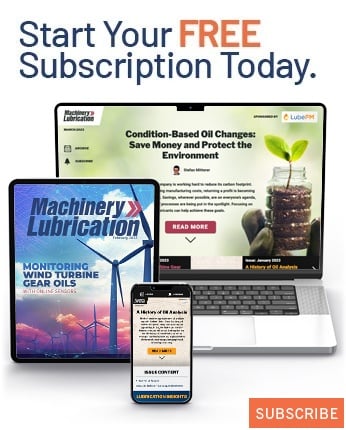